製造業DXとは?重要性やメリット、課題、進め方、工程別の推進ポイント、事例を解説
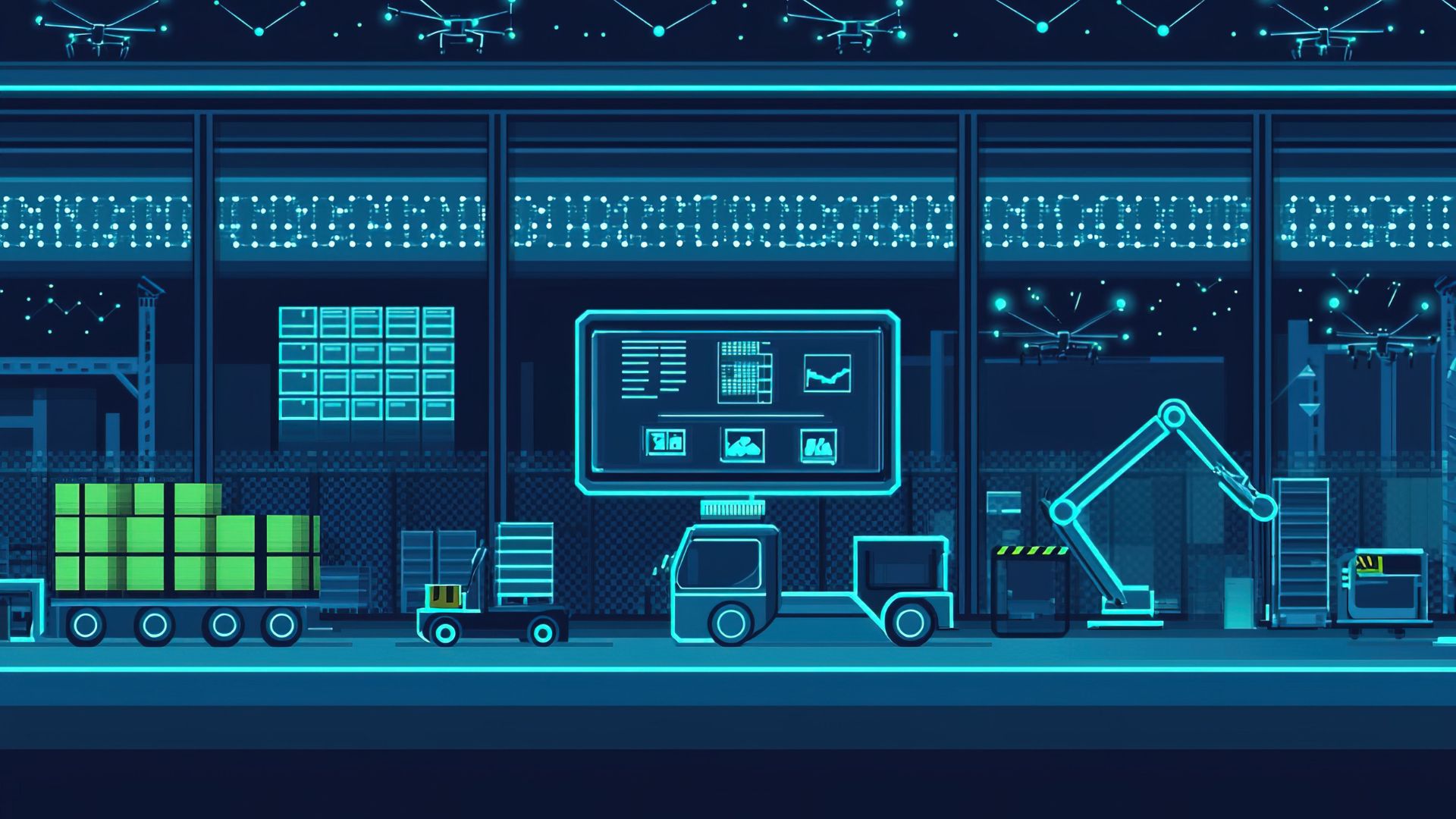
近年、製造業において「DX(デジタルトランスフォーメーション)」が注目を集めています。人手不足や生産性向上の課題を抱える製造業にとって、DXは避けては通れない重要なテーマとなっています。本記事では、製造業DXの基本的な概念から、その重要性、期待されるメリット、さらには具体的な導入事例まで、製造業のDX推進に関する情報について、物流DXパートナーのHacobuが解説します。
なお、Hacobuでは物流DXの戦略、導入、実行まで一気通貫で支援する物流DXコンサルティング Hacobu Strategy を提供しています。物流業務の改善にお悩みがありましたら、以下をクリックしてご覧ください。
目次
製造業DXとは
製造業DXとは、従来の製造プロセスやビジネスモデルをデジタル技術によって根本的に変革することを指します。製造現場でのデータ収集・分析による予知保全、デジタルツインによる製品開発の効率化、サプライチェーン全体の可視化と最適化など、様々な取り組みが含まれます。これにより、生産性の向上だけでなく、新たな付加価値の創出や顧客満足度の向上も実現できます。
製造業DXが必要とされる背景
製造業においてDXが求められる背景には、以下のような要因があります。
グローバル競争の激化
世界規模での競争が激化する中、製造業各社は生産性向上とコスト削減の両立を迫られています。新興国企業の台頭により価格競争が激化する一方で、製品の高付加価値化も求められており、デジタル技術の活用なしには競争力の維持が困難になっています。
消費者ニーズの多様化と変化の加速
消費者の嗜好や要求は急速に多様化・個別化しており、これに対応するための柔軟な生産体制の構築が必要です。また、製品のライフサイクルも短縮化しており、市場投入までのリードタイムの短縮や、迅速な製品改良が求められています。デジタル技術を活用することで、このような変化への対応力を高めることができます。
サステナビリティへの要求
環境負荷の低減や持続可能な生産活動への社会的要請が高まっています。製造業DXは、エネルギー使用の最適化、廃棄物の削減、資源の効率的利用などを実現し、環境負荷を低減させることができます。また、製造プロセスの透明性を高めることで、環境への配慮や社会的責任を示すことも可能になります。
製造業のDX推進状況
IPA(独立行政法人情報処理推進機構)の「DX動向2024」によると、企業全体として、DXの取り組みは年々増加傾向にあります。DXに取り組んでいる企業(全社戦略に基づき取り組んでいる、一部の部門で取り組んでいる、部署ごとに個別で取り組んでいるの合計)の割合は、2021年度の55.8%から73.7%に増加し、企業へのDX浸透が着実に進んでいることがわかります。
また、業種別に見ると、「製造業等」でDXに取り組んでいる企業の割合は77.0%と高い傾向にあります。ただし、DXの取り組み内容はデジタイゼーション、デジタライゼーションの段階が多く、デジタルトランスフォーメーション段階での取り組みは成果が出ていない部分もある状況です。
製造業DXを推進するメリット
以下では、製造業DXを推進する主なメリットを3つご紹介します。
データドリブンな意思決定
製造業DXを推進することで、生産現場から得られる膨大なデータを活用した意思決定が可能になります。センサーやIoTデバイスから収集されるリアルタイムデータを分析することで、生産計画の最適化や品質管理の精度向上、設備の予知保全など、より正確で効率的な判断を行うことができます。これにより、従来の経験や勘に頼る経営から、客観的なデータを活用した意思決定へと移行できます。
新たなビジネスモデルの創出
デジタル技術の活用により、従来の製品販売中心のビジネスモデルから、製品とサービスを組み合わせた新たな価値提供が可能になります。例えば、製品の稼働状況をモニタリングしてメンテナンスサービスを提供するサブスクリプションモデルや、製品から得られるデータを活用した顧客向けコンサルティングサービスなど、収益源の多様化を図ることができます。
サプライチェーンの最適化
サプライチェーン全体のデジタル化により、部材の調達から製造、物流、販売までの一連のプロセスを可視化し、効率的に管理することが可能になります。在庫の適正化や配送ルートの最適化、需要予測の精度向上などにより、コスト削減とリードタイムの短縮を実現できます。また、不測の事態が発生した際の代替調達先の確保など、サプライチェーンの強靭化にも貢献します。
製造業DXを推進するうえでの3つの課題
一方で、製造業DXの推進には課題も残ります。
デジタル人材の不足
多くの製造業企業において、DX推進に必要なデジタルスキルを持つ人材が不足しています。データサイエンティストやITエンジニアといった専門人材の確保が困難であるだけでなく、現場の従業員のデジタルリテラシー向上も課題となっています。外部からの人材採用や社内教育の強化、デジタル人材の育成プログラムの整備などが求められています。
レガシーシステムの存在とデータの分断
多くの製造業企業では、長年使用してきた古いシステムが存在し、新しいデジタル技術との統合が困難な状況にあります。また、部門ごとに異なるシステムを導入してきた結果、データが分断され、全社的な活用が難しくなっています。こういった課題を解決するためには、システムの刷新やデータ統合基盤の整備が必要ですが、多大な投資とリソースが必要となります。
組織文化と経営層の理解不足
DXの推進には、従来の業務プロセスや組織文化の変革が求められますが、変化への抵抗が課題となることも少なくありません。特に、経営層のデジタル技術に対する理解不足や、投資対効果の不透明さから、DX推進への積極的な投資判断が遅れるケースも少なくありません。DXを成功させるには、経営層のリーダーシップと組織全体の意識変革が欠かせません。
製造業DXの進め方
製造業DXを進めるには、まず全体のプロセスを見渡したうえで以下のようなステップで進めていきます。
1. 現状分析と目標設定
製造業DXを成功させるためには、まず自社の現状を正確に把握することから始める必要があります。現在の業務プロセス、システム構成、データの流れ、人材のスキルレベルなどを詳細に分析します。その上で、経営課題や市場環境を踏まえた明確な目標を設定します。この際、短期的な効率化だけでなく、中長期的な競争力強化や新規事業創出なども視野に入れた目標設定が重要です。定量的なKPIを設定することで、進捗管理や成果測定も容易になります。
2. 推進体制の構築と計画策定
DXを確実に推進するには、社内横断的な体制の構築が不可欠です。経営層直轄のDX推進部門を設置し、各事業部門との連携を図りながら、全社的な取り組みとして展開することが望ましいです。また、外部のコンサルタントやITベンダーとの協力体制も検討します。推進計画では、優先順位を付けたロードマップを作成し、段階的な実施により、早期に成果を出せる領域から着手することで、組織全体のモチベーション向上につなげます。
3. デジタル技術の導入と業務変革
計画に基づき、具体的なデジタル技術の導入と業務プロセスの変革を進めます。IoTセンサーやAI、クラウドシステムなど、目的に適した技術を選定し、段階的に導入を進めます。この際、単なる技術導入ではなく、業務プロセスの見直しや働き方改革も含めた包括的な取り組みが求められます。また、従業員への教育・研修を並行して実施し、新しい技術や業務プロセスへの適応を支援します。
4. 成果の評価と改善
導入したデジタル技術や新しい業務プロセスの効果を定期的に評価します。設定したKPIの達成状況を確認し、期待した成果が得られない場合は、その原因を分析して必要な改善を行います。また、従業員からのフィードバックも積極的に収集し、使い勝手や業務効率の観点から改善点を洗い出しましょう。評価結果を次のアクションにつなげるPDCAサイクルを確立することで、継続的な改善と発展を実現します。
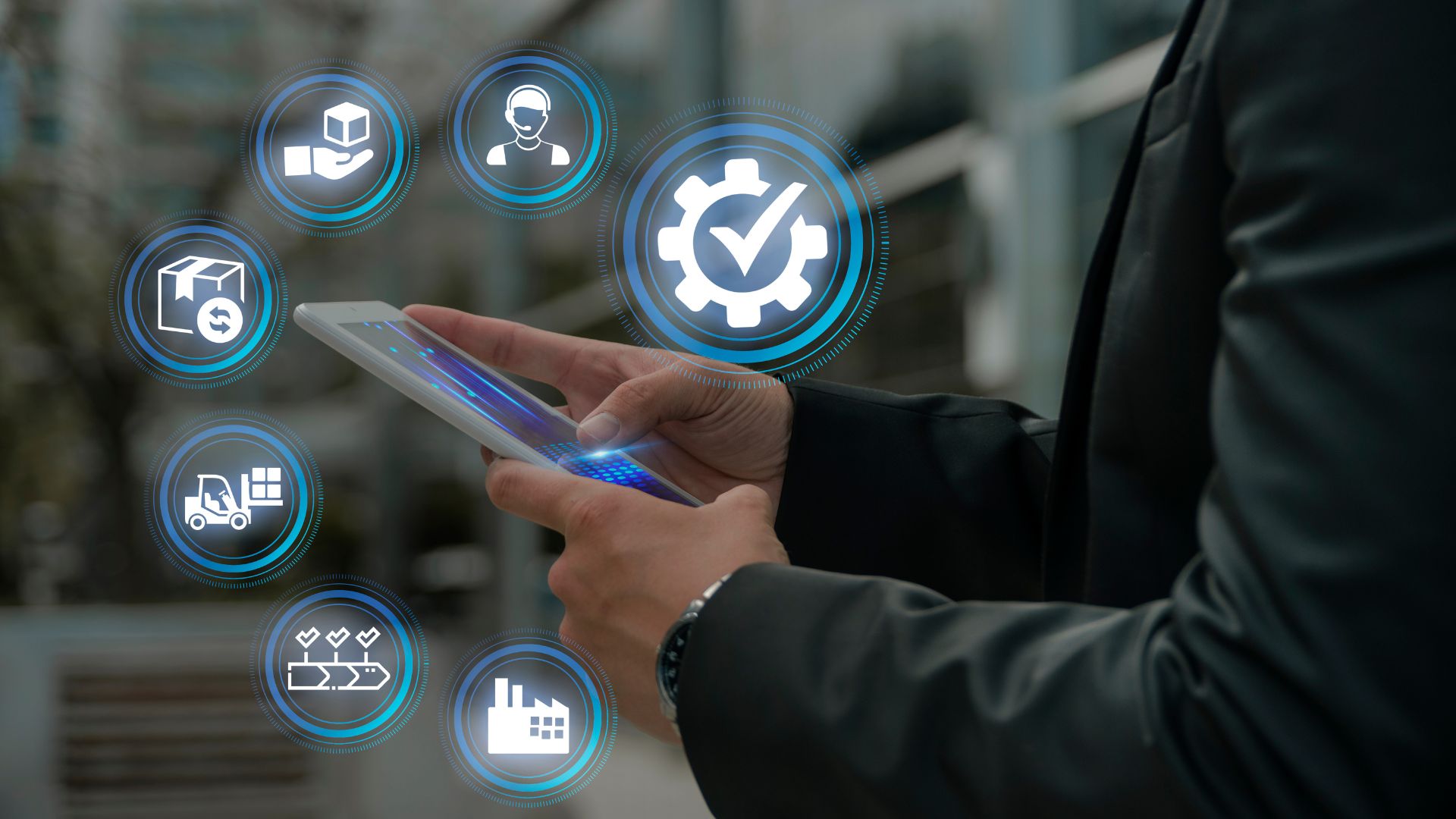
【工程別】製造業DXを進めるポイント
製造業DXを進めるステップは先ほどご紹介しましたが、ここからは製造業の各工程において製造業DXを検討すべきポイントを解説します。
1. 原材料の調達・入荷
サプライチェーン管理のデジタル化
製造業のDXにおいて、AIを活用した需要予測システムを導入することで、最適な調達計画の策定が可能となります。また、ERP(Enterprise Resource Planning)システムを導入することで、在庫と調達管理を統合的に管理できるようになります。さらに、EDI(電子データ交換)の活用により、仕入先との円滑なデータ連携を実現し、調達プロセス全体の効率化を図ることができます。
入荷検品の自動化
入荷プロセスにおいては、RFIDやバーコードスキャナを導入することで、入荷データをリアルタイムで管理することが可能です。また、AI画像認識技術を活用することで、入荷時の不良品検出を自動化し、検品作業の効率化と精度向上を実現できます。
2. 生産計画・工程管理
スマートファクトリー化
製造現場では、スマートファクトリー化が期待されています。IoTセンサーを活用することで、設備のリアルタイムな稼働状況を監視することができます。また、AIによる生産計画の最適化により、需要予測と生産キャパシティを効果的に連携させることが可能となります。
MES(Manufacturing Execution System)の導入
MESを導入することで、工場の生産実績をリアルタイムに可視化し、生産進捗を正確に把握することができます。また、作業員の稼働状況をデータ化することで、作業効率の最適化を図ることが可能です。
デジタルツインの活用
デジタルツイン技術を活用することで、仮想空間上で工場のシミュレーションを実施し、生産ラインの最適化を効率的に進めることができます。
3. 製造(加工・組立)
スマートマニュファクチャリングの推進
製造工程では、AI・機械学習技術を活用することで品質検査の自動化を実現し、検査精度の向上と作業効率化を図ることができます。また、自律型ロボット(AGV/AMR)を導入することで部品供給の最適化が可能となり、さらにCNC機械や3Dプリンタを活用した自動加工システムを導入することで、製造プロセス全体の効率化を実現できます。
予知保全の導入
設備保全においては、IoTセンサーを活用して設備の振動、温度、稼働時間などを常時監視することで、故障が発生する前に適切なメンテナンスを実施することが可能です。また、AI解析を活用することで設備の異常を早期に検知し、ダウンタイムを大幅に削減することができます。
4. 品質管理
AIを活用した品質検査
品質管理プロセスでは、画像解析AIを導入することで外観検査の自動化を実現できます。また、X線や超音波技術とAIを組み合わせることで、内部欠陥の検出精度を高度化し、より確実な品質保証を実現することが可能です。
品質データの一元管理
システムを導入・活用することで、過去の不良履歴やトレーサビリティを一元的に管理することができます。また、蓄積されたデータを分析することで不良の発生原因を特定し、製造プロセスの継続的な改善と品質向上を図ることが可能となります。
5. 在庫管理
倉庫管理システム(WMS)の導入
IoTと組み合わせたWMSを導入することで、在庫状況をリアルタイムで可視化することができます。また、AIによる需要予測に基づいて適正在庫を維持することで、在庫コストの最適化を実現できます。
自動倉庫・ロボット導入
AGVやピッキングロボットのようなマテハン機器を導入することで、物流業務の自動化を推進し、作業効率を大幅に向上させることができます。また、RFIDタグを活用することで、在庫の自動計上や検索時間の削減を実現し、在庫管理業務全体の効率化を図ることが可能です。
6. 出荷・物流
配車の効率化
昨今ではドライバー不足により、出荷のためのトラックの手配が難しくなっています。MOVO Vistaのような配車システムを活用することで、配車における事務作業を削減します。
積み込みの効率化
積み込みの時間を削減することで、全体のリードタイム削減にもつながります。MOVO Berthのようなトラック予約システムを活用することで、トラックの到着時間を事前に把握し、事前準備を効率化できます。
輸配送の最適化
配送ルート最適化システムを活用することで、最適な配送ルートを自動的に計算し、配送効率を向上させることができます。また、MOVO Fleetのような動態管理システムを活用することで、配送状況をリアルタイムで把握し、顧客への納品確認にかかる時間を削減します。
7. データ活用・業務全体の最適化
BI(Business Intelligence)ツールの活用
各工程から収集したデータを統合し、経営層がリアルタイムで状況を把握できる環境を整備することができます。また、AI解析を活用することで、異常値やトレンドを検出し、迅速な業務改善につなげることが可能です。
SCM(サプライチェーンマネジメント)の高度化
需要予測AIやブロックチェーン技術を活用することで、サプライチェーン全体の可視化を実現できます。また、DXを通じてパートナー企業とのデータ連携を強化し、効率的なエコシステムを構築することが可能となります。
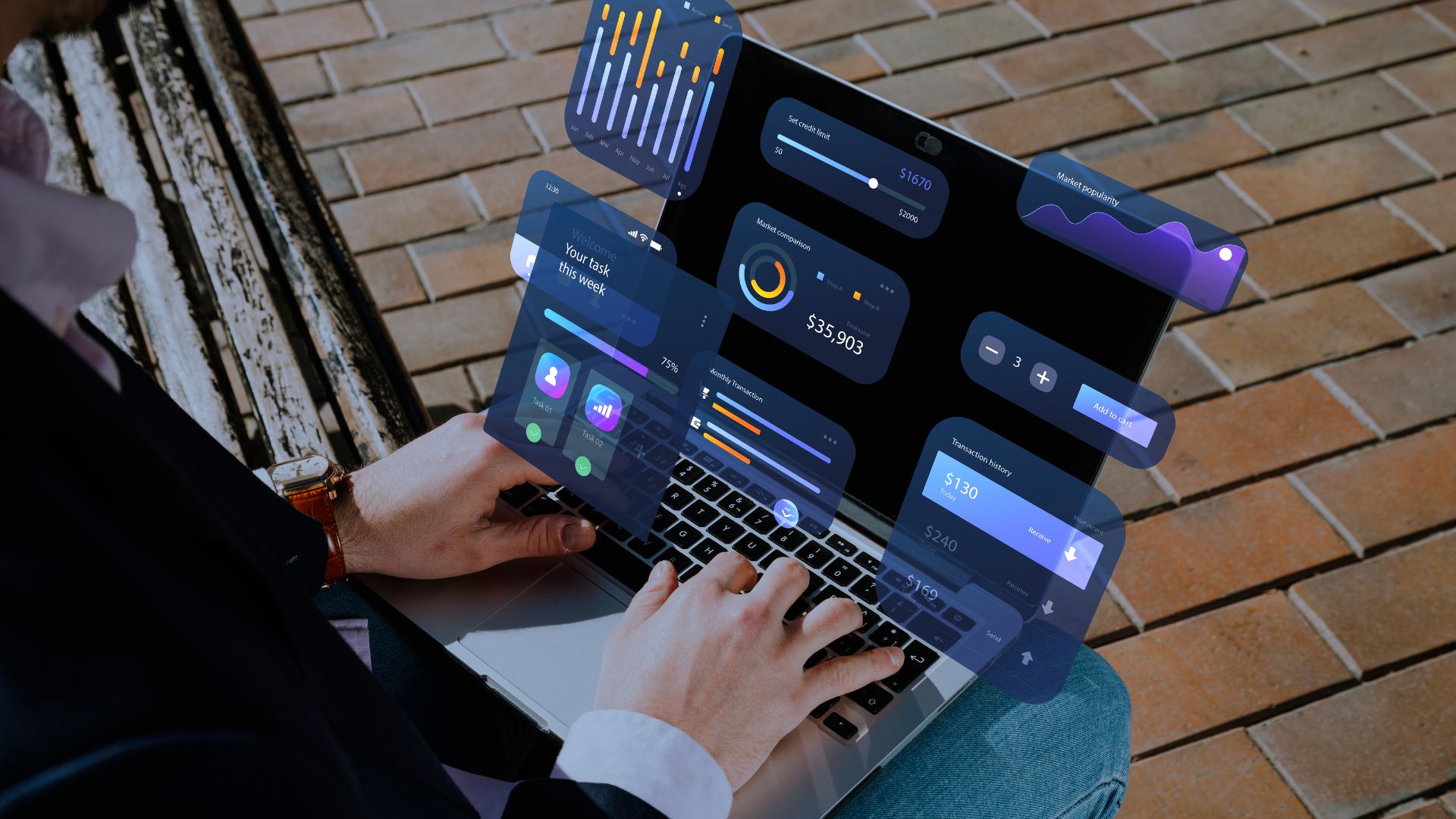
製造業DXの事例
ここからは経済産業省「製造業DX取組事例集」よりDXの取組事例をご紹介します。(2024年に独立行政法人情報処理推進機構が調査した時点の内容です。)
沖電気工業株式会社「バーチャル・ワンファクトリー」
沖電気工業株式会社のバーチャル・ワンファクトリーは、本庄工場と沼津工場を仮想的に1つの工場として融合する取り組みです。部門間融合、生産融合、試作プロセス融合、IT融合の4つの要素で構成され、コスト削減と外部環境変化への対応力強化を目指しています。
この取り組みは、マスカスタマイゼーションへの対応や需要減への危機感から始まりました。従来は各工場で異なる製品を生産し、設計部門も工場ごとに最適化された仕様で設計を行っていたため、共通部品であっても統一的な生産ができない状況でした。
そこで、設計情報の共通化や生産状況の可視化を進め、工場間での生産応援を可能にしました。また、多品種少量生産に強い工場で試作を行うなど、各工場の特徴を活かした体制を構築しました。その結果、2工場の生産規模を維持しながら効率化を実現し、人材や技術の交流も活発化させることで、多品種少量生産のニーズ対応や人手不足への対応力を向上させることができました。
トヨタ自動車株式会社「工場IoT」
トヨタ自動車株式会社の工場IoTは、3D CADデータなどの既存のデジタル化データを一元管理し、工場と現場の部署間で情報共有を行うための基盤です。現有資産の有効活用、AIによる現場課題の解決、FAデータの活用、セキュリティ対策、設備の標準化を目的としています。
従来の地道な改善活動から、より戦略的なアプローチへの転換を図り、まず工場IoTから着手しました。デジタル技術を活用したトヨタ生産方式として、各社員が小規模なテーマを立案・実行するボトムアップの取り組みを進め、社内での教育支援やツール整備も行いました。
その結果、各事業部・工場でプラットフォームを活用したプロジェクトを展開し、費用対効果を上げることができました。現在はこの成果を基に、品質向上や商品力向上など、より広範な付加価値向上に向けたデジタル化へと取り組みを拡大しています。
三菱電機株式会社「e-F@ctory」
三菱電機株式会社のe-F@ctoryは、工場設備IoTで収集した製造現場のデータをエッジコンピューティングでリアルタイムに処理・分析し、さらにITシステムと連携することで、エンジニアリングチェーンとサプライチェーンを含めた生産性向上とコスト改善を実現するシステムです。
同社はFA機器メーカーとしての強みを活かし、FA-IT連携技術、制御技術、産業用ネットワーク技術の開発を進め、自社モデル工場での実証を重ねながらソリューションとして確立しました。顧客ごとに最適化したソリューションを提供し、IoT化の目的や手順を明確にする指標も作成しています。
この取り組みを通じて、パートナー企業との連携プログラム「e-F@ctory Alliance」を発足させ、さらにEdgecrossコンソーシアムへの参画により、互換性のあるサービス展開を実現しました。今後はAI技術の搭載やデジタルツイン構築との連携強化を進める計画です。
ヤマハ発動機株式会社「経営目線デジタル改革」
ヤマハ発動機株式会社は、売上拡大を目指し、経営目線で「既存のビジネスの効率化」と「未来のビジネスの創出」に取り組んでいます。従来の地道な改善活動から戦略的アプローチへの転換を図り、経営陣の意識改革を実施し、グローバル全体での最適化を進めています。
様々なバックグラウンドの人材を集めた「デジタル戦略部」を立ち上げ、「デジタルマーケティング」「コネクテッド」「スマートファクトリー」「データ分析」の4つのテーマで年間数十個のPoCを実施しました。また、社内のソフトエンジニアにデータ分析のトレーニングを行い、事業目的に適した分析ができる人材を育成しています。
これらの取り組みにより、エンジニアリングチェーンの効率化や不良率低減などの成果を上げており、今後はデジタルマーケティングの強化やデジタル改革のリーダー育成を継続していく計画です。
オムロン株式会社「i-BELT」
オムロン株式会社のi-BELTは、FA機器メーカーとしてのノウハウを活かした現場データ活用サービスで、「生産管理」「品質管理」「設備効率」「エネルギー」の4つの領域をカバーしています。このサービスは、顧客企業におけるトップダウンの取り組み(目的や経営指標の提示)とボトムアップの取り組み(効果実感できる改善活動)の連携強化を支援します。
顧客企業の技術や知見を棚卸してコア技術を明確化し、業務プロセスを可視化した上で、価値向上につながる部分のデジタル化を提案します。デジタル化においては、プラットフォームの提供よりも運用の可視化や課題発見に重点を置き、暗黙知のデータ化とナレッジマネジメントを重視しています。
この取り組みにより、製造現場での作業効率の安定化や工具摩耗の削減などの成果を上げ、日本企業のデジタル化推進に貢献しています。今後は人材育成とナレッジ伝承、およびデータ化基盤の整備を進めていく計画です。
製造業DXのカギは物流DXにも取り組むこと
製造業DXは、デジタル技術を活用して製造業の業務プロセスやビジネスモデルを根本的に変革する取り組みです。グローバル競争の激化や消費者ニーズの多様化など、様々な外部環境の変化に対応するため、その重要性は年々高まっています。
製造業DXを推進することで、データドリブンな意思決定の実現や新たなビジネスモデルの創出が期待できる一方、デジタル人材の不足やレガシーシステムの存在といった課題もあります。これらの課題を克服するには、現状分析から始まり、推進体制の構築、デジタル技術の導入、成果の評価と改善という段階的なアプローチが重要です。単なる技術導入にとどまらず、業務プロセスの見直しや組織文化の変革まで含めた包括的な取り組みとして推進することが、持続的な競争力の確保につながります。
また、製造業DXは自社工場内の生産プロセスの最適化にとどまるものではありません。原材料の調達から生産、出荷、輸送、納品といったサプライチェーン全体を見渡し、物流プロセスのDXにも取り組むことが重要です。たとえば、配車の効率化や積み込み時間の短縮、納品時のリアルタイムトラッキングなど、物流DXを推進することで、製造業のDXがより効果的に機能します。
特に、物流領域は人手不足や輸送効率の向上といった課題を抱えており、デジタル技術の活用による変革が求められています。物流DXを製造業DXと一体的に進めることで、調達・生産・輸送・納品がシームレスにつながり、サプライチェーン全体の最適化を実現することができます。
物流DXの具体的な取り組みについては、こちらの記事が参考になります。
なお、Hacobuでは「運ぶを最適化する」をミッションとして掲げ、物流DXツールMOVO(ムーボ)と、物流DXコンサルティングサービスHacobu Strategy(ハコブ・ストラテジー)を提供しています。物流現場の課題を解決する物流DXツール「MOVO」の各サービス資料では、導入効果や費用について詳しくご紹介しています。
トラック予約受付サービス(バース予約システム) MOVO Berth
MOVO Berth(ムーボ・バース)は、荷待ち・荷役時間の把握・削減、物流拠点の生産性向上を支援します。
動態管理サービス MOVO Fleet
MOVO Fleet(ムーボ・フリート)は、協力会社も含めて位置情報を一元管理し、取得データの活用で輸配送の課題解決を支援します。
配車受発注・管理サービス MOVO Vista
MOVO Vista(ムーボ・ヴィスタ)は、電話・FAXによるアナログな配車業務をデジタル化し、業務効率化と属人化解消を支援します。
物流DXコンサルティング Hacobu Strategy
Hacobu Strategyは、物流DXの戦略、導入、実行まで一気通貫で支援します。
関連記事
お役立ち資料/ホワイトペーパー
記事検索
-
物流関連2法
-
特定荷主