ECRSとは?概要や注目される理由、4ステップの改善手法、メリット、物流領域に求められる理由、導入のポイントなどを解説
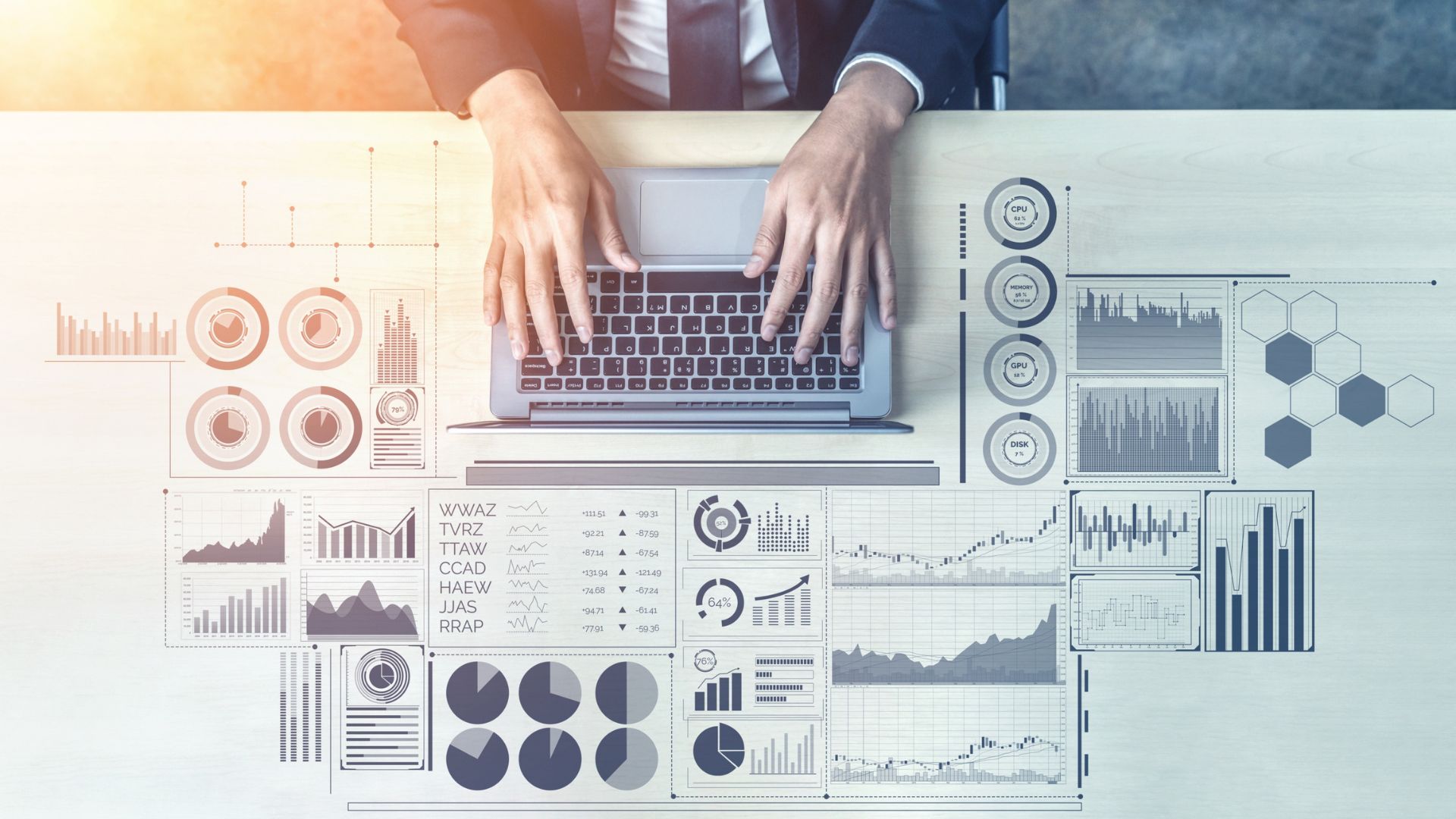
ECRSとは、業務のムダを洗い出して効率を向上させるためのフレームワークです。製造業や小売業、卸業などの荷主にとって、物流の効率化は企業の競争力を高める要素であることから、ECRSのフレームワークも注目を集めています。本記事では、ECRSという業務効率化のフレームワークについて、物流DXパートナーのHacobuが解説します。
なお、Hacobuでは物流DXの戦略、導入、実行まで一気通貫で支援する物流DXコンサルティング「Hacobu Strategy」を提供しています。物流業務の改善にお悩みがありましたら、以下をクリックしてご覧ください。
目次
ECRSとは
まずは、ECRSの基本的な内容を解説します。
ECRSの概要
ECRSは、業務のムダを洗い出して効率を向上させるためのフレームワークで、「Eliminate(排除)」「Combine(結合)」「Rearrange(再配置)」「Simplify(簡素化)」の頭文字から構成されます。
製造現場の改善手法として広く活用されてきましたが、現在では小売や物流、サービス業など多様な領域で注目されています。
ECRSの背景
ECRSはトヨタ生産方式などのリーン生産思想とも共通点が多く、“ムダの徹底排除”を根幹としています。グローバル競争が激化する中、効率化や生産性向上の必要性が叫ばれるようになり、ECRSもあらためて見直されるようになりました。
ECRSが注目される理由
本章では、ECRSが注目される理由を解説します。
シンプルかつ実践的なフレームワーク
ECRSは誰でも理解しやすい4つのステップによって構成されています。チェックリスト感覚で業務改善に取り組めるため、現場担当者から経営層まで幅広い層で実践しやすい点が特徴です。
幅広い業種・業態に適用可能
ECRSは、製造ラインだけでなく、事務作業の効率化や物流倉庫内の動線見直し、小売店舗の陳列方法改善など、多種多様な業務に対応できます。単純な作業から高度なオペレーションまで適用範囲が広いため、あらゆる企業で導入しやすいフレームワークです。
成果が見えやすく継続しやすい
改善内容が具体的で目に見えやすいため、社内で成果を共有しながら進めることができます。小さな改善を積み重ねることで、社内の改善意識を高めやすく、継続的な効率化に繋がります。
ECRSの4ステップ
本章では、ECRSの4つのステップを解説します。それぞれのステップを踏むことで、無理なく着実に業務のムダを削減し、生産性を高めることができます。
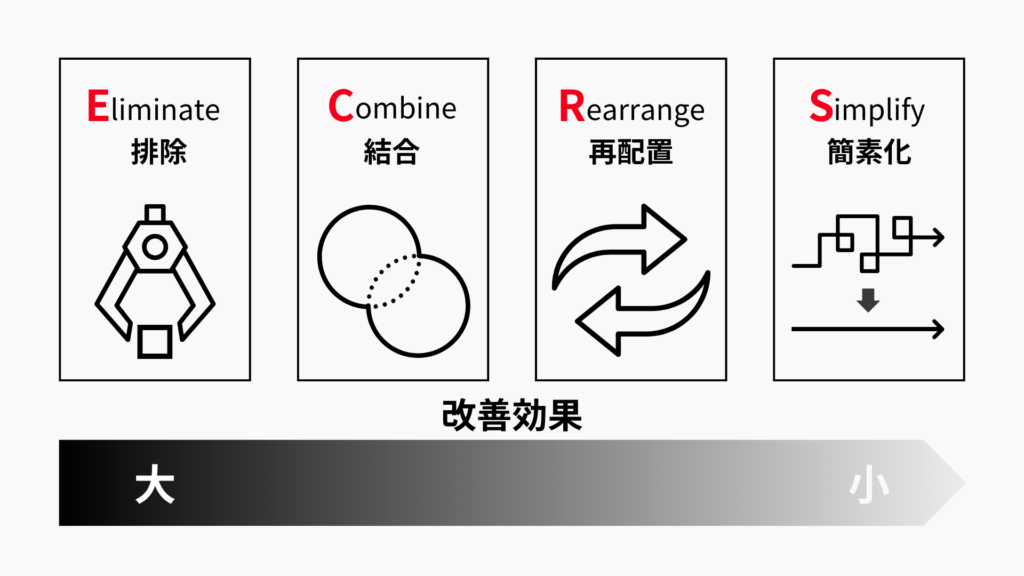
1. Eliminate(排除)
意味と目的
「排除」では、現行の業務プロセスにある不要な作業や非効率な手順を取り除くことに焦点を当てます。
具体例
- 製造ラインでの重複検品を廃止する
- 事務作業で不要になった帳票を作成しない
- 物流倉庫で使われなくなった棚を撤去する
2. Combine(結合)
意味と目的
「結合」では、類似作業や関連作業をまとめて行うことで効率を上げ、手戻りやムダな移動を減らします。
具体例
- 製造ラインで複数部品の組立工程をひとつの作業ステーションに集約する
- 小売店舗でまとめて発注できる商品は同時にオーダーする
- 物流センターで荷捌きと検品を同じ場所で行う
3. Rearrange(再配置)
意味と目的
「再配置」では、作業順序や設備の配置、導線を見直して業務効率を高めることを指します。
具体例
- 製造ラインのレイアウトを直線型からU字型に変更し作業者の移動距離を短縮する
- 小売店舗で商品の陳列を顧客導線に合わせて見直す
- 物流倉庫でピッキング工程を集約するために棚の配置を変更する
4. Simplify(簡素化)
意味と目的
「簡素化」では、業務プロセス自体をシンプルにし、無駄なステップや複雑さを削ぎ落とす取り組みを行います。
具体例
- 複雑な承認フローを見直して電子化しワンクリックで完結するようにする
- マニュアルを標準化し誰でも簡単に作業できるようにする
- ピッキング作業をバーコードや自動化システムで単純化する
ECRSの並び順
並び順には意味があります。E→C→R→Sは改善効果の大きい順に並んでおり、このステップで業務改善を行うことが効率的です。
ECRSのメリットと導入効果
ECRSにはさまざまなメリットがあります。
コスト削減
ムダな作業を排除し、効率的に業務を行うことで人件費や設備稼働費を削減できます。また、時間短縮による生産量増加や作業品質の向上がコスト削減に拍車をかけます。
作業者の負担軽減
業務プロセスが合理化されることで、余分な移動や無理な姿勢での作業が減り、作業者の身体的・精神的な負担が軽減します。それにより、労働災害のリスクも抑えられます。
品質向上とクレーム削減
工程を見直すことでミスや不良の発生を減らし、結果として顧客満足度の向上やクレーム削減に繋がります。品質が安定すると競争力向上にも寄与します。
組織全体の改善意識醸成
ECRSを継続的に導入することで、「ムダは必ずある」という改善意識が醸成され、組織全体での問題解決能力が向上します。部門間連携も強化され、次の改善につながる好循環が生まれます。
FAXは減った。売上は増えた。MOVO Vistaで実現する配車効率化
「配車担当…
2024.07.03
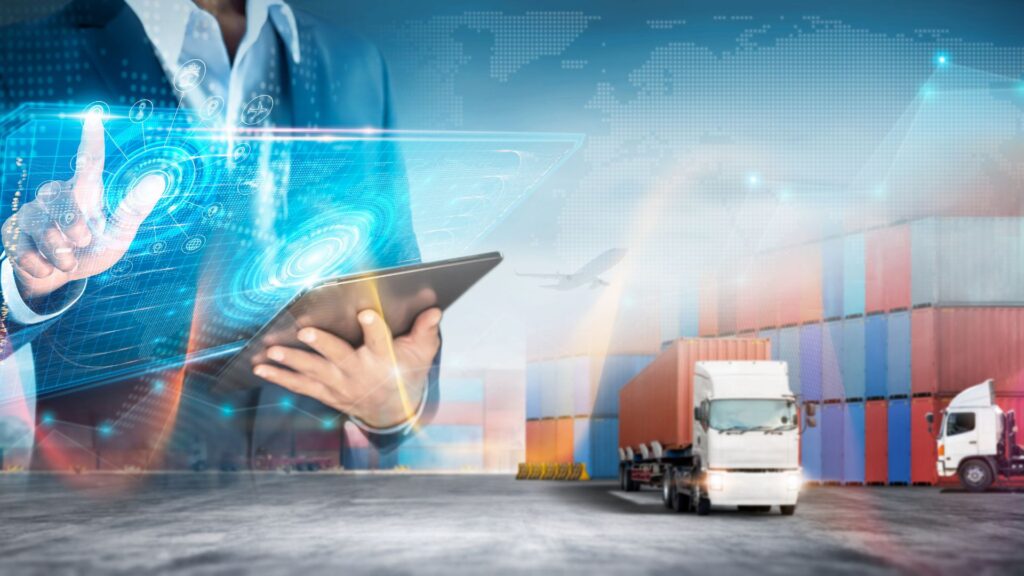
なぜECRSが物流に必要なのか
物流領域では、無駄な輸送や過剰な在庫、不要な作業の積み重ねがコスト増大の要因となり、企業の収益性を圧迫することがあります。言い換えれば、ECRSを行うことで競合よりも収益性の高い企業に変革することも可能と言えます。
たとえば、生産部門の都合で過剰に製品を生産するが保管場所がないため、外部倉庫を借り、そこへ横持ち輸送をします。外部倉庫で保管された製品は、顧客から注文されることなく長期間保管されていたり、配送した製品が返品されたり、廃棄に至ることもあります。これらのプロセスで発生される製品原価や人的コスト、保管コスト、廃棄コストなどは、すべからく無駄なコストと言えます。
物流の基本を解説!今の課題やこれから求められることへの対応策も提案
スーパーマ…
2024.05.07
現状維持バイアスとECRSの関係性
物流現場において、「今のやり方が最も安全だ」と考えてしまう現状維持バイアスは、業務効率化の大きな障壁となります。長年続けてきたプロセスに対する安心感から、無駄な工程や非効率な作業が温存されがちです。
しかし、環境変化が激しい現代では、現状維持こそが競争力を低下させる要因になり得ます。そこで、ECRSを活用することで、このバイアスを打破し、物流プロセスを抜本的に見直すことが可能です。
たとえば、「この作業は本当に必要か?」と問い直し排除(Eliminate)することで、無駄を削減し、よりシンプルで柔軟な物流体制を構築できます。ECRSは、現状維持にとらわれず、継続的な改善を促す強力なツールとなります。
現状維持バイアスとは?要因や脱却すべき理由、ステップなどを物流における例を交えて解説
「現状維持…
2025.01.14
ECRSを活用した業務改善のポイント
ECRSの考え方を取り入れる際のポイントを解説します。
現場へのヒアリングと可視化
ECRSを実践する上で、まず現場担当者の声を丁寧にヒアリングし、業務フローを「見える化」することが大切です。可視化することで、ムダや重複工程が明確になり、改善の着眼点がはっきりします。
小さな改善からスタート
ECRSのメリットは、小さな改善から取り組める点にあります。大規模な改革ではなく、まずは一部工程の排除や結合、配置転換などから始め、成果を積み上げていくことで社内の理解・協力を得やすくなります。
継続的なPDCAサイクルの実施
改善は一度実施して終わりではなく、常にPDCAサイクルを回し続けることが重要です。ECRSで洗い出した改善案を実行後も、改善効果を計測・検証し、新たな課題があれば再度ECRSを適用していきましょう。
システムやロボティクスとの組み合わせ
近年では、物流システムやロボティクスを活用した自動化が進んでいます。ECRSで不要な工程を削ぎ落としたうえで、システム導入や機器の自動化を検討すると、さらなる効率化を図ることが可能です。
マテハンとは?導入のメリットやデメリット、導入時の注意点、業務別の主なマテハン機器を解説
マテハンと…
2024.09.26
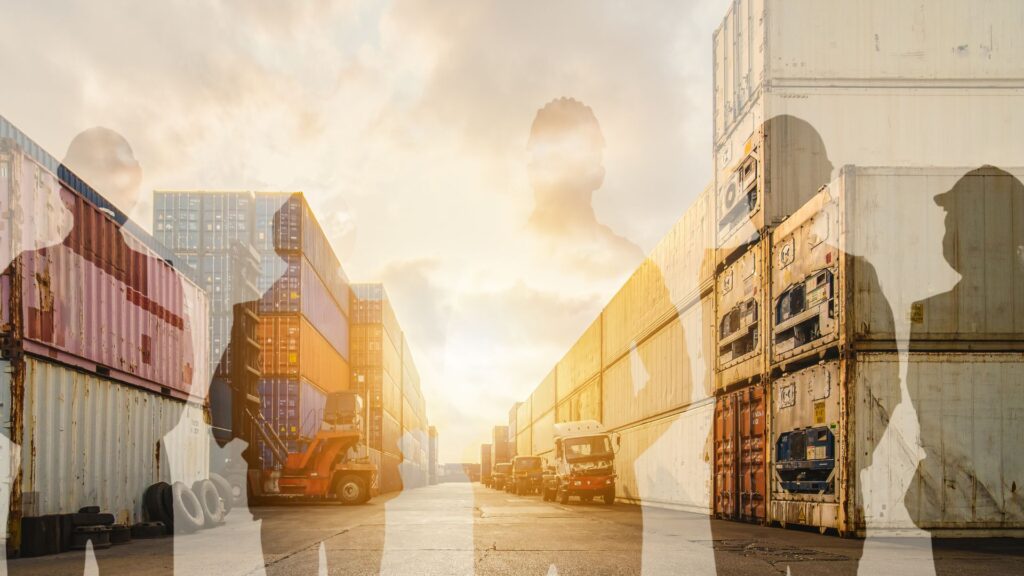
物流システム導入によるECRSの成功事例
物流システムを用いて、ECRSに成功した事例を紹介します。
Eliminate(排除):レオックフーズ
レオックフーズでは、着荷主から受ける配送に関する問い合わせについて、一度電話を切り、物流会社に問い合わせ、回答を得てから、また回答していました。それにより、1つの回答に10~15分程度要していました。
動態管理サービスのMOVO Fleet(ムーボ・フリート)の導入により、画面を見てすぐに配送状況を把握できるようになり、確認作業を「排除」することで、電話対応にかける時間が5分程度に半減しました。
詳細は以下の事例記事をご覧ください。
納品先でも配送状況が確認できる仕組みで、顧客満足度が向上 問合せ対応の時間も半減し、災害時も配送状況が即座に把握できるように
Combine(結合):京セラ 鹿児島川内工場
京セラ 鹿児島川内工場では、配送案件を自社と運送会社それぞれが管理表を作成しており、二重管理が課題になっていました。
配車受発注・管理サービスのMOVO Vista(ムーボ・ヴィスタ)を導入し、配送依頼のコミュニケーションをデジタル上で行うことで、配送案件の管理の「統合」に成功しました。
詳細は以下の事例記事をご覧ください。
京セラ鹿児島川内工場 物流部門にて、MOVO Vistaでトラックの輸送手配にかかる業務工数を60%削減!物流データの取得と活用で更なる効率化を目指す
Rearrange(再配置):森永乳業 神戸工場
森永乳業 神戸工場の資材受入では、朝に車両が集中することで庫内の受入が追いつかない状況が発生し、庫内作業者への心理的負担にもなっていました。
トラック予約受付サービスのMOVO Berth(ムーボ・バース)の導入により、トラックの到着時間や荷姿が事前にわかるようになりました。それにより、これまで到着後に行なっていた庫内作業を到着前に準備しておく「再配置」を行い、トラックのバース滞在時間が短縮されました。
詳細は以下の事例記事をご覧ください。
手作業による「荷待ち時間の把握・削減」の限界からMOVO Berthを導入し、ドライバー・庫内作業者の双方にとって快適な調達物流を実現
Simplify(簡素化):山藤運送 門真営業所
山藤運送 門真営業所では、トラックの荷待ちが発生していましたが、トラック待機所は6台分しかなく、満車時は一旦待機所外に移動していただく必要がありました。そして、トラックの呼出し業務に1台2分程度かかり、日々40台以上の対応をしていました。
MOVO Berthの導入により、庫内にいるリフトマンがオンライン上でトラックの呼出しができるようになり、月間で3営業日分の工数の「簡素化」に成功しました。
詳細は以下の事例記事をご覧ください。
荷主と連携し、物流DXを推進 荷待ち待機削減と庫内保管効率30%向上
ECRSを成功させる物流システムならMOVO
ECRSは物流現場で活用できる実践的な業務効率化のフレームワークです。「Eliminate」「Combine」「Rearrange」「Simplify」の4つのステップを意識するだけで、日々の業務に潜むムダを洗い出し、効率化につなげることができます。
前述しましたとおり、ECRSを活用した業務改善には物流システムの導入が有効です。Hacobuでは物流システムのMOVO(ムーボ)を提供しています。
トラック予約受付サービス(バース予約システム) MOVO Berth
MOVO Berth(ムーボ・バース)は、荷待ち・荷役時間の把握・削減、物流拠点の生産性向上を支援します。
動態管理サービス MOVO Fleet
MOVO Fleet(ムーボ・フリート)は、協力会社も含めて位置情報を一元管理し、取得データの活用で輸配送の課題解決を支援します。
配車受発注・管理サービス MOVO Vista
MOVO Vista(ムーボ・ヴィスタ)は、電話・FAXによるアナログな配車業務をデジタル化し、業務効率化と属人化解消を支援します。
関連記事
お役立ち資料/ホワイトペーパー
記事検索
-
物流関連2法
-
特定荷主