荷役とは?概要や物流現場での課題、最適化方法をわかりやすく解説
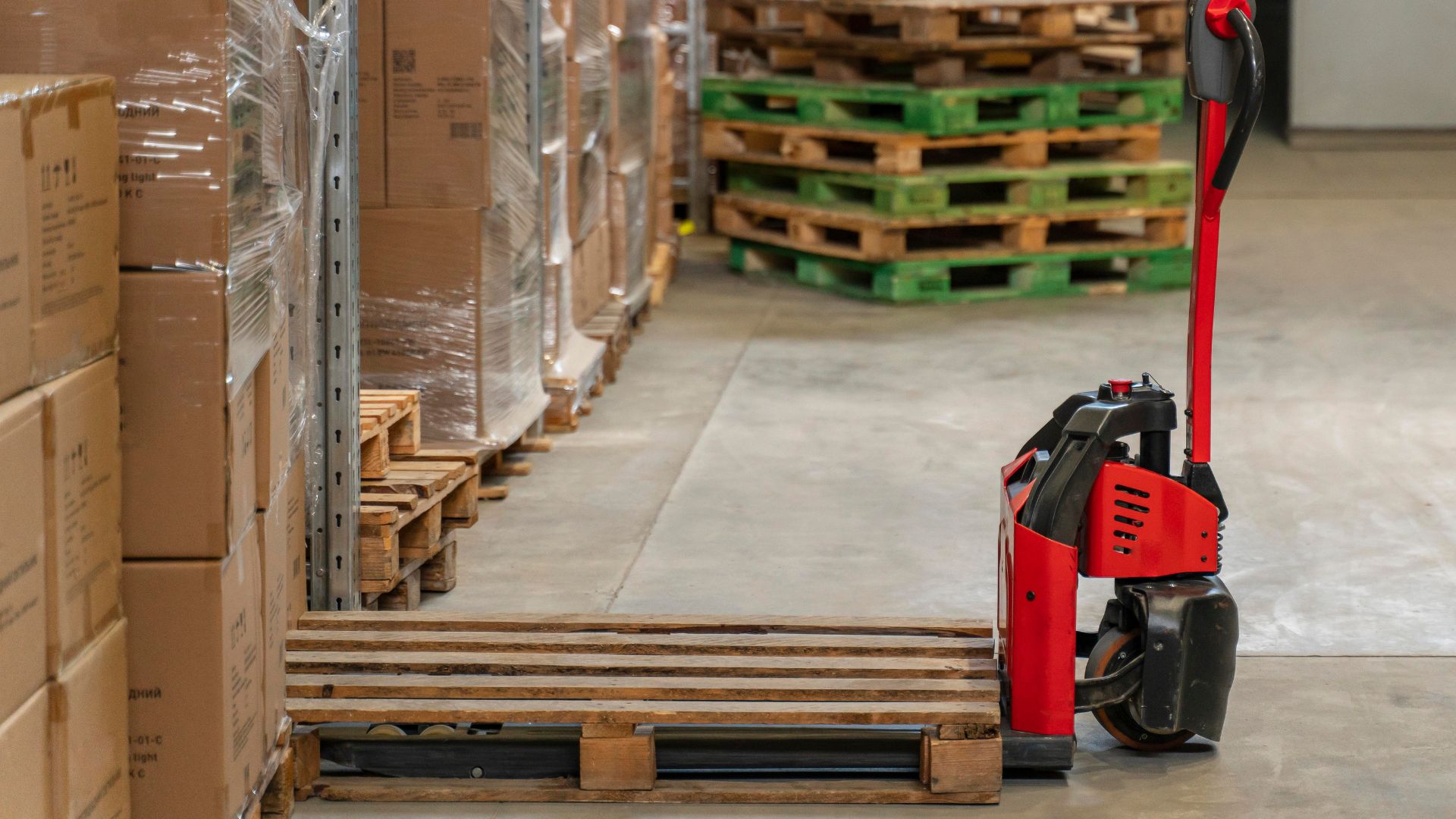
荷役は物流プロセスにおいて不可欠な作業であり、商品の効率的な取り扱いや移動を支えています。本記事では荷役の基礎や役割、種類、使用される機器、課題、現状、時間短縮のメリット・方法について、物流DXパートナーのHacobuが解説します。
なお、荷役時間の把握や短縮には、MOVO Berth(ムーボ・バース)のようなトラック予約受付システムが有効です。
MOVO Berthの資料は以下からダウンロードいただけます。
目次
荷役とは
まずは荷役の基礎について解説します。
荷役の概要
荷役(にやく・にえき)とは、物流の過程で荷物を積み降ろし、仕分けをし、適切な場所へ移動させる一連の作業を指します。物流センターや倉庫での荷物の入出荷を大きく分けると、以下のような流れになります。
入庫
- トラックなどからの荷降ろし
- 仕分けと運搬
- 保管場所への格納
出庫
- 出荷指示にもとづくピッキング
- 仕分けと荷揃え
- トラックへの積み込み(荷積み)
このように保管と輸送をつなぐ作業が荷役であり、物流において欠かせない中核的な役割を担っています。
荷役の役割
物流拠点では毎日、大量の荷物が入出荷されます。仕入れ先別に入ってきた荷物を、今度は配送先別に組み替えて出荷する「変換作業」を行うことが荷役の大きな役割です。
「にやく」と「にえき」の違い
読み方としては「にやく」「にえき」の2種類がありますが、指し示す作業内容に違いはありません。
荷役の特徴
輸送手段ごとに、荷役の特徴を解説します。
内陸荷役
内陸荷役は、主にトラック輸送における荷物の積み降ろし作業を指します。工場や物流センター、倉庫などでフォークリフトを用いて荷役を行う場面が代表例です。
港湾荷役
船舶輸送ではコンテナが標準化されており、港湾ではガントリークレーンを使って船舶への積み降ろしを行います。その後、ドレージ輸送によってコンテナを倉庫やターミナルへ移動させます。
空港荷役
空港荷役は、航空機への積み降ろしや仕分け作業です。航空便は「軽量・高価値」の貨物が多く、スピードと正確性が求められます。またフライトスケジュールに合わせた緊急対応や、トラブル時の素早い対応も重要です。
以降では、内陸荷役を中心に解説します。
荷役の種類
荷役はさらに細かく分類できます。
積み降ろし
トラックなどの貨物輸送機器への積み込みと、目的地での荷降ろしを指します。
大型貨物・重量物の取り扱い
高い技術や経験が必要で、商品の損傷防止やバランスの確保が重要です。
積載形態による時間の違い
パレットに載っていればフォークリフトですぐに積み降ろしができますが、バラ積みだと人力で一つずつ積み降ろしする必要があり、作業時間が大幅に増えます。
仕分け・積付け・荷揃え
入庫時
保管場所別に仕分けを行いながら、パレットやカゴ車に積み付けします。その際、重い荷物を下に配置したり、荷崩れ防止のために固定したりといった工夫が必要です。
出庫時
配送先のトラック別に荷物を揃え、輸送に適した積付けを行います。
運搬
荷捌き場と保管場所の間で荷物を移動させる作業です。フォークリフトやカゴ車、コンベヤを使うことで大量の荷物を効率的に動かします。運搬では、商品の破損や紛失を防ぐ取り扱い方法や動線確保が重要となります。
格納・ピッキング
格納
運搬した荷物を、あらかじめ定めた保管場所に収めることです。
ピッキング
出荷指示を受けた荷物を、正しい種類・数だけ保管場所から取り出して集める作業です。
いずれも、保管場所の確認、商品の正しさや数量の確認が基本手順となります。
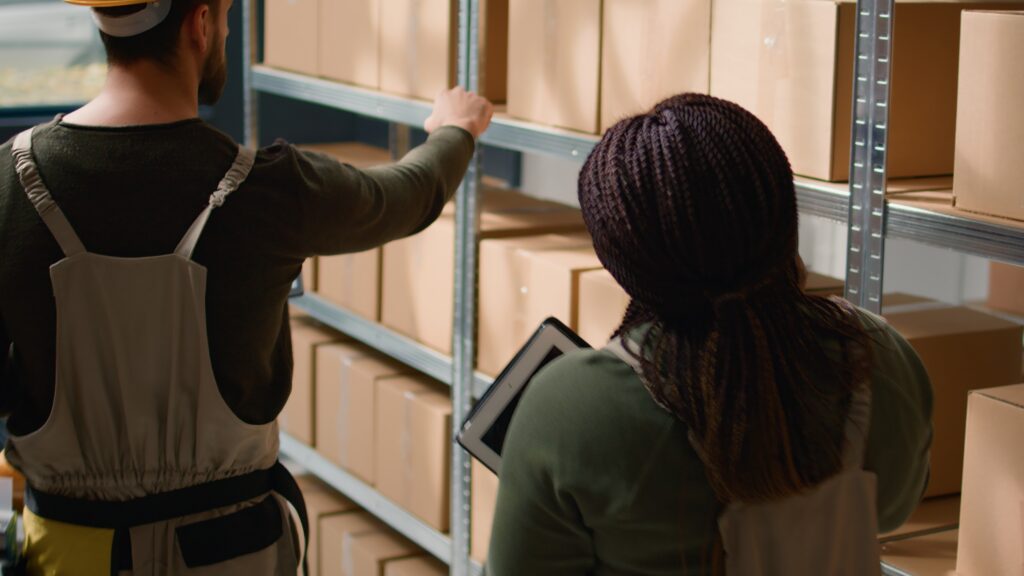
荷役に使用される機器
効率化はもちろん、労働負担の軽減や安全対策の観点からも、荷役には機器やツールの適切な活用が欠かせません。
フォークリフト
倉庫作業の中心的存在で、重い荷物の積み込みや運搬に不可欠です。作業員の労働負担を大幅に軽減し、効率的なオペレーションを実現します。
クレーン(天井クレーン)
大型貨物を取り扱う際に活躍する機械です。天井クレーンは倉庫の天井に設置され、高所から荷物を移動させるため、限られたスペースでも効率的に荷役を行えます。
コンベヤ
自動搬送装置として、倉庫や製造ラインでの荷役の迅速化と省力化に貢献します。荷物を連続的に移動できるため、人手による運搬回数が大幅に減少します。
パレット・ラック
商品の整理整頓と効率的な保管を支える基本ツールです。パレットを用いて荷物をまとめ、ラックに収納することで倉庫内の空間を有効に活用し、作業効率を上げることができます。
ロボット・自動化設備
自動搬送ロボット(AGVなど)は、 倉庫内の運搬を自動化し、人手不足解消に寄与します。ピッキングロボットは、バーコードやAI技術を活用し、高精度なピッキングを実現します。
詳細は以下の記事もご覧ください。
マテハンとは?導入のメリットやデメリット、導入時の注意点、業務別の主なマテハン機器を解説
マテハンと…
2024.09.26
これらの導入により、作業スピードと正確性が格段に向上します。
人手による荷役への制限と労働災害、安全対策
重量物など、身体負荷の大きい荷役作業には法的な制限があります。
重量物の制限
厚生労働省が示す「職場における腰痛予防対策指針(1994年)」では、人力のみで扱う荷物の重量は、男性は体重の40%まで、女性はその男性の取り扱う重量の60%程度とされています。作業前にリスクを評価し、重量の明示や持ちやすい形状への工夫、2人作業の導入などを行う「リスクアセスメント」の取り組みも強く求められています。
リスクアセスメントの活用
リスクアセスメントとは、潜在的なリスクを体系的に洗い出し、発生確率や影響度を評価したうえで、適切な対策を優先順位に沿って実施するプロセスです。 結果は災害防止マニュアルや安全対策に反映され、定期的な見直しで常に最新の対策を維持することが大切です。
労働災害の防止と安全対策
安全対策としては、適切な安全装備の着用や作業手順の遵守、定期的な安全講習の実施などが挙げられます。作業員は、安全ヘルメット、保護手袋、安全靴などの個人防護具を着用し、作業中の事故を未然に防ぐことが求められます。また、機械や設備の操作には十分な訓練を受け、正しい手順を守ることが重要です。さらに、作業現場の整理整頓や危険箇所の明示など、作業環境そのものの安全性を高める取り組みも必要です。
ドライバーの労働災害発生は荷役時が7割
ドライバーの労働災害は、交通事故よりも荷役作業時のほうが多く、約7割を占めるとされています。年間1万件近くあるとの推計もあり、厚生労働省は2023年に「荷役作業安全ガイドライン」を改訂し、ドライバー・荷主・配送先・元請け事業者が連携して荷役時の労働災害を防ぐ必要性を再度明確にしました。
新ガイドラインでは、ドライバーに依頼する荷役作業は事前通知が必須となり、通知されていない作業をドライバーに行わせてはならないことが明記されています。また、荷主には荷役5大災害の防止策を徹底する責務が課せられています。
荷役5大災害
- 墜落・転落
- 荷崩れ
- フォークリフト使用時
- 無人暴走
- 後退時
参考:陸上貨物運送事業における 労働災害発生状況と本年度の補助事業
物流現場の荷役における課題
荷役には、さまざまな課題があります。
人手不足
日本倉庫協会が2024年に行った調査によると、今後5年以内に倉庫現場の人員不足率は15.9%に達すると予測されており、荷役作業員の確保が大きな課題となっています。
トラックの集中
一定の時間帯に物流拠点のキャパシティを超える台数のトラックが集中すると、場内の混雑や事故リスクが高まるうえ、作業者の心理的負担にもつながります。
荷待ちの発生
繁忙期や入出庫のピーク時には、荷役が滞ってトラックの長時間待機(荷待ち)が発生しがちです。ドライバーの拘束時間が延び、運行スケジュールにも影響を及ぼします。
拠点内の情報連携
事務所・待機場所・荷捌き場などが物理的に離れていると、互いの状況を把握しづらくなり、ドライバーへの誘導ミスや無駄な移動が発生します。結果として荷待ちや作業遅延につながるケースも多いです。
非計画な作業手順
トラックが到着してから保管場所を探す、届いた荷物を仮置きして後で仕分けるなど、場当たり的な手順は作業時間を大幅に増やします。
仕分け・積付け・荷揃えの属人化
仕分け・積付け・荷揃えは、トラックの発着状況に左右されるため、臨機応変な対応が必要です。しかし、これらの作業が人の経験や勘に依存していると、業務が属人化して遅延やミスが発生しやすくなります。
法対応
流通業務総合効率化法の改正により、すべての荷主・倉庫業者には荷役時間の短縮の努力義務が課せられました。さらに、一定の基準を超える特定事業者(特定荷主・特定倉庫業者)には、荷役時間の短縮などについて中長期計画の作成と定期報告が義務化されました。
荷役時間の現状
国土交通省が発表した2024年度の調査結果によると、荷役時間は、1回の運送当たり平均1時間34分でした。前回の2020年度調査では、1時間29分だったことから、ここ数年で荷役時間は統計上では短縮できていないことになります。
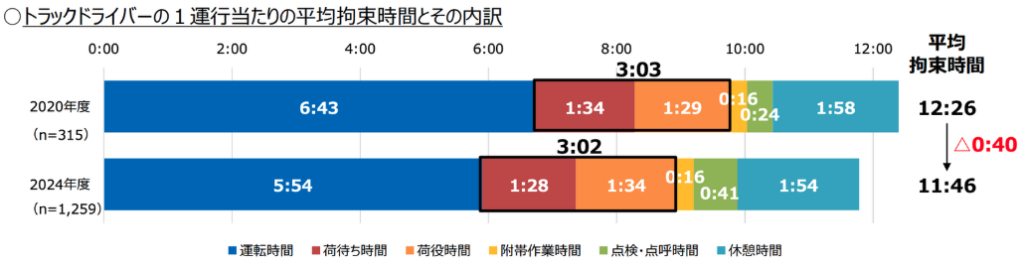
引用:第17回トラック輸送における取引環境・労働時間改善中央協議会
一方で、人手不足は深刻化しており、今後さらに荷役が滞るリスクが高まる可能性があります。荷主や倉庫業者は、本格的に荷役時間短縮に取り組む必要があるといえます。
荷役の非効率がもたらす経営リスク
社名公表のリスク
物流効率化法の改正により、荷主には荷役時間の短縮が努力義務として課されています。
努力義務には行政処分や罰則はありませんが、努力を怠った場合は勧告や社名公表などがなされたり、第三者からの損害賠償請求で不利な立場に置かれる恐れがあります。
社名公表や損害賠償請求がなされると悪い形で社名が世に広まり、信用低下、そして事実上の不利益につながるリスクがあります。
義務規定になる可能性を見据える
男女雇用機会均等法において、当初は努力義務だった規定が後に義務規定に変わった例があります。今後も荷役の効率化が進まない場合、荷役の効率化が義務規定となるかもしれません。
義務規定になる可能性を見据え、荷役の効率化を推進することが将来のリスクを回避することに繋がります。
特定荷主に迫る物流の「2026年問題」と、2025年にすべきこととは?法対応を物流改善の好機に
物流の「2026…
2025.03.07
荷役時間を短縮するメリット
荷役時間の短縮は、物流拠点側に多くのメリットがあります。
倉庫・ヤードの回転率向上
荷役時間が短縮されると、トラックの滞留時間が減り、倉庫やヤードのスペースを有効活用できます。限られたスペースの中でより多くの荷物を処理できるため、倉庫の稼働率が向上します。また、車両の荷待ち時間が減ることで、場内の混雑が解消され、フォークリフトや作業員の動線もスムーズになります。これにより、作業ミスや事故のリスクも低減し、効率的な物流オペレーションを実現できます。
作業員の労働生産性向上と人件費削減
荷役がスムーズに進むと、作業員のアイドルタイムが減少し、無駄なく業務を進められます。作業の流れが効率化されることで、少ない人員でも対応が可能になり、労働コストを削減できます。また、残業時間が減ることで作業員の負担も軽減され、労働環境の改善にもつながります。業務が標準化され、短時間で作業を終えられる仕組みを作ることで、全体的な生産性向上を図ることができます。
荷待ちの解消と協力会社との関係強化
スムーズな荷役を実現することで、運送会社やドライバーからの「待たされる現場」という評価を避け、必要な輸送力を安定的に確保しやすくなります。
リードタイム短縮による取引先満足度向上
荷役作業が迅速に進むことで、出荷スピードが向上し、納期の安定や短縮が図れ、取引先の満足度が向上します。
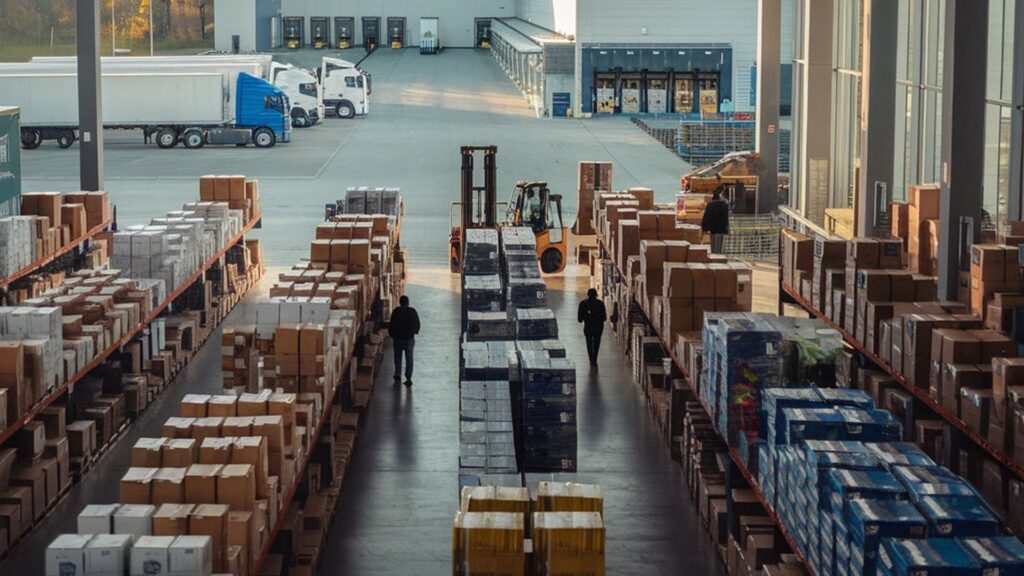
荷役時間を短縮する方法
荷役時間を短縮するためには、現場の作業効率を高める取り組みが必要です。本章では、具体的な改善策を解説します。
倉庫レイアウトと作業動線の最適化
倉庫内のレイアウトを見直し、作業員やフォークリフトの無駄な移動を削減することで、荷役作業のスピードを向上させることができます。たとえば、頻繁に出荷する商品を出荷エリアの近くに配置すれば、作業員が商品を取りに行く時間が短縮され、効率的にピッキングや積み込みが行えます。また、フォークリフトと作業員の動線を整理し、走行ルートを明確にすることで、渋滞や衝突のリスクを減らし、安全かつスムーズに荷物を運搬できます。定期的に作業動線を分析し、最適なレイアウトを維持することが、荷役時間の短縮につながります。
自動化・機械化の導入
フォークリフトの自動運転化、AGV(無人搬送車)やコンベアの導入など、機械化・自動化を進めることで、作業スピードを向上させることができます。特に、パレット積み降ろしの自動化や、バーコード・RFIDを活用した入出庫管理を導入することで、作業時間の短縮だけでなく、ミスの削減にもつながります。初期投資は必要ですが、長期的に見ると人手不足の解消やコスト削減に貢献します。
作業ルールの統一と教育の強化
作業ルールが統一されていないと、作業員ごとに手順が異なり、作業のばらつきが生じます。その結果、効率が悪くなり、時間のロスが発生します。この問題を解決するために、標準的な作業ルールを定め、全員が同じ手順で作業できるように教育を行うことが重要です。特に、新人教育の際には、マニュアルや研修を充実させることで、早期にスキルを習得できるようにします。これにより、作業の質を一定に保ち、スムーズな荷役を実現できます。
トラック予約受付システムの活用
トラックの到着時間が集中すると、荷役作業が滞り、荷待ち時間が長くなってしまいます。これを防ぐために、MOVO Berth(ムーボ・バース)のようなトラック予約受付システムを導入し、事前に荷役のスケジュールを管理することが効果的です。システムを活用することで、トラックの到着時間を分散させ、荷役作業をスムーズに進めることができます。また、ドライバーにとっても荷待ち時間の削減につながり、労働環境の改善にも寄与します。
有責待機とは?バースの予約運用で本質的な荷待ち時間削減に取り組もう
目次1 有責待機&…
2024.05.15
トラック予約受付システムの活用で荷役時間を短縮できる理由
作業計画性の向上
トラック予約受付システムでは、運送会社やドライバーが事前に荷役の予約を入力できるため、物流拠点側の管理画面にはトラックの入場予定(荷役予定)が、以下のように一覧で表示されます。これにより、トラックの到着時刻に合わせてあらかじめ荷物を荷揃えしておくことができ、実際にトラックが到着してからピッキングしに行く手間が大幅に削減されます。
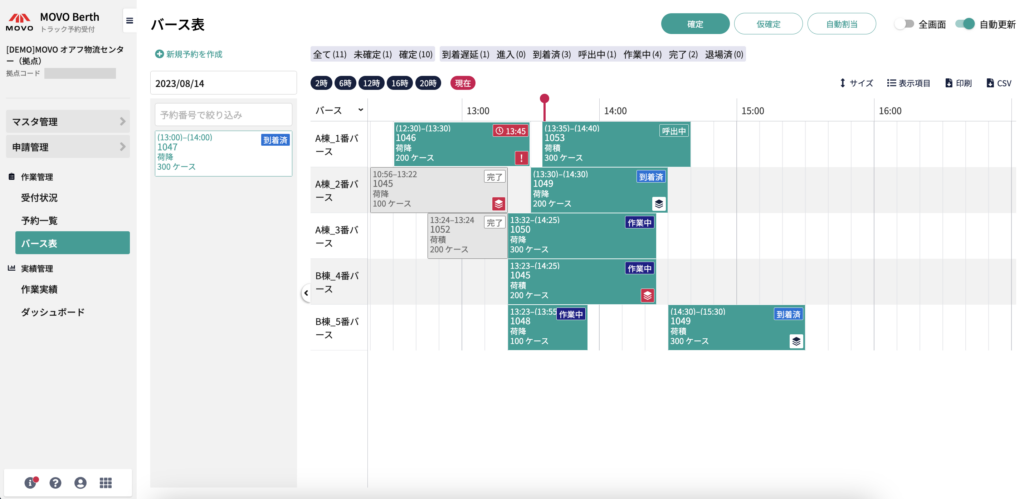
拠点内コミュニケーションの効率化
事務所と荷捌き場が物理的に離れていても、同じ管理画面を共有することで、事務所にいながら作業の進捗状況をリアルタイムで把握できます。ドライバーが到着した際には、事務所からでも適切な指示を出せるため、無駄な往復が減ります。
さらに、システムからドライバーの携帯電話へバース誘導の指示を直接送ることもできるため、待機場所まで呼び出しに行く必要がなくなり、時間のロスを最小限に抑えられます。
データ分析と課題の特定
以下のように直感的なダッシュボードを備えたシステムであれば、荷役時間が長くなっている作業を可視化できます。その結果、該当する荷物や荷姿をさらに深掘りし、長期化の原因を特定することが可能です。原因が明らかになれば、最適な改善策を検討し、荷役時間のさらなる短縮につなげることができます。
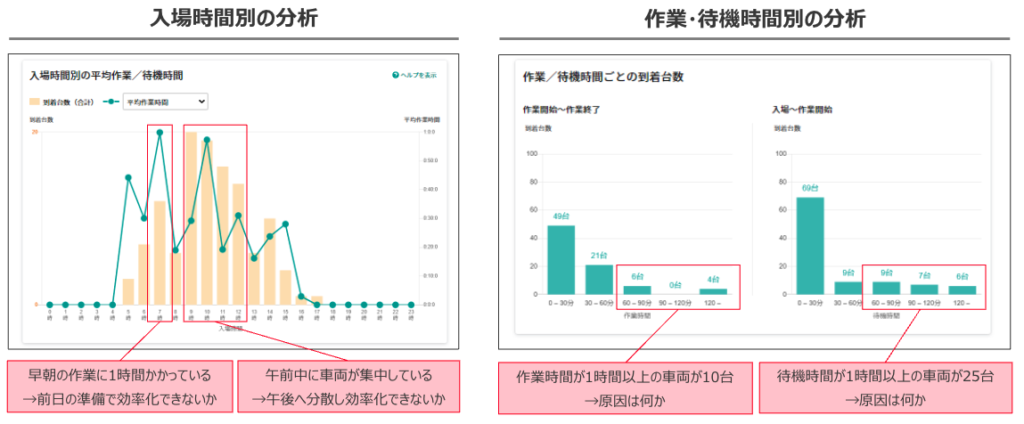
荷役時間の短縮ならMOVO Berth
トラック予約受付システムを活用して荷役時間を短縮するなら、MOVO Berth(ムーボ・バース)の導入がおすすめです。MOVO Berthは豊富な機能や手厚い導入支援が評価され、5年連続シェアNo.1*のトラック予約受付システムです。
MOVO Berthを活用した荷役時間短縮の事例:株式会社LIXIL物流
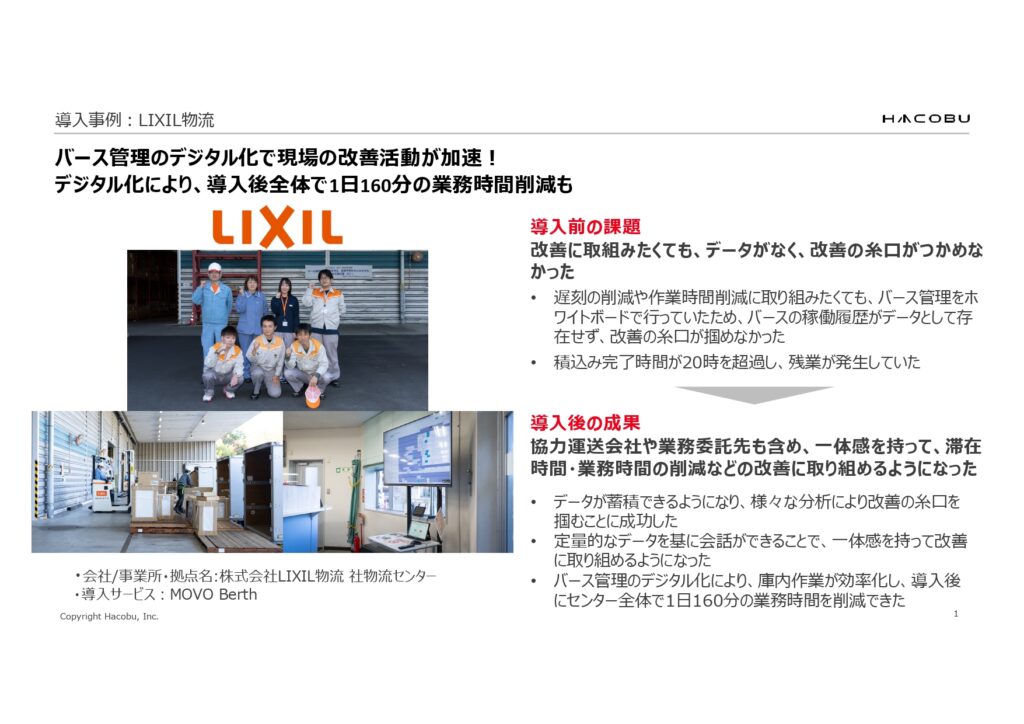
株式会社LIXIL物流は、MOVO Berth導入以前は、トラックがいつ入場するかわからないため、その把握に非効率な電話のやり取りが発生していました。しかし、MOVO Berthの導入によって入場予定が把握できるようになり、庫内作業が効率化され、1日160分の業務時間を削減できました。また、バース表を見ながら接車バースの入れ替えなども実施でき、バースの有効活用も可能になりました。
詳細は以下の記事をご覧ください。
バース管理のデジタル化で現場の改善活動が加速!デジタル化により導入後全体で1日160分の業務時間削減も
MOVO Berthの資料は以下からダウンロードいただけます。
※出典 デロイト トーマツ ミック経済研究所『スマートロジスティクス・ソリューション市場の実態と展望【2024年度版】』https://mic-r.co.jp/mr/02960/ バース管理システム市場の売上高および拠点数におけるシェア
関連記事
お役立ち資料/ホワイトペーパー
記事検索
-
物流関連2法
-
特定荷主