ミルクランとは?仕組みやメリット・デメリット、他の輸送方式との違い、導入手順などについて解説
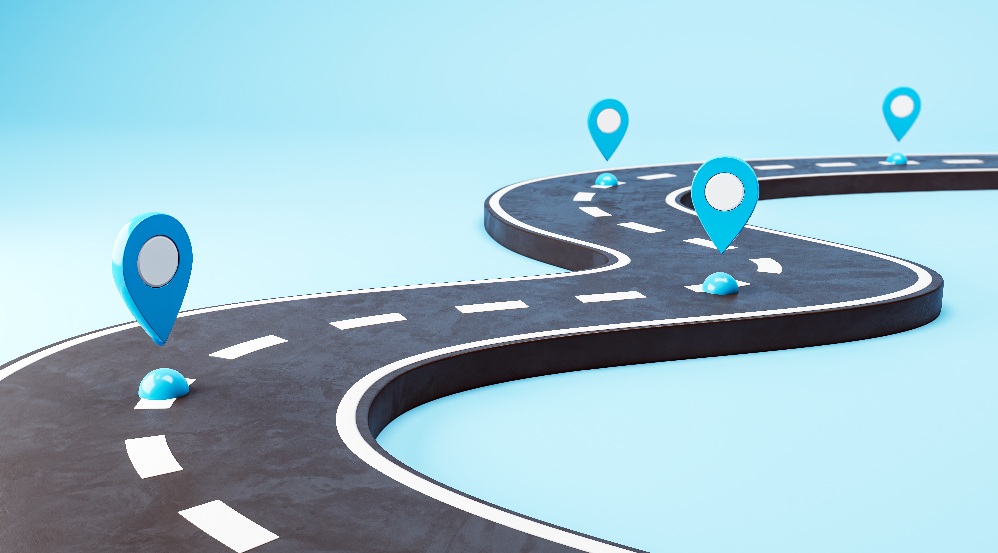
ミルクラン方式は、物流領域における効率的な輸送方式の1つです。本記事では、ミルクラン方式の仕組みやメリット・デメリット、他の輸送方式との違い、導入手順などについて、物流DXパートナーのHacobuが解説します。
Point ミルクランを成功させるカギは、現状を正確に把握したうえで、ルート組み替え計画と検証を高精度かつ短サイクルで回すことです。最適なデータ取得システムの詳細は、以下のリンクからご覧いただけます。
目次
ミルクランとは
ミルクランの基本概念やその由来について詳しく説明します。
ミルクランの概要
ミルクランとは、メーカーが原材料や部品を調達する際、メーカー側が車両を手配し、複数のサプライヤーを巡回して集荷する輸送方式を指します。
ミルクランという名称の由来
名前の由来は、牛乳メーカーが牧場を回って原乳をまとめて集める 「milk run」 にあります。一般的に、牛乳メーカーは牧場から牛乳を調達する際、それぞれの牧場が車両を手配して工場に配送しに行くのではなく、工場から出す集乳ローリーが各牧場の酪農家のもとを回り、まとめて集乳を実施しています。この考え方が自動車や建設機械など、さまざまな業界に応用されています。
ミルクランの採用事例
たとえば、自動車メーカーの工場では、生産ラインへ投入する時刻に合わせて多頻度・少量の Just‑in‑Time(JIT) 納品を行います。一方、サプライヤーは物流費を抑えるため荷物をまとめたいと考えます。両者の要件を両立させる方法として、サプライヤーを巡回して集荷するミルクラン方式が採用されています。
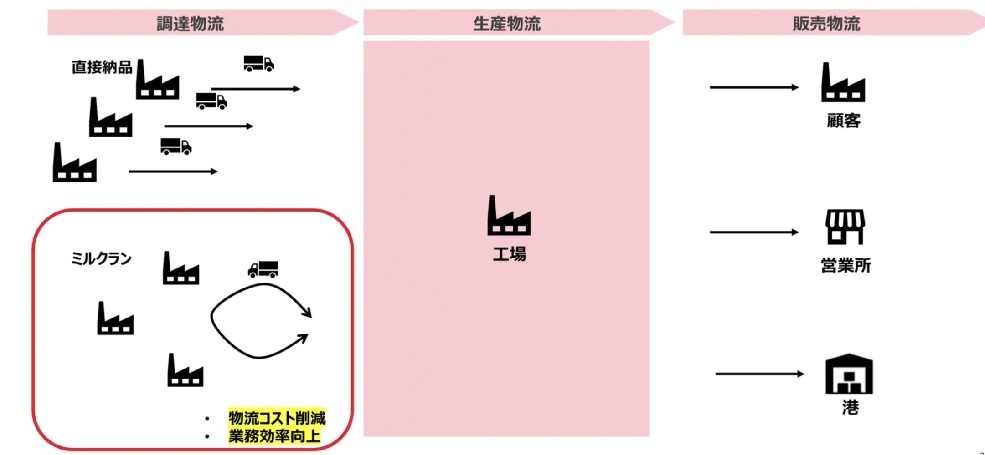
ミルクラン方式の仕組みと特徴
従来の輸送方式との違い
従来(直接方式):サプライヤーが個別に配送・集荷を手配
ミルクラン:メーカーが車両を手配し、複数サプライヤーの軒先を回って一括集荷
ミルクランは、車両稼働率の向上と輸送費削減に加え、統合的な運行計画により配送時間の一貫性やサービス品質の向上も期待できます。
共同輸配送の一種
ミルクラン方式では、特に1つのサプライヤーからの納品量が車両1台に満たない場合に用いることが効果的です。複数のサプライヤーの原材料や部品を1台の車両に乗せることから、ミルクラン方式は巡回集荷とも呼ばれる共同輸配送の一種とも言えます。
ミルクランのメリット
輸送費の明確化
サプライヤー負担だった輸送費をメーカーが負担・管理することで、仕入れ原価と輸送費を切り分けて把握できます。
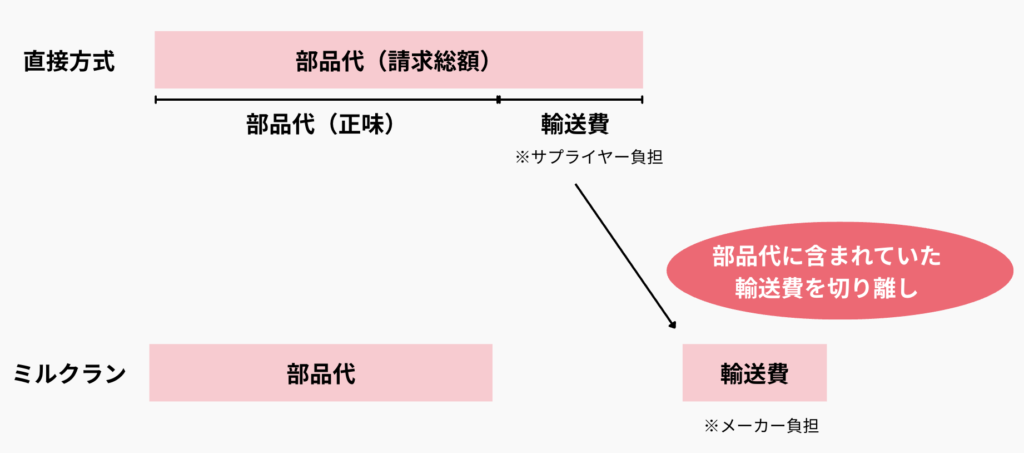
輸送費の削減
1 台の車両で集荷を集約するため積載効率が向上し、単位あたりの輸送コストが削減されます。最適なルートをメーカー自ら設計することで、総走行距離も短縮でき、燃料費・人件費も抑えられます。
ドライバー不足への対応
走行回数を減らし車両当たりの積載効率を高められるため、必要なドライバー数を大幅に低減できます。確保が難しいドライバーを過剰に抱える必要がなく、生産計画の変動時も臨時便を増車するリスクが低減します。
運行管理業務の効率化
ルートと納品時刻が一元化され、輸送指示・車両手配・到着確認といった管理業務を効率化・平準化できます。
荷受け・検品効率の向上
納品回数が減り、荷受けや検品をまとめて処理できるため庫内作業の中断が減少します。
保管費の削減
JIT調達により安全在庫を減らし、倉庫スペースと運転資金を圧縮できます。
CO2排出量の削減
車両台数と走行距離を削減することで燃料消費が抑えられ、環境負荷低減につながります。
ミルクランのデメリット
ミルクランにもデメリットはあります。
輸送費が高くなるケース
集荷先が近距離圏内にまとまっていない場合、かえって輸送費が高くなる可能性があります。巡回ルートに遠方が混ざるだけで走行距離と拘束時間が膨らみ、輸送費は一気に上昇します。
さらに、車両制限や荷受けスペース不足で大型車が入れないサプライヤーがあると、その拠点だけ別便や小型車を手配せねばならず、結局サプライヤー別集荷よりコスト高になる恐れがあります。
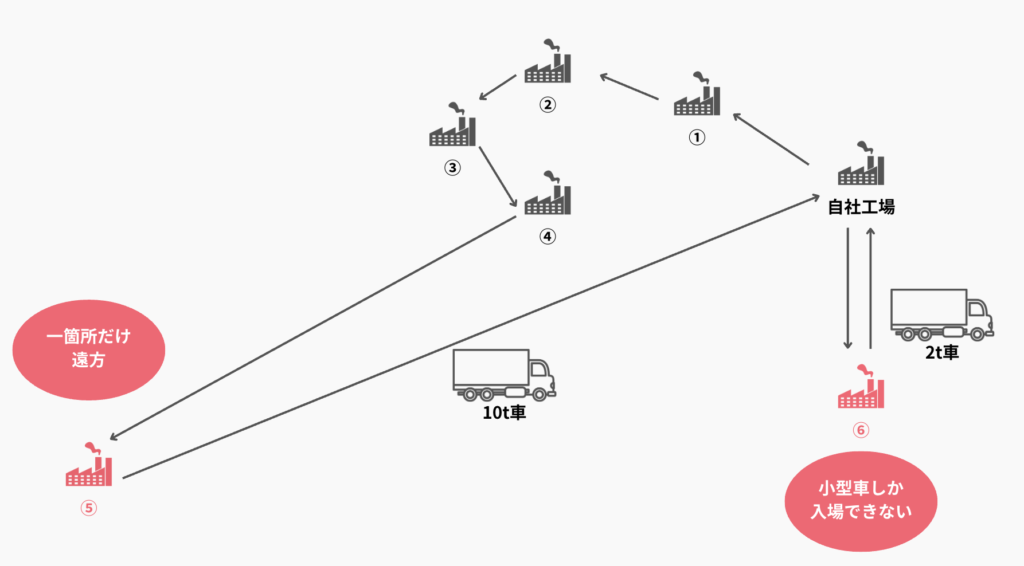
集荷時間の調整が難しい
ミルクランでは一台の車両で複数サプライヤーを順番に回るため、集荷時間を分刻みで設定する綿密なスケジュールと厳格な時間管理が不可欠です。
道路渋滞・工事・荷待ち・荷受け人員不足など予期せぬ遅延が一箇所で生じるだけで後続の集荷が連鎖的にずれ込み、制限時間内に全てを回り切れなくなる場合があります。
積載率の調整が難しい
ミルクランでは一台の車両が複数のサプライヤーから荷物を段階的に積み増していくため、途中で過積載にならないよう各社の引取り量を精密に配分・調整しなければなりません。
需要変動や梱包サイズのばらつきがあると計画どおりに積載率を保つのが難しく、載せ切れずに追加便が発生したり、逆に空きスペースを残して非効率な輸送となるリスクが高まります。
サプライヤーからの理解を得ることが難しい
ミルクラン導入にはサプライヤーの理解が不可欠ですが、障壁も少なくありません。まず、積込時刻やロット管理の見直しにはオペレーションの変更やシステム改修などの追加コストが発生します。
また、長年付き合いのある運送会社との委託を打ち切ることへの心理的抵抗があります。もし、従来の直送納品において、運賃に利益を上乗せしてきた場合、その収益が薄まることを懸念する場合もあります。
ミルクラン方式と他の輸送方式の比較
ミルクラン方式以外にもさまざまな輸送方式が存在します。本章では、ミルクラン方式と他の主要な輸送方式を比較し、その特徴や利点・欠点について解説します。
直送方式との比較
直送方式は特定のルートに縛られない柔軟性があります。一方で、複数の取引先を一括して扱わないため、輸送費が高くなる場合があります。ミルクラン方式は、集約配送によりコストを削減する一方で、ルート設定やスケジュール管理が複雑になることがあります。
ハブ・スポーク方式との比較
ハブ・スポーク方式は、中央のハブ拠点から放射状にスポーク(支線)が伸びる物流ネットワークを指します。一方、ミルクラン方式は、複数の取引先を巡回する形で運行するため、より柔軟なルート設定が可能です。
両方式とも効率化を目指していますが、ハブ・スポーク方式は規模の大きな物流ネットワークに適しており、ミルクラン方式は柔軟性とコスト削減を重視する場合に適しています。
クロスドッキング方式との比較
クロスドッキング方式は、商品の仕分けや集約を効率化するための物流手法であり、商品の倉庫での保管時間を極力短縮し、そのまま次の配送先へと直行させる方式です。
ミルクラン方式と比較すると、クロスドッキング方式は在庫を最小限に抑え、迅速な配送を実現する点が特徴です。一方、ミルクラン方式は複数の取引先を効率的に巡回することで輸送費を削減することに重点を置いています。
ミルクランが活用されている業界
自動車業界
自動車業界では、数百社に及ぶ部品サプライヤーが半径100 km圏内に集積し、1日数回のJIT納入が行われています。ミルクランで巡回集荷すれば車両台数と在庫が同時に削減でき、ライン停止リスクも抑えられます。
電機・精密機器業界
基板・コネクタなど小型・高単価部品を多品種少量で調達するため、小口便が乱発しがちです。ミルクランなら複数メーカーからの集荷を一本化しつつ、梱包寸法を揃えて積載効率を最大化できるため、輸送費と破損リスクの双方を低減できます。短サイクルの新製品立ち上げ時にもルートを柔軟に組み替えやすい点が適合理由です。
食料品業界
鮮度維持が求められる原材料やパッケージ資材を短いリードタイムで調達しなければならず、温度帯別に車両や積載スペースを区切る必要もあります。ミルクランで集荷時間を細かく設定し、定温車を効率活用すれば、ハンドリング回数を減らしつつ鮮度とトレーサビリティを確保でき、食品ロス削減と環境負荷低減の両立が図れます。
ミルクランが難しい業界
鉄鋼・セメントなど重量バルク材業界
製品は比重が高く、1社目で車両の最大積載重量に達してしまう場合、複数拠点を巡回できません。荷役にも天井クレーンやサイロが必要で停車時間が長く、ルート途中での積み下ろしが現実的でないことから、ミルクランの経済性・機動性を活かしにくいことが一般的です。
石油・化学液体業界
石油製品や危険物化学品は、それぞれ専用タンクローリーと洗浄工程が必要で混載が禁じられています。途中での残液リスクや温度・圧力管理も厳しく、1便で複数サプライヤーを回ると品質事故や設備洗浄コストが跳ね上がるため、単独直行便が原則となりミルクラン運用は難度が高くなります。
建設・住宅資材業界
工事現場への納入は「決まった日に大型資材を一括搬入する」ケースが多く、現場ごとに必要量と搬入時間が日々変動します。道路幅やクレーン手配など現地条件も個別対応が必須なうえ、天候や工程ずれで直前変更が頻発するため、定時ルートを組んで複数現場を巡回するミルクランとは相性が悪いとされています。
ミルクラン方式導入の手順とポイント
ミルクラン方式を導入する際の具体的な手順と注意すべきポイントについて解説します。
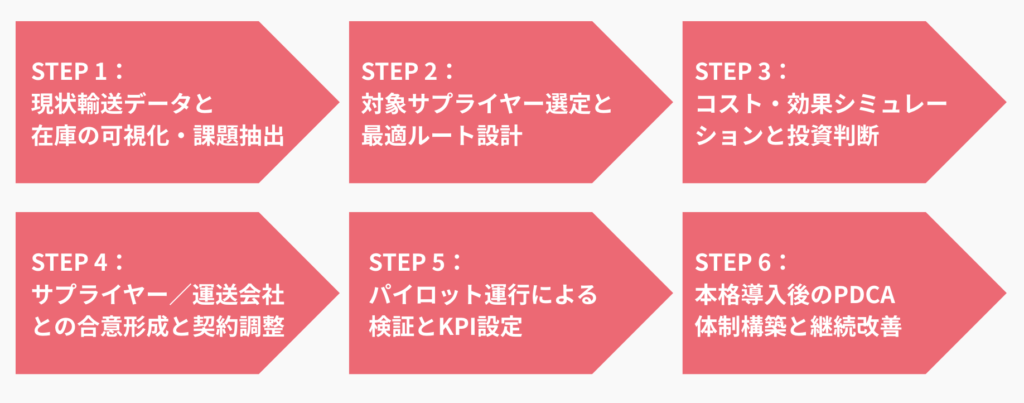
STEP 1:現状輸送データと在庫の可視化・課題抽出
まずはメーカーとサプライヤー双方の輸送データ(車両台数・走行ルート・積載率・荷待ち時間)と在庫推移、発着時刻記録を月次・日次で収集し、現場ヒアリングでムダや制約条件を洗い出します。そしてBIツールなどを活用し、総走行距離やリードタイム、荷待ちロス、安全在庫などを指標化し、現行KPIと比較してギャップを可視化します。
ボトルネックと潜在コストを定量的に把握することで、改善余地と優先順位を明確化し、次工程のルート設計や投資判断の土台を構築します。ここで数値精度を高めておけば、後続工程の議論がスムーズになります。
STEP 2:対象サプライヤー選定と最適ルート設計
可視化結果を基に、地理的近接性・発着頻度・荷量の変動幅を評価し、ミルクラン効果が大きいサプライヤー群を選定します。GIS(Geographic Information System)やルート最適化システムで巡回順序と時間帯をシミュレーションし、法定拘束時間内に収まるルート案を複数作成して概算走行距離やCO2排出量などを算出します。
この際、積込待機時間や工場受入能力をパラメータに含め、将来増産時の拡張性も検証することが重要です。併せて安全在庫への影響も試算します。
STEP 3:コスト・効果シミュレーションと投資判断
選定したルート案ごとに車両費、燃料費、ドライバー人件費、倉庫削減効果、CO2削減量をモデル化し、現行コストとの差異を月次・年次で試算します。シミュレーションでは拘束時間規制や燃料単価変動、生産計画の季節変動をシナリオに織り込み、投資回収期間とIRRを算出します。
併せてドライバー削減数やCO2削減率を非財務KPIとして提示し、経営層とサプライチェーン部門で投資判断を行います。必要投資としてシステム導入や荷受設備改修費などを含め、キャッシュフローへの影響を把握します。
STEP 4:サプライヤー/運送会社との合意形成と契約調整
試算を基にサプライヤーと運送会社に説明会を開き、目標コストとKPIを共有します。運送会社には臨時便・逆回送の扱いや車両仕様を明示することが有効でしょう。
サプライヤーとは納品時刻、ロットサイズ変更、EDI連携など新オペレーションを協議し、必要経費や利益調整を合意文書に反映させます。反発が予想される場合は試験期間中の補填策や共同改善会議を設け、信頼醸成を図ることが円滑導入の鍵となります。
STEP 5:パイロット運行による検証とKPI設定
合意後は影響度の小さいルートから3〜6か月のパイロット運行を開始します。車載端末や動態管理システムで走行距離、積載率、遅延時間、荷受トラブルなどをリアルタイム収集し、週次でKPI達成度をレビューします。
課題が出た場合はルート再編や待機調整を即時反映し改善サイクルを回すことで、本格展開前に運用リスクと追加コストを最小化します。併せてドライバーの作業負荷や安全面のフィードバックをアンケートで取得し、教育内容や休憩計画をブラッシュアップします。
STEP 6:本格導入後のPDCA体制構築と継続改善
パイロットで確立したKPIと改善手順を標準化し、月次レビューと四半期ごとの刷新会議を設定します。動態管理システムからデータを集計し、走行距離や在庫日数が逸脱した際に即アラートを出す体制を構築します。またESG評価や顧客要求に応じて環境指標をレポートし、競争力を同時に高める循環的なPDCAを回し続けます。
新たなサプライヤーをミルクランに組み込む場合
新たなサプライヤーをミルクランに組み込む際には、既存ルートの組み替えや新規ルート再設計のために、運行実態を「現ルート」と「新拠点」の両側面から詳細に把握することが不可欠です。
まず既存ルートでは、拠点ごとの平均滞在時間と拠点間の平均移動時間を洗い出し、サプライヤー別に部材の形状・荷姿・量まで整理します。
同じ粒度で、新たに組み込むサプライヤーの所在地・部材属性・出荷量も収集し、ルート負荷を正確に予測します。
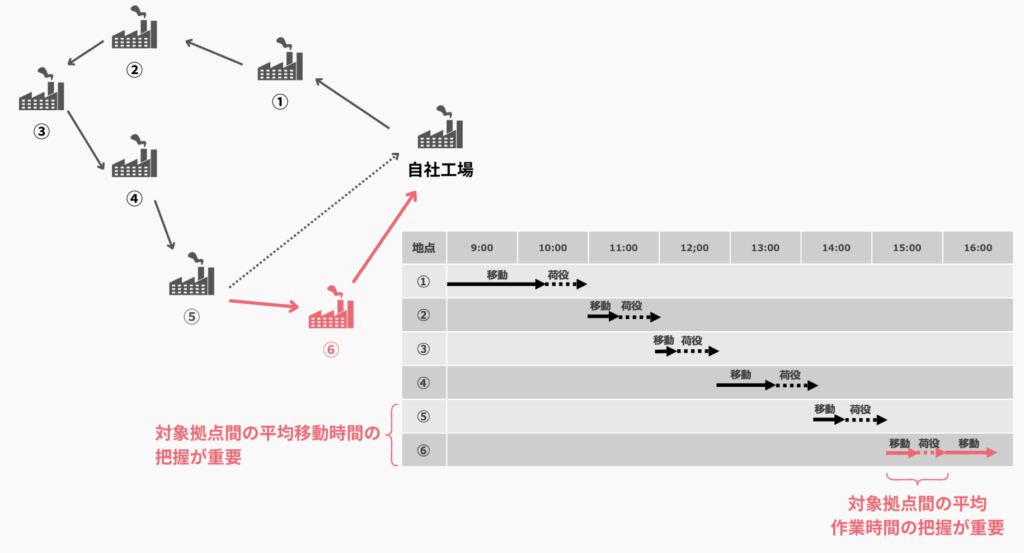
ミルクランのデータ取得ならMOVO Fleet
前述のような一連のデータ取得には動態管理サービス MOVO Fleet(ムーボ・フリート)が有効です。MOVO Fleetは、既存ダイヤの運行実態を詳細に把握しながら、新たな集荷先を組み込む計画作りをサポートします。
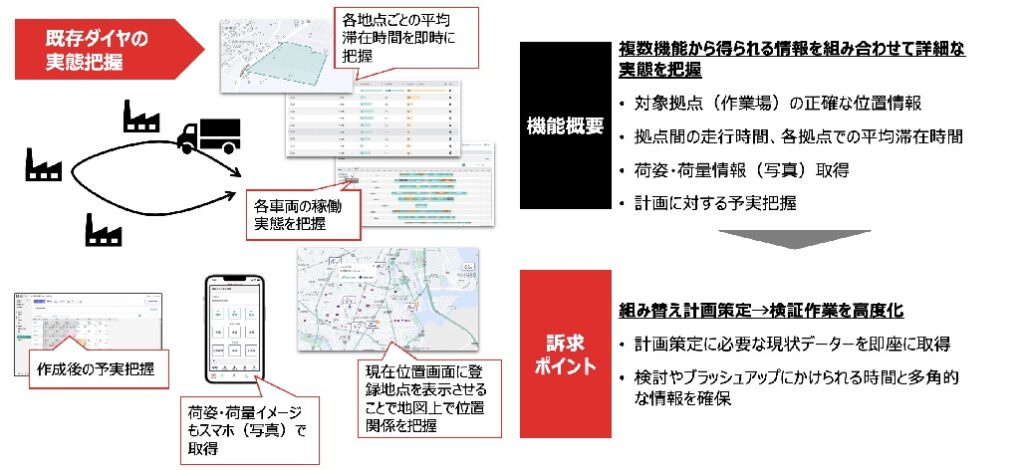
複数機能から得られる情報を組み合わせて詳細な実態を把握
現在位置画面に登録地点を表示させることで、地図上で既存・新規のサプライヤー工場や自社工場の位置関係を把握できます。
また、GPSログから、拠点間の走行時間や各拠点での平均滞在時間を把握できるだけでなく、ドライバーがスマートフォンの専用アプリを活用することで、荷姿・荷量情報を取得できます。 そして配送計画に対する予実把握も可能です。
組み替え計画策定→検証作業を高度化
前述の機能を活用し、新たなミルクラン計画策定に必要な現状データを即座に取得することで、検討やブラッシュアップにかけられる時間と多角的な情報を確保し、組み替え計画策定→検証作業を高度化できます。
MOVO Fleetの詳細は以下よりダウンロードいただけます。
関連記事
お役立ち資料/ホワイトペーパー
記事検索
-
物流関連2法
-
特定荷主