デジタルツインとはどのような技術?概要やシミュレーションとの違い、注目される理由、メリット、実現できること、課題を解説
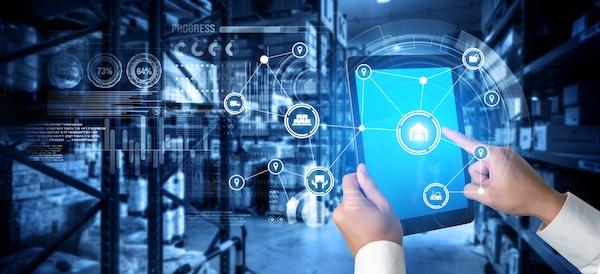
デジタルツインは、実世界の物理的なものをデジタル空間に再現する革新的な技術です。製品やシステム、プロセスなどあらゆる対象を仮想空間内に「双子」として作り出すことで、様々な分析や予測、最適化を可能にします。近年のIoT技術やデータ分析技術の進化により、その実用性と応用範囲が急速に拡大しています。本記事では、物流DXパートナーのHacobuがデジタルツインの基本概念から注目される理由、そして実現できることやメリット・課題について解説します。
デジタルツインとは
デジタルツインとは、物理的な製品、プロセス、システムをデジタル空間に忠実に再現した仮想モデルのことです。実世界のオブジェクトやシステムからリアルタイムでデータを収集し、それを基にデジタル上で動的に表現することで、監視、分析、予測、最適化などを可能にする技術です。
実際の対象物とデジタルツインは常にデータでつながっており、物理世界での変化がデジタルモデルにリアルタイムで反映されます。これにより、現実世界では困難または不可能な実験やシミュレーションをデジタル空間で安全に実行できるようになります。例えば、製造業では製造ラインのデジタルツインを作成し、生産効率の改善策を仮想的にテストしてから実装することが可能です。また、都市計画では都市全体のデジタルツインを構築し、新しいインフラの影響を事前に評価できます。
デジタルツインの構築には、センサーネットワークやIoTデバイスからのデータ収集、高度な3Dモデリング技術、ビッグデータ処理能力、そして人工知能や機械学習による分析能力など、多様な技術要素が必要となります。これらの技術が融合することで、より精緻で実用的なデジタルツインが実現しています。
デジタルツインとシミュレーションの違い
デジタルツインとシミュレーションは似た概念ですが、いくつかの重要な違いがあります。以下4つの主な違いを解説します。
- リアルタイム性
- 用途の広さ
- 双方向性
- 包括性
リアルタイム性
まず最も大きな違いはリアルタイム性です。デジタルツインは実世界のオブジェクトとリアルタイムでデータ連携しており、常に最新の状態を反映します。一方、従来のシミュレーションは特定の条件下での挙動を予測するための静的なモデルであることが多く、実世界の変化に自動的に追随するわけではありません。
用途の広さ
次に用途の広さが異なります。シミュレーションは主に設計段階での検証や予測に使用されますが、デジタルツインは製品やシステムの全ライフサイクル(設計、製造、運用、保守)にわたって活用されます。デジタルツインは対象物の「誕生から終焉まで」の全体を扱うことができます。
双方向性
また双方向性も重要な違いです。デジタルツインは物理世界からデータを取得するだけでなく、分析結果や最適化案を物理世界にフィードバックする双方向の関係性を持ちます。シミュレーションは通常、一方向の分析ツールであり、物理世界への自動的なフィードバックは想定されていません。
包括性
さらに、包括性においても違いがあります。デジタルツインは物理的対象の形状だけでなく、動作特性、性能データ、保守履歴など多面的な側面を含む包括的なモデルです。シミュレーションは特定の側面(例えば構造強度や熱伝導など)に焦点を当てることが多いです。
このように、デジタルツインはシミュレーションの概念を拡張し、より動的で包括的、そして実用的なものへと進化させたものと言えます。
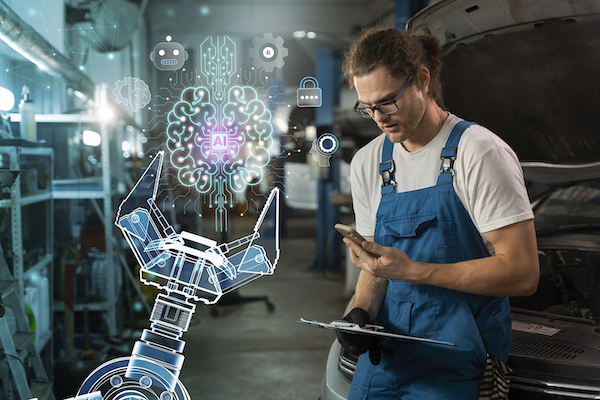
デジタルツインが注目される理由
デジタルツインが近年注目を集める背景にはさまざまな要因があります。
製品開発と予知保全の進化
製品開発では、物理的なプロトタイプを減らし、設計から製造までの時間を短縮できるため、早期に問題を発見できます。また予知保全においては、機械設備の動作をリアルタイムで監視し故障の予兆を検知できるため、計画的な保守が可能になり、突発的な停止を防止できます。
運用最適化と新たなビジネスモデルの創出
運用面では、リアルタイムデータと予測分析を組み合わせることで、エネルギー消費や生産スケジュールの最適化が実現します。さらに、収集したデータを活用して従来の製品販売だけでなくサービス提供や結果ベースの課金など新たなビジネスモデルの創出も可能になります。
複雑なシステム管理
複雑なシステムの管理においても、都市インフラや製造プラント全体の挙動を可視化し、効果的な意思決定を支援します。IoTやAI、クラウド技術の発展により以前は大企業だけのものだった技術が広く普及しつつありますが、データ品質やセキュリティ、専門スキル、初期投資などの課題も存在します。これらは技術進歩や標準化によって徐々に解決されつつあり、デジタルツインの活用は今後さらに広がると考えられています。
デジタルツインのメリット
デジタルツインには以下のようなメリットがあります。
設備保全
デジタルツインを活用することで、実際の設備の状態をリアルタイムで監視し、予測保全が可能になります。センサーから収集したデータを分析することで、設備の劣化や不具合を事前に検知し、計画的なメンテナンスを実施できます。これにより、突発的な故障による生産ラインの停止を防ぎ、設備の稼働率を向上させることができます。また、メンテナンス作業のシミュレーションを事前に行うことで、効率的な保全計画の立案も可能になります。
品質向上
デジタルツインによる仮想環境では、製品の設計段階から様々な条件下でのシミュレーションが可能です。これにより、実際の製造前に製品の性能や品質を検証し、潜在的な問題を早期に発見・解決できます。また、製造プロセスのデジタルツインを構築することで、各工程のパラメータ最適化が可能となり、製品の均一性や精度が向上します。さらに、品質データの継続的な収集と分析により、製造プロセスの改善点を特定し、継続的な品質向上を実現できます。
リスク低減
デジタルツインを活用することで、実際の環境で発生する可能性のあるリスクを事前に特定し、対策を講じることができます。設備の故障リスク、安全リスク、製品不良リスクなど、様々なリスクをシミュレーションによって予測し、対応策を検討することが可能です。また、仮想環境での試験により、危険を伴う実験や検証を安全に行うことができ、作業者の安全確保にも貢献します。さらに、市場変動や供給チェーンの問題などの外部リスクに対しても、シナリオ分析を通じて柔軟な対応策を準備できます。
期間短縮
製品開発プロセスにデジタルツインを導入することで、設計から生産までの期間を大幅に短縮できます。仮想環境での設計検証により、試作回数を削減し、設計変更の迅速な反映が可能になります。また、生産ラインのデジタルツイン上で事前に生産プロセスを最適化することで、立ち上げ期間の短縮や生産効率の向上を実現できます。市場投入までの期間短縮は、競争力強化や市場ニーズへの迅速な対応につながります。さらに、顧客要求の変更にも柔軟かつ迅速に対応することが可能になります。
コストダウン
デジタルツインの活用により、様々なコスト削減効果が期待できます。試作品製作コストの削減、設備投資の最適化、エネルギー消費の効率化などが主な例です。予測保全によるダウンタイムの減少は、生産性向上とコスト削減に直結します。また、製造プロセスの最適化により、原材料の無駄を削減し、歩留まり向上を実現できます。さらに、設計変更や不具合対応にかかるコストも低減できるため、トータルコストの削減につながります。長期的には、製品のライフサイクル全体を通じたコスト管理が可能になります。
アフターサービスの充実
デジタルツインは製品の納入後も顧客サポートに大きく貢献します。納入済み製品の状態を遠隔監視することで、予防保全の提案や最適な運用アドバイスを提供できます。また、不具合発生時には、デジタルツイン上で原因究明と解決策の検証を行い、迅速かつ的確な対応が可能になります。さらに、製品の使用状況データを分析することで、顧客ごとにカスタマイズされたサービス提案や製品改良にも活かせます。これにより、顧客満足度の向上と長期的な信頼関係の構築が実現します。製品のアップグレードやリプレースの最適なタイミング提案など、製品ライフサイクル全体をサポートするサービスも展開可能です。
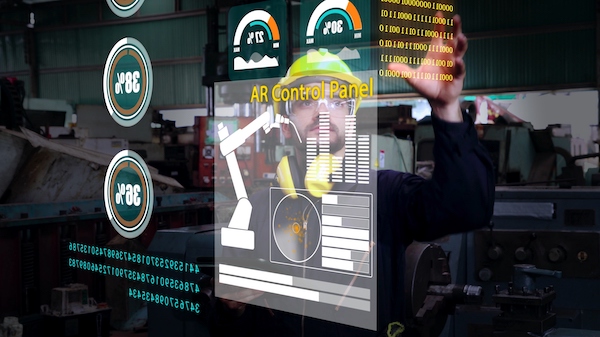
デジタルツインで実現できること
生産プロセスの最適化
デジタルツインを活用することで、製造ラインの稼働状況をリアルタイムでモニタリングし、生産プロセス全体を可視化できます。収集されたデータを基に、生産スケジュールの最適化や設備の稼働率向上が可能になります。また、仮想空間でさまざまな生産条件をシミュレーションすることで、最適なパラメータ設定や工程配置を導き出せます。これにより、生産リードタイムの短縮、材料ロスの削減、エネルギー効率の向上など、生産効率を総合的に高めることができます。さらに、異常検知機能により、品質問題の早期発見と迅速な対応も実現します。
予知保全の実現
デジタルツインによって設備の状態をリアルタイムで監視し、収集したデータをAIで分析することで、設備の故障や性能低下を事前に予測できます。これにより、従来の定期保全から予知保全へと移行し、最適なタイミングでのメンテナンスが可能になります。設備の異常兆候を早期に検知することで、重大な故障を未然に防ぎ、予期せぬダウンタイムを大幅に削減できます。また、部品交換の最適なタイミングを予測することで、過剰なメンテナンスを回避しつつ、設備の寿命を延ばすことができます。これにより、保全コストの削減と設備稼働率の向上を同時に実現します。
製品開発の効率化
デジタルツインを製品開発プロセスに導入することで、設計段階から製品の性能や信頼性を仮想空間で検証できます。様々な使用条件や環境下でのシミュレーションにより、実機製作前に設計の最適化が可能になり、試作回数の削減と開発期間の短縮が実現します。また、設計変更の影響を迅速に評価できるため、問題の早期発見と解決が容易になります。さらに、製造プロセスとの整合性を設計段階から確認できるため、設計から生産への移行もスムーズになります。顧客要求の変化にも柔軟かつ迅速に対応できるため、市場競争力の強化につながります。
遠隔作業支援と技能伝承
デジタルツインを活用した拡張現実(AR)や仮想現実(VR)技術により、熟練作業者の技能や知識を効果的に伝承できます。現場の設備や製品の3Dモデルとリアルタイムデータを組み合わせることで、遠隔地からの作業指導や支援が可能になります。複雑な作業手順や点検方法をデジタル化し、視覚的に分かりやすく表示することで、未熟練者でも高度な作業を行えるようになります。また、熟練者の作業を記録・分析し、暗黙知を形式知化することで、貴重な技能やノウハウを組織全体で共有・活用できます。これにより、人材不足や高齢化といった課題への対応も可能になります。
製品のライフサイクル管理
デジタルツインにより、製品の設計・製造から使用・廃棄までのライフサイクル全体を一元管理できます。製品の使用状況や性能データをリアルタイムで収集・分析することで、製品の最適な運用方法や保守計画を提案できます。また、実際の使用環境下での製品挙動を把握することで、次世代製品の開発に活かせる貴重な知見が得られます。さらに、製品のアップグレードやリプレースの最適なタイミングを予測し、顧客に提案することも可能になります。廃棄・リサイクル段階においても、材料の分別や再利用を最適化するための情報提供ができ、環境負荷の低減に貢献します。
社会課題の解決
デジタルツインは製造業だけでなく、都市計画、交通システム、エネルギー管理、医療など幅広い分野で社会課題の解決に貢献します。都市のデジタルツインでは、交通流の最適化による渋滞緩和やエネルギー消費の効率化、災害シミュレーションによる防災対策の強化などが可能になります。また、医療分野では患者個人のデジタルツインを作成し、個別化医療や治療法の最適化に活用できます。さらに、環境モニタリングと連携したデジタルツインにより、CO2排出量の削減や資源の効率的利用など、持続可能な社会の実現に向けた取り組みを支援します。多様なデータを統合・分析することで、複雑な社会システムの相互依存関係を理解し、総合的な解決策を導き出すことができます。
デジタルツインの活用における課題
デジタルツインは多くの可能性を秘めていますが、実際の導入と活用には様々な課題が存在します。これらの課題を理解し適切に対処することが、デジタルツイン活用の成功には不可欠です。
技術的課題
技術面では、シミュレーションの精度向上とデータ処理・管理が大きな課題となっています。
シミュレーション精度の向上
デジタルツインの価値はシミュレーションの精度に大きく依存します。現実世界の複雑な物理現象や相互作用を正確にモデル化することは容易ではありません。特に多様な要素が絡み合う製造プロセスや都市環境などでは、全ての変数を考慮したシミュレーションの構築が困難です。また、予測モデルの精度向上には継続的な検証と調整が必要であり、この精度向上のプロセス自体が技術的チャレンジとなっています。
データ処理と管理
デジタルツインは膨大な量のデータを扱います。センサーから継続的に送られてくるリアルタイムデータの処理、蓄積されたヒストリカルデータの管理、そしてこれらのデータから意味のある洞察を引き出すための分析技術など、データに関する課題は多岐にわたります。さらに、データの品質保証や欠損データへの対応方法も重要な課題です。
システム統合の課題
異なるシステム間の連携、特にレガシーシステムとの統合は大きな障壁となります。
レガシーシステムとの連携
多くの企業や組織では、長年にわたって構築されてきた既存のシステムが稼働しています。これらのレガシーシステムはデジタルツインとの連携を想定して設計されていないため、データ形式の違いやインターフェースの互換性などの問題が生じます。また、古いシステムからのデータ抽出や変換にも技術的な困難が伴うことが多く、システム統合のプロセスが複雑化する要因となっています。
人材と組織の課題
デジタルツイン活用の成功には、技術だけでなく人材と組織の側面も重要です。
デジタル人材の確保・育成
デジタルツインの開発と運用には、データサイエンス、AIモデリング、IoT技術など、多様な専門知識を持つ人材が必要です。しかし、これらのスキルを持つ人材は市場でも需要が高く、確保が難しい状況です。また、既存の従業員に対する継続的な教育と研修も重要ですが、急速に進化する技術に対応した教育プログラムの構築自体が課題となっています。
組織体制の整備
デジタルツインの導入は、単なる技術導入にとどまらず、業務プロセスや意思決定方法の変革を伴います。従来の組織構造や部門間の壁がデジタルツイン活用の障壁となることが多く、横断的なチーム編成や柔軟な組織体制の構築が求められます。また、データドリブンな文化への移行も組織的な課題の一つです。
コストと投資の課題
デジタルツイン導入には相当の初期投資が必要です。センサーネットワークの構築、データ収集・分析インフラの整備、専門人材の確保など、様々な面でコストが発生します。これらの投資に対する明確なROI(投資収益率)の見通しが立てにくいことも、経営判断を困難にする要因となっています。また、継続的な運用と更新にかかるコストも考慮する必要があります。
これらの課題は相互に関連しており、総合的なアプローチで取り組むことが重要です。技術の進化や成功事例の蓄積により、徐々にこれらの障壁は低くなっていくことが期待されますが、現時点ではデジタルツイン活用の道のりには慎重かつ戦略的な計画が必要です。
まとめ
デジタルツインは実世界の対象をデジタル空間に忠実に再現し、リアルタイムでデータ連携する技術です。従来のシミュレーションと異なり、リアルタイム性と双方向性を備え、製品やシステムのライフサイクル全体をカバーします。
この技術により、生産プロセスの最適化、予知保全の実現、製品開発の効率化、遠隔作業支援などが可能になり、製造業だけでなく都市計画や医療など様々な分野で活用されています。
課題としては、シミュレーション精度の向上、データ処理・管理、専門人材の確保、初期投資コストなどがありますが、技術の進化とともに解消されつつあります。デジタルツインはDX推進の中核技術として、企業の競争力強化と持続可能な社会の実現に貢献していくでしょう。
関連記事
お役立ち資料/ホワイトペーパー
記事検索
-
物流関連2法
-
特定荷主