今こそ物流現場に5S活動の徹底を。具体的な効果や実践イメージ、成功に向けた6つのステップ、秘訣を解説
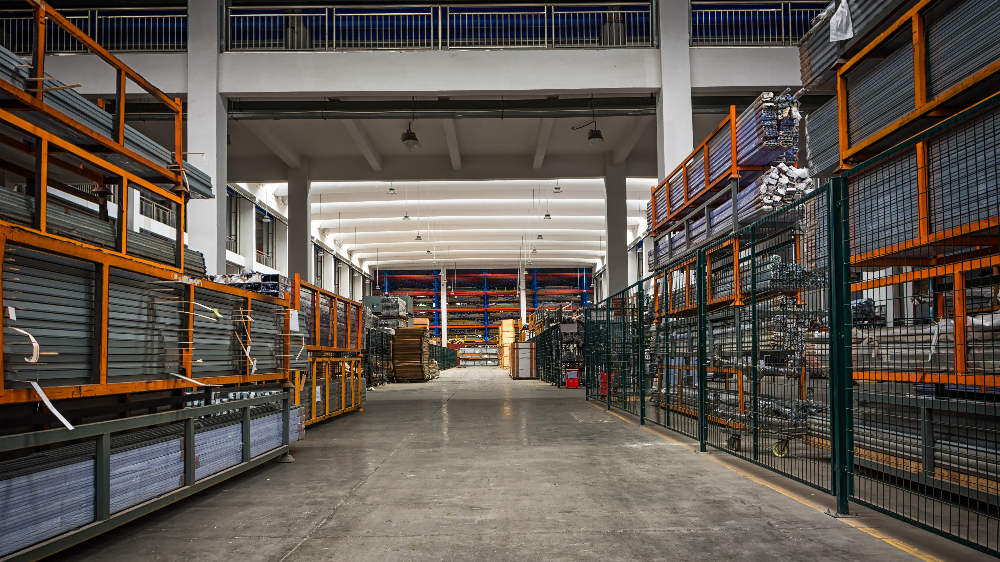
物流を取り巻く環境は、深刻化するドライバー不足や度重なる法規制、物流コストの上昇など、日々変化し、その厳しさを増しています。このような状況下で、物流業務の効率化は、企業の競争力を維持・強化するための喫緊の課題と言えるでしょう。
多くの企業がDX(デジタルトランスフォーメーション)や自動化といった先進技術の導入を検討する一方で、それらの効果を最大限に引き出すためには、まず足元の「現場力」を高めることが不可欠です。その最も基本的かつ効果的な手法が、「5S活動」です。
本記事では、物流現場における5S活動の基本から、具体的な実践方法、期待される効果、そして活動を成功させ定着させるための秘訣について、物流DXパートナーのHacobuが解説します。
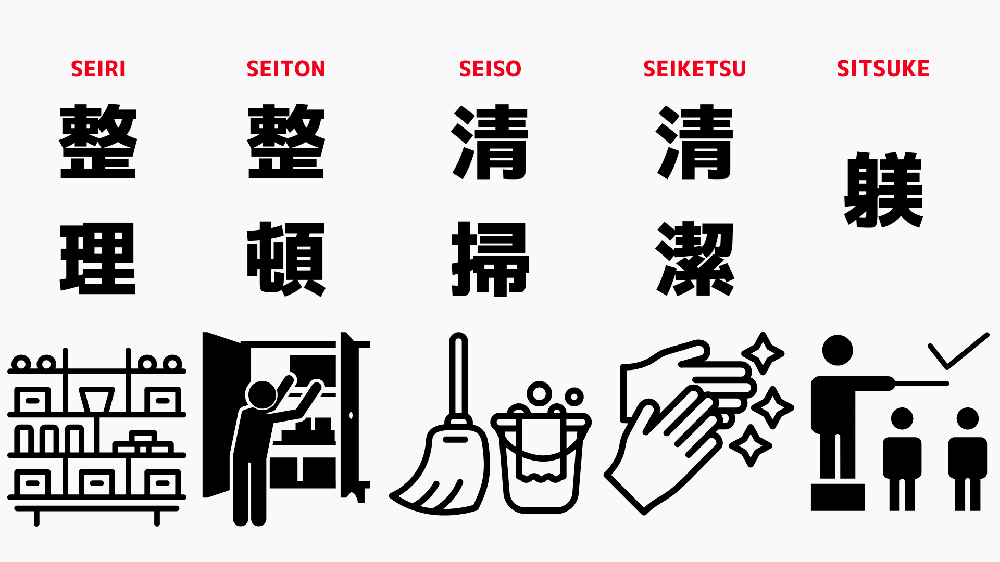
目次
- 1 5S活動とは
- 2 なぜ今、物流現場で「5S活動」が改めて注目されているのか?
- 3 物流現場における5S活動の基本と、具体的な実践イメージ
- 4 物流5S活動がもたらす具体的な効果
- 5 物流現場で5S活動を成功に導く!導入から推進までの6つのステップ
- 6 5S活動を「一過性のイベント」で終わらせない!継続・定着化のための秘訣
- 7 5S活動は、変化に強く持続可能な物流体制を築くための第一歩
5S活動とは
5S活動とは、「整理(Seiri)」「整頓(Seiton)」「清掃(Seiso)」「清潔(Seiketsu)」「しつけ(Shitsuke)」の頭文字Sを取った職場改善のための活動のことです。これら5つのSを順番に、かつ継続的に実践することで、職場環境の維持・改善を図ります。
なぜ今、物流現場で「5S活動」が改めて注目されているのか?
「5S活動はもう聞き慣れている」と感じる方もいらっしゃるかもしれません。しかし、その本質的な重要性は、時代の変化とともにむしろ高まっています。なぜ今、改めて物流現場で5S活動が注目されるのか、その理由を深掘りしてみましょう。
物流パートナーの「現場力」の重要性
荷主企業として、自社製品の安定供給と顧客満足度を維持・向上させるためには、委託する物流パートナーの選定が極めて重要です。運賃やその他の料金だけでなく、配送品質、リードタイムの遵守、柔軟な対応力、法令遵守、運行管理におけるガバナンスなど、物流パートナーに求めるサービスレベルは年々高まっています。
信頼できる物流パートナーは、日々のオペレーションを支える「現場力」が高いレベルにあるのではないでしょうか。その現場力を測る一つの指標が5S活動の徹底度です。物流パートナーの現場で5S活動が徹底されていれば、ムダ・ムラ・ムリが排除され、高品質で効率的な物流サービスが期待でき、結果として自社の競争力強化にも繋がります。また、自社の物流部門においても、5S活動は業務品質向上の基礎となります。
物流コストの最適化と収益構造改善への貢献
燃料費の高騰、人件費の上昇、さらには環境対応に伴うコストの増加など、物流コストは常に上昇圧力にさらされています。荷主企業にとって、これらのコストは製品価格や収益性に直接影響します。
5S活動を自社物流部門で徹底することはもちろん、委託先である物流パートナーの現場で推進・徹底されることで、作業時間の短縮、誤出荷の削減、在庫管理の精度向上、スペースの有効活用などが実現します。
これは、荷主企業にとって委託コストの適正化や、自社のトータル物流コスト削減に繋がり、収益構造の改善に大きく貢献します。
働きがいのある職場環境づくりと人材定着への効果
5S活動を通じて物流現場の環境を整備することは、従業員の安全確保はもちろん、働きやすさや快適性の向上にも繋がります。働きやすさや快適性の向上は、人材の定着率向上に貢献し、結果として経験豊富な人材による安定した物流サービスの提供、ひいては自社製品の安定供給というメリットに繋がります。
DX推進や自動化を成功させるための基盤整備
多くの荷主企業が、サプライチェーン全体の効率化を目指し、自社の物流拠点や物流パートナーにDXや自動化への対応を促しているでしょう。しかし、これらの最新技術も、物流現場が整理整頓されていなければその真価を発揮できません。
たとえば、自動倉庫やAGVを導入する際、その前提として5S活動による物理的な環境整備が不可欠です。5S活動の徹底は、先進技術導入をスムーズにし、より高度で効率的な物流サービスの提供を可能にする基盤となります。
物流現場における5S活動の基本と、具体的な実践イメージ
本章では、物流現場における5S活動の基本と、具体的な実践イメージを解説します。
【整理】不要なモノを徹底的に見極め、処分する
「整理」とは、必要なモノと不要なモノを明確に区分し、不要なモノを処分することです。自社の大切な製品が、倉庫で不要なモノに埋もれ、スペースを圧迫したり、品質劣化のリスクに晒されたりすることを防ぐための第一歩です。
実践例:長期動きのない在庫(デッドストック)のリストアップと廃棄判断
倉庫に保管している自社製品の中に、長期間動きのないデッドストックはないでしょうか。定期的な棚卸しを通じてこれらをリストアップし、廃棄などの適切な処分方針を決定・指示することが重要です。
実践例:破損・劣化したパレットや梱包資材の定期的な処分
倉庫で使用されるパレットや梱包資材が破損・劣化していると、自社製品の汚損や破損の原因となりかねません。これらの定期的な点検と速やかな処分、または良質なものへの交換を求めることも重要です。
実践例:使用頻度の低い古い伝票や書類の電子化と廃棄
保管義務のある伝票や書類を除き、参照頻度の低い過去の書類は、可能な限り電子データ化し、原本は適切に廃棄・ペーパーレス化することで、倉庫内のスペース効率向上に繋がります。
実践例:「赤札作戦」による一時的な不要品置き場の設置と、その後の処理ルールの明確化
「これは不要かもしれないが、すぐに判断できない」というモノ(たとえば、旧型の販促物やサンプル品など)に「赤札」を貼り、一時的な保管場所に集めます。一定期間経過後に必要ないと判断したものは処分する、というルールを設けることで、段階的に整理を進められます。
【整頓】必要なモノを「誰でも、すぐに、安全に」取り出せる状態にする
「整頓」とは、必要なモノを、決められた場所に、決められた向きで、使いやすく、かつ安全に配置することです。倉庫における誤出荷を防ぎ、必要な時に必要な製品を確実にお届けするための基本です。
実践例:工具や備品の定位置管理
倉庫で製品の取り扱いに使用されるパレットやカゴ車、ハンディターミナルなどの備品が適切に管理されているかを確認することが重要です。これらが定位置に置かれ、常に使用可能な状態にあることは、作業効率と安全性を高めます。
実践例:在庫ロケーションの3定管理とロケーション番号の付与
製品が倉庫のどこに、何が、いくつ保管されているか(3定管理)が正確に管理されていることは、在庫管理の基本です。ロケーション管理が徹底されていれば、WMS(倉庫管理システム)との連携もスムーズになり、リアルタイムに近い在庫情報を把握でき、欠品や過剰在庫のリスクを低減できます。
実践例:通路や作業エリアのライン表示
倉庫内の通路が明確に確保され、安全な作業動線が引かれていることは、製品の安全な取り扱いと作業者の安全確保に不可欠です。
たとえば、ゼブラゾーンや歩行者通路を明確に区分し、フォークリフト動線と交差しないように整備することで、接触事故の防止や作業効率の向上が期待できます。
実践例:製品特性基づいた、効率的な商品配置
自社の製品特性(出荷頻度、重量、サイズなど)を考慮した上で、倉庫で効率的な商品配置がなされているかを確認しましょう。出荷頻度の高い製品が取り出しやすい場所に配置されていれば、ピッキング作業の効率が上がり、リードタイム短縮やコスト削減に繋がります。
【清掃】ゴミや汚れがない状態を保ち、異常を発見しやすい環境を作る
「清掃」とは、職場や設備を常にキレイな状態に保つことです。荷主企業にとっては、自社製品が保管・作業される環境が清潔であることは、製品の品質維持(特に食品や精密機器など)や、異物混入リスクの低減に不可欠です。
実践例:床面、棚、コンベア、作業台などの定期的な清掃と点検
委託先倉庫の床面や棚、製品が触れる可能性のあるコンベアや作業台が定期的に清掃されているかを確認しましょう。これは、製品へのホコリや汚れの付着を防ぐ基本です。委託契約に清掃基準を盛り込むことも検討しましょう。
実践例:フォークリフトや運搬台車などのマテハン機器の日常的な清掃とグリスアップ
製品を運搬するフォークリフトなどが清潔に保たれているか、また、油汚れなどが製品に付着するリスクはないかを確認しましょう。これらのマテハン機器の清掃状況も、製品品質に関わる重要なポイントです。
実践例:「清掃=点検」と捉え、微細な変化にも気づける観察力を養う
委託先の作業員が、清掃を通じて製品の軽微な異常(梱包の小さな破れ、濡れなど)にも気づき、報告する体制があれば、品質問題の拡大を未然に防ぐことができます。また、清掃を通じて設備の不具合(油漏れ、異音、破損など)が早期に発見され、速やかに修理される体制が整っていることは、突発的な作業停止リスクを減らし、製品の安定的な出荷に繋がります。
【清潔】整理・整頓・清掃(3S)を維持し、誰が見ても分かりやすい状態を標準化する(常に高い物流品質を期待するために)
「清潔」とは、整理・整頓・清掃(これらを合わせて3Sと呼びます)の状態を維持し、さらにそれを徹底・標準化することです。荷主企業にとっては、委託先倉庫が常に高いレベルの3Sを維持し、安定した物流品質を提供してくれることへの期待に繋がります。
実践例:3S状態の維持基準の設定
委託先倉庫が、自社製品の取り扱いに関して、どのような3S状態を「あるべき姿」として設定し、それを現場で共有しているかを確認しましょう。品質管理レベルを測る上で参考になります。荷主・委託先間でも、あるべき姿を写真やイラストを用いて共通認識を持つことも重要です。
実践例:清掃・点検チェックリストの作成と、その実施状況の「見える化」
委託先が、製品保管エリアや作業エリアの清掃・点検をどのようなチェックリストに基づいて行い、その実施状況をどのように管理・共有しているかを確認しましょう。これらの仕組みは、継続的な品質維持に不可欠です。
実践例:良い状態を保っているエリアやチームの表彰、模範エリアの設定
委託先企業内で、3S活動が活発に行われ、従業員のモチベーション向上に繋がるような取り組み(表彰制度など)があれば、それは企業全体の品質意識の高さを示すものと考えられます。
実践例:5S活動マニュアルの作成と、新人教育への組み込み
委託先が、5Sに関する明確なマニュアルを持ち、新人作業員にも徹底して教育していることは、作業品質の標準化と維持に繋がります。
【しつけ】決められたルールや手順を、全員が正しく守る習慣を組織文化として根付かせる
「しつけ」とは、職場で決められた作業標準手順や安全ルールなどを、指示されなくても全員が正しく守り、それが習慣化されている状態を目指すことです。荷主企業にとっては、自社製品が委託先でルール通りに丁寧かつ安全に取り扱われ、安心して物流業務を任せられる信頼関係の基盤となります。
実践例:作業標準書や安全マニュアルの理解と遵守の徹底
荷主製品の取り扱いに関する作業標準書(例:積み付け方法、検品手順など)が委託先で整備され、作業員に正しく理解・遵守されているか、また標準書の定期的な読み合わせやテストが行われているかを確認しましょう。これは、品質事故を防ぐ上で非常に重要です。
実践例:保護具の正しい着用と、指差呼称の習慣化
委託先作業員の安全意識の高さは、労働災害の防止だけでなく、製品の丁寧な取り扱いにも繋がります。保護具(ヘルメット、安全靴など)の着用徹底や指差呼称の習慣化は、その一端を示すものです。
実践例:朝礼や終礼、ミーティングでの5Sに関する意識啓発と情報共有
委託先で、日常的に5Sや品質に関する意識啓発が行われているかを確認しましょう。荷主からの連絡事項(製品仕様変更、キャンペーン情報など)が確実に現場作業員まで伝達される仕組みがあるかも重要です。
実践例:従業員からの改善提案を奨励し、優れた提案は積極的に採用・表彰する制度
委託先が、現場作業員からの改善提案を積極的に吸い上げ、業務改善に活かす風土がある場合、それは継続的な物流品質の向上に繋がる可能性があります。
物流5S活動がもたらす具体的な効果
5S活動は、地道な取り組みの積み重ねですが、その効果は多岐にわたり、荷主企業の物流戦略に大きなメリットをもたらします。具体的にどのような効果が期待できるのか、荷主企業の視点から見ていきましょう。
効果1:在庫管理の精度向上と、それに伴うキャッシュフローの改善
荷主企業は、委託先倉庫での正確な在庫管理により、欠品による販売機会損失や過剰在庫のリスクを低減できます。また、5S活動が徹底された現場では、製品の置き場所が明確になり、数量管理も正確になるため、棚卸差異も大幅に削減されます。これにより、自社のキャッシュフロー改善にも貢献します。
効果2:作業動線の最適化とムダ取りによるスループットの向上
委託先倉庫での5S活動の徹底は、作業員がモノを探す時間や不要な移動を削減し、作業動線を効率化します。これにより、ピッキング、梱包、入出庫といったあらゆる作業のリードタイムが短縮され、スループットが向上します。スループットの向上は、荷主企業にとって、緊急出荷への対応力向上や物流ネットワークの再設計といったメリットに繋がります。
効果3:誤出荷、汚破損、遅延の削減による物流品質の向上と顧客信頼の獲得
荷主企業にとって最も重要なことの一つは、製品を正確に、良い状態で、納期通りに顧客へ届けることです。5S活動が徹底された委託先倉庫では、品番の誤認や数量間違いによる誤出荷、製品の汚破損、作業遅延などが大幅に削減されます。これにより、エンドユーザーからのクレームを減らし、ブランドイメージと顧客からの信頼を確固たるものにできます。
効果4:倉庫スペースの有効活用と、保管効率の最大化による固定費削減
委託先倉庫での整理・整頓は、保管スペースの有効活用を促進します。これにより、荷主企業は、より少ないスペースで効率的に製品を保管できるようになり、保管料という固定費の削減に繋がる可能性があります。また、将来的な物量増加にも対応しやすくなります。
効果5:安全で整理された職場環境による、労働災害リスクの低減
委託先倉庫での労働災害は、作業の遅延や停止を引き起こし、荷主企業の製品供給に影響を与える可能性があります。そもそも、倉庫作業者が労働災害に巻き込まれること自体があってはならず、社会的責任の観点からも荷主企業が主体的に管理・改善に関与すべき領域です。5S活動の徹底による安全な職場環境の実現は、こうしたリスクの低減につながり、荷主にとっても安定した物流サービスの提供を担保する重要な取り組みとなります。
効果6:従業員の改善意識の向上と、主体的な業務遂行の促進
5S活動を通じて、委託先の従業員が自ら問題点に気づき、改善に取り組むようになると、それは物流品質の継続的な向上に繋がります。荷主企業と物流パートナーが、共通の目標(品質向上、効率化など)に向かって協力し合う良好な関係構築にも寄与します。
効果7:企業全体のイメージアップと、対外的な競争力強化
5S活動が行き届いた物流現場を持つ(あるいはそのようなパートナーと協業している)ことは、荷主企業の品質管理体制や危機管理能力の高さを対外的に示すことにも繋がります。これは、顧客や取引先からの信頼を高め、企業全体のブランドイメージ向上、ひいては競争力強化に貢献します。
物流現場で5S活動を成功に導く!導入から推進までの6つのステップ
5S活動を効果的に導入し、現場に定着させるためには、計画的かつ段階的に進めることが重要です。荷主企業が自社物流部門で推進する場合、また物流パートナーに協力を求める場合、それぞれの視点からステップを見ていきましょう。
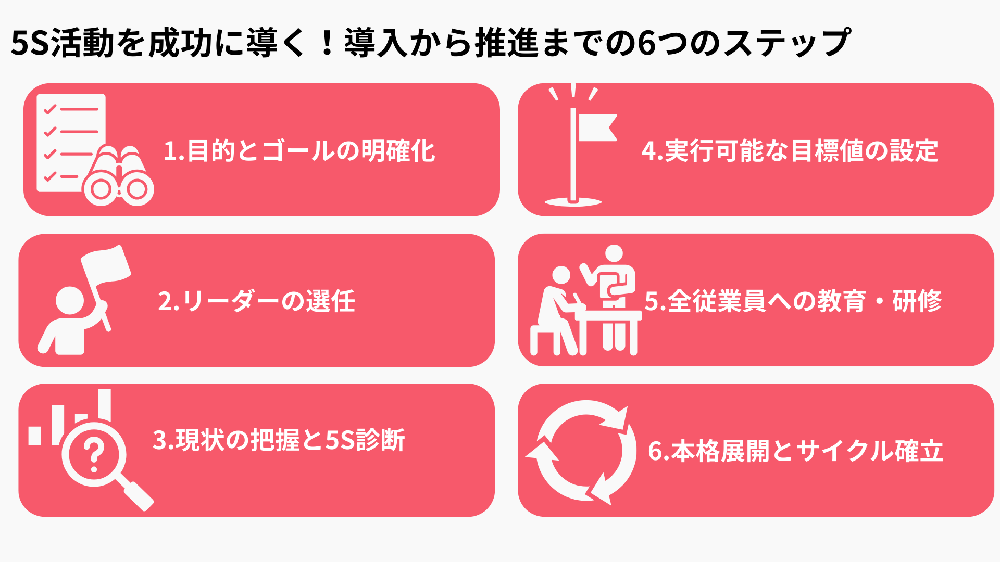
ステップ1:目的とゴールの明確化、部門長のコミットメント表明
荷主企業として、自社物流部門における5S活動の推進、あるいは物流パートナーに求める5Sレベルの目的(例:誤出荷率〇%削減、製品破損率〇%削減、荷待ち時間〇分短縮など)と、目指すべきゴールの姿を明確にします。そして最も重要なのは、荷主企業のCLOや物流部長が5S活動の重要性を理解し、全社的(または委託先との連携において)に推進することを明確にコミットメント(宣言)することです。トップの強い意志が、活動の推進力となります。
ステップ2:推進体制の構築とリーダーの選任、役割分担の明確化
自社物流部門で5S活動を推進する場合は、専門チームや委員会を設置します。物流パートナーに協力を求める場合は、定期的な協議の場を設け、双方の担当者と責任者を明確にします。役割分担(情報共有、課題抽出、改善策検討など)を明確にすることで、活動がスムーズに進みます。
ステップ3:現状の課題把握と5S診断の実施(写真や動画も活用)
自社倉庫の現状把握はもちろん、委託先倉庫を選定・評価する際には、5S活動の実施状況を重要なチェックポイントとします。定期的な倉庫監査や現場確認を通じて、客観的に現状を把握し、課題を洗い出します。その際、現場の状況を写真や動画で記録しておくと、改善前後の比較が容易になり、活動の成果を実感しやすくなります。
ステップ4:具体的な5S活動計画の策定と、実行可能な目標値の設定
ステップ3で明らかになった課題に基づき、具体的な5S活動計画(何を、いつまでに、誰が、どのように行うか)を策定します。荷主と物流パートナーが共同で計画を策定する場合は、双方の役割と責任を明確にします。目標は、測定可能で達成可能なもの(例:3ヶ月後までに特定エリアの整頓レベルを〇点向上させる)を設定し、スケジュールを明確にします。
ステップ5:全従業員への教育・研修と、パイロットエリアでの試行導入
自社物流部門の従業員、あるいは物流パートナーの担当者に対し、5S活動の目的、進め方、期待される効果などについて教育・研修を実施し、意識の共有を図ります。いきなり全体で展開するのではなく、まずは特定のエリアや製品群(パイロットエリア)を選定し、そこで試行的に活動を開始します。試行導入で得られたノウハウや課題点を踏まえ、計画を修正します。
ステップ6:本格展開と、定期的な進捗確認・効果測定・改善活動のサイクル確立
パイロットエリアでの成功体験と改善点を元に、本格的に5S活動を展開します。活動開始後は、定期的に進捗状況を確認し(例:月次でのKPI報告会)、設定した目標値に対する達成度を測定・評価します。荷主と物流パートナーが協力してPDCA(Plan-Do-Check-Action)サイクルを回しながら、継続的な改善に取り組みます。
5S活動を「一過性のイベント」で終わらせない!継続・定着化のための秘訣
多くの企業で5S活動が導入されますが、残念ながら途中で形骸化してしまったり、一時的な盛り上がりで終わってしまったりするケースも少なくありません。5S活動を継続し、組織文化として定着させるためには、いくつかの重要なポイントがあります。荷主企業としても、物流パートナーの活動を支援し、共に成果を享受する視点が重要です。
「見える化」による進捗管理と成功体験の共有
5S活動の進捗状況や成果を、グラフや写真などを用いて職場内に掲示し、「見える化」します。目標達成や改善事例を荷主と物流パートナー間で共有することで、双方のモチベーションを高め、成功体験を積み重ねていくことが重要です。小さな成功でも良いので、積極的に評価し合い、活動への参加意欲を引き出しましょう。
定期的な5Sパトロールの実施と、建設的なフィードバック文化の醸成
荷主企業の担当者が定期的に委託先倉庫を訪問し、5S活動の状況を確認する(5Sパトロール)ことも有効です。単に問題点を指摘するだけでなく、良い点や努力している点を積極的に評価し、共に改善策を考えるなど、建設的なフィードバックを心がけます。パトロールの結果は記録し、継続的な改善に繋げます。
5S活動コンテストや改善事例発表会など、楽しみながら参加できる工夫
5S活動が義務感だけで行われると長続きしません。物流パートナー企業内で、部署対抗の5Sコンテストが開催されたり、優れた改善事例を発表する場が設けられたりする場合、荷主企業としてそれを奨励・支援することも、良好な関係構築と活動の活性化に繋がります。
小集団活動(QCサークルなど)との連携による、改善活動の日常化
物流パートナー企業内でQCサークルなどの小集団活動が行われている場合、そのテーマとして5S活動を取り上げてもらうよう働きかけることも一案です。現場の従業員が自ら問題を発見し、解決策を考え、実行するというプロセスを日常的に繰り返すことで、改善文化が組織に根付きます。
経営層による継続的な関心と、活動成果に対する正当な評価
荷主企業の経営層が、物流品質や物流パートナーとの連携における5S活動の重要性を理解し、継続的に関心を持つことが不可欠です。また、物流パートナーの5S活動の成果や努力を正当に評価し、それを契約更新の際の評価項目の一つとしたり、インセンティブを設けたりすることも、活動を定着させる上で有効な手段となり得ます(ただし、公平性と透明性が重要です)。
5S活動は、変化に強く持続可能な物流体制を築くための第一歩
本記事では、物流現場における5S活動の重要性、基本的な進め方、期待される効果、そして活動を成功させ定着させるための秘訣について解説してきました。
5Sを起点とした、継続的な改善文化の醸成が企業の成長を支える
5S活動は、単なる職場美化運動ではありません。それは、ムダを徹底的に排除し、業務効率を高め、安全性を確保し、従業員の意識を変革するための強力な経営ツールです。荷主企業が主体的に、あるいは物流パートナーと協調して5S活動を徹底することで、問題点が「見える化」され、関わる全ての人に改善意識が芽生えます。この「気づき」と「改善」の積み重ねこそが、変化の激しい時代を生き抜くための、強くしなやかな現場力、そして継続的な改善文化を育むのです。
今こそ、自社の物流現場のポテンシャルを最大限に引き出すために5S活動に取り組もう
物流DXや自動化といった新たな技術導入が加速する現代において、その効果を最大限に引き出すためにも、まずは足元である物流現場(自社および委託先)の5S活動を見直し、強固な土台を築くことが不可欠です。5S活動は、決して一朝一夕に成果が出るものではありませんが、地道に継続することで、必ずやコスト削減、品質向上、生産性向上、そして顧客満足度の向上といった形で、荷主企業の経営に大きなプラスの効果をもたらします。
この機会に、ぜひ自社の物流部門、そして重要なビジネスパートナーである物流企業の現場力を5S活動を通じて高め、サプライチェーン全体の競争力強化に繋げてみてはいかがでしょうか。
関連記事
お役立ち資料/ホワイトペーパー
記事検索
-
物流関連2法
-
特定荷主