スループットとは?概要や重要性、メリット、最大化するための具体的な方法や米国・日本の事例を解説
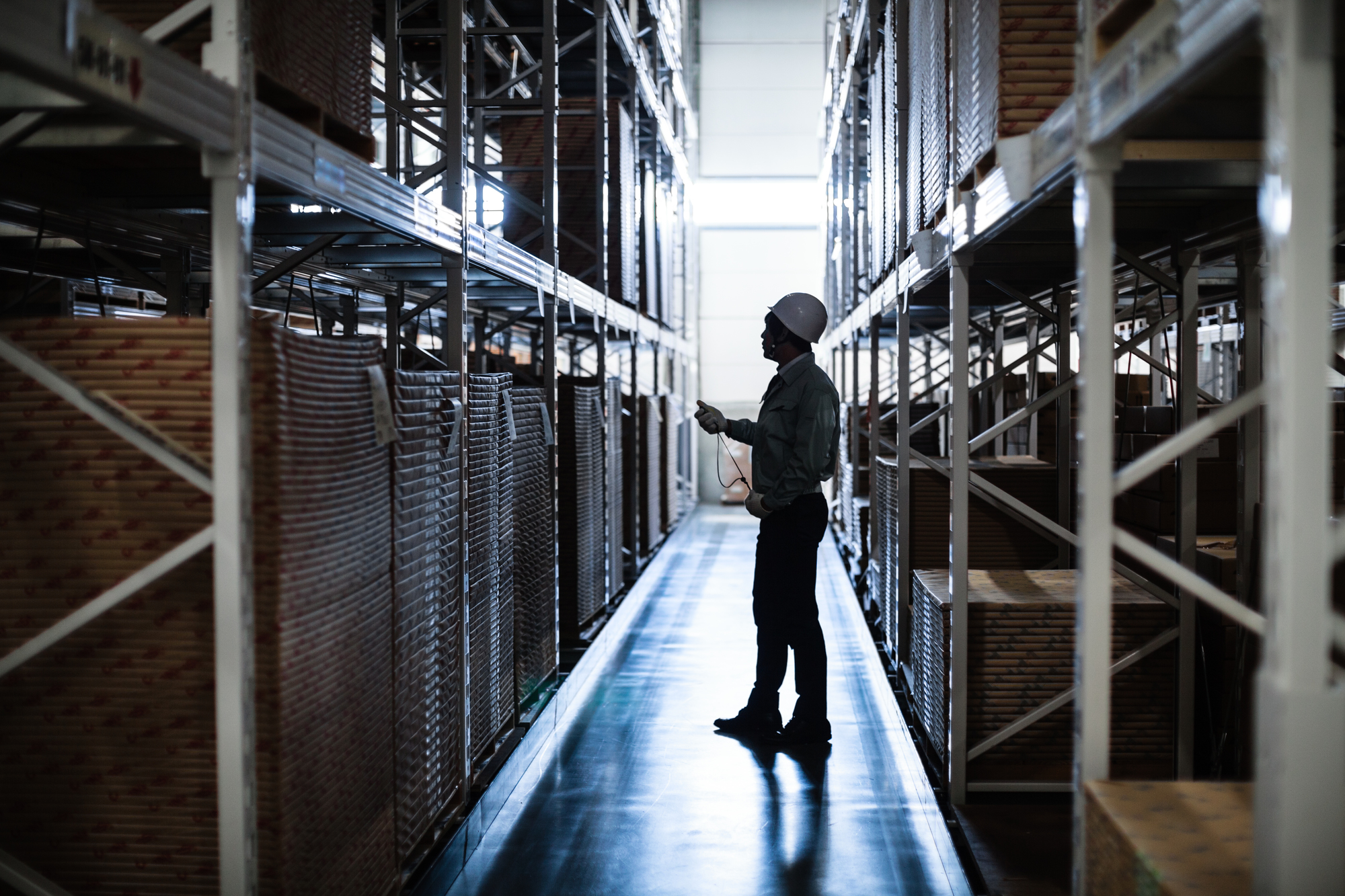
物流センターや工場の現場では、「どうすれば作業効率を上げられるか」「なぜ目標の処理量に達しないのか」という課題に日々直面しています。これらの課題を解決する上で重要になるのが「スループット」という考え方です。
本記事では、スループットの基本的な考え方から具体的な改善方法まで、実践的な内容を物流DXパートナーのHacobuがご紹介します。
目次
スループットとは
スループットとは、単位時間あたりの処理能力を表す指標です。例えば、以下のように現場で具体的な数値として把握できるものです。
- 物流センター:1時間あたりの出荷個数
- 製造ライン:1日あたりの生産台数
- 検品作業:1人あたりの1時間の検品処理数
スループットの重要性とメリット
スループットを適切に管理することは、物流・製造現場の運営において極めて重要な意味を持ちます。
納期遵守率の向上
現場の処理能力が明確になることで、お客様からの納期に関する問い合わせに対して、より正確な回答が可能になります。また、繁忙期や急な大量注文が入った際にも、必要な処理能力を事前に把握できるため、適切な対応が可能となります。
コスト削減
スループットを把握し改善することで、残業時間を大幅に削減できます。また、設備の稼働率を向上させることで、既存の設備でより多くの処理が可能になり、新規設備投資を抑制することができます。さらに、作業量と処理能力の関係が明確になることで、必要な人員配置を最適化でき、人件費の効率的な運用にもつながります。
品質向上
スループットを管理することで、作業のどの部分がボトルネックとなっているかが明確になり、そこに焦点を当てた改善活動が可能になります。また、標準的な作業時間が設定されることで、作業者が必要以上に急ぐことなく、適切なペースで作業を行えるようになり、作業ミスの低減にもつながります。
スループットの最大化とは
ザ・ゴールという本はサプライチェーンの教科書として非常に有名な本でしょう。そこではボトルネック行程を分析して、スループットを最大化することで工場が再生したことが書かれています。日本の工場では需要の変動に合わせながら、生産性を最大化を狙った生産計画というのは当たり前の考え方になっています。つまり、工場ではスループットの最大化ということを日々考えながら作業を実施されています。しかしながら物流の世界で、スループットの最大化という言葉を使う方々は少ないでしょう。入荷や出荷が大まかな時間単位になっており、作業計画を立てにくい環境にあるためではないかと考えています。
スループット最大化の具体的な方法
ボトルネックの特定
スループットの改善には、まず現場のボトルネックを正確に特定することから始める必要があります。物流センターでは、ピッキング作業での商品取り出し時間が大きなボトルネックとなることが多く見られます。特に、人気商品が奥に配置されていたり、重量物と軽量物が混在していたりする場合に顕著です。製造現場では、検品作業での書類確認や、荷役機器の待ち時間がボトルネックとなるケースが多く見られます。システム入力作業の遅延も、全体の作業効率を下げる要因となっています。
改善策の実施
これらのボトルネックに対しては、具体的な改善策を講じていく必要があります。まず、動線の最適化が重要です。出荷頻度の高い商品は出荷口近くに配置し、作業者の移動距離を最小限に抑えます。また、クロスドッキングエリアを設置することで、保管を必要としない商品の処理時間を大幅に短縮することができます。
作業の標準化も効果的な改善策です。ピッキングルートを固定することで、作業者が迷うことなく効率的に作業を進められるようになります。また、作業手順書を作成して教育を行うことで、作業者による処理速度のばらつきを抑えることができます。検品作業においては、チェックリストを活用することで、確認漏れを防ぎつつ、作業速度を向上させることができます。
設備やシステムの導入も、状況に応じて検討する価値があります。ハンディターミナルの活用により、データ入力作業を効率化できます。音声ピッキングシステムを導入すれば、作業者の両手が自由になり、作業効率が向上します。また、AGV(無人搬送車)の導入は、人手不足の解消と24時間稼働の実現に貢献します。
測定と改善のサイクル
スループットの最大化を継続的に行うためには、PDCAサイクルに基づいた測定と改善の取り組みが欠かせません。
現状把握
まず、現状把握の段階では、工程別の処理時間を詳細に測定します。この際、単に平均値を見るだけでなく、作業者別の生産性データや時間帯別の処理量の変動なども細かく分析します。これにより、改善すべきポイントがより明確になります。
目標設定
次に、目標設定の段階では、現場の実態に即した達成可能な目標を設定することが重要です。現場の作業者のモチベーションを考慮し、段階的な改善計画を立案します。例えば、最初の3ヶ月で5%の改善、半年で10%の改善といった具合に、実現可能な目標を段階的に設定していきます。
改善活動
改善活動の実施では、現場作業者を積極的に巻き込むことが重要です。現場で実際に作業を行っている人々の意見やアイデアを取り入れることで、より実効性の高い改善が可能になります。また、大きな改革を一度に行うのではなく、小さな改善を積み重ねていくアプローチが効果的です。定期的な進捗確認と見直しを行いながら、必要に応じて改善策を修正していくことで、持続的な改善が実現できます。
米国スーパーマーケットの例
米国大手スーパーマーケットの倉庫では、スループットの最大化のため、ボトルネックがどこにあるのかを常にモニターするインダストリアルエンジニアリングチームという部隊を持っています。大学などで専門の教育を受け、理系頭脳を持ち物流を数学でとらえるメンバーです。彼らは各工程の生産性を計測し、ボトルネック行程の生産性をあげるために、新しいプロセスへの変更やマテハン機器の調整・導入を行っています。それらの作業の中で重要視しているのが、荷物の入荷時間と出荷時間です。店舗出荷時間から逆算して、どのようなものが何時に入ってきて、その後どのような作業を加えて出荷してくかについて綿密な計画が立てられ実行されています。これらはWMSでコントロールされ、また人事システムと連携して、適切な人材のアサインメントがなされています。こうして倉庫のスループットの最大化を日々追求しています。これは彼らが購買力を使って、欲しいものを欲しい時間に正確に届けさせることから始まっています。場合によってはメーカーに生産計画の変更まで要求し、効率的な運用を実現しているのが実態です。
日本企業での適用
日本の流通倉庫で効率的なマネジメントを実現するためには、さらに高度なマネジメントが必要になるものと考えています。なぜなら日本で市場で上記企業ほどの購買力をもつプレーヤーは存在せず、メーカーの生産計画を変えられる力を持つ場合は少ないためです。結果として、日本では、流通倉庫の納品希望時間に対して、メーカー側の納品可能時間が確認し、流通倉庫側で作業時間の再設計が必要になります。
この作業は一見大変なように見えますが、基本納品パターンは週次で決まっていることが多いため、大きな季節動向の変化の際に1度行えば良い作業であり、それによりスループットが最大化できるので価値が大きな作業です。Hacobuの顧客では、これらにより入荷作業の効率が30%向上したという企業も出てきています。
今、庫内作業の自動化を検討している企業も多いでしょう。機械は予定通りに計画された動きをするため、庫内作業の自動化の効果を最大化していくためには、その接点となる入荷と出荷の時間の厳格なマネジメントが今まで以上に重要になっていくでしょう。
すべては「見える化」から
すべての出発点は入荷時間、出荷時間の見える化です。改善点を見つけるという観点でデータを見れば、トラックの荷待ち時間の問題だけではなく、入出荷量のブレによる手待ちの発生など見えてくるはずです。問題点が見えれば、改善は日本企業の得意とするところではないでしょうか。これも物流DXと捉え、是非ともチャレンジしてみてはいかがでしょうか。
関連記事
お役立ち資料/ホワイトペーパー
記事検索
-
物流関連2法
-
特定荷主