SCM(サプライチェーンマネジメント)とは?意味や仕組み、メリットを分かりやすく解説
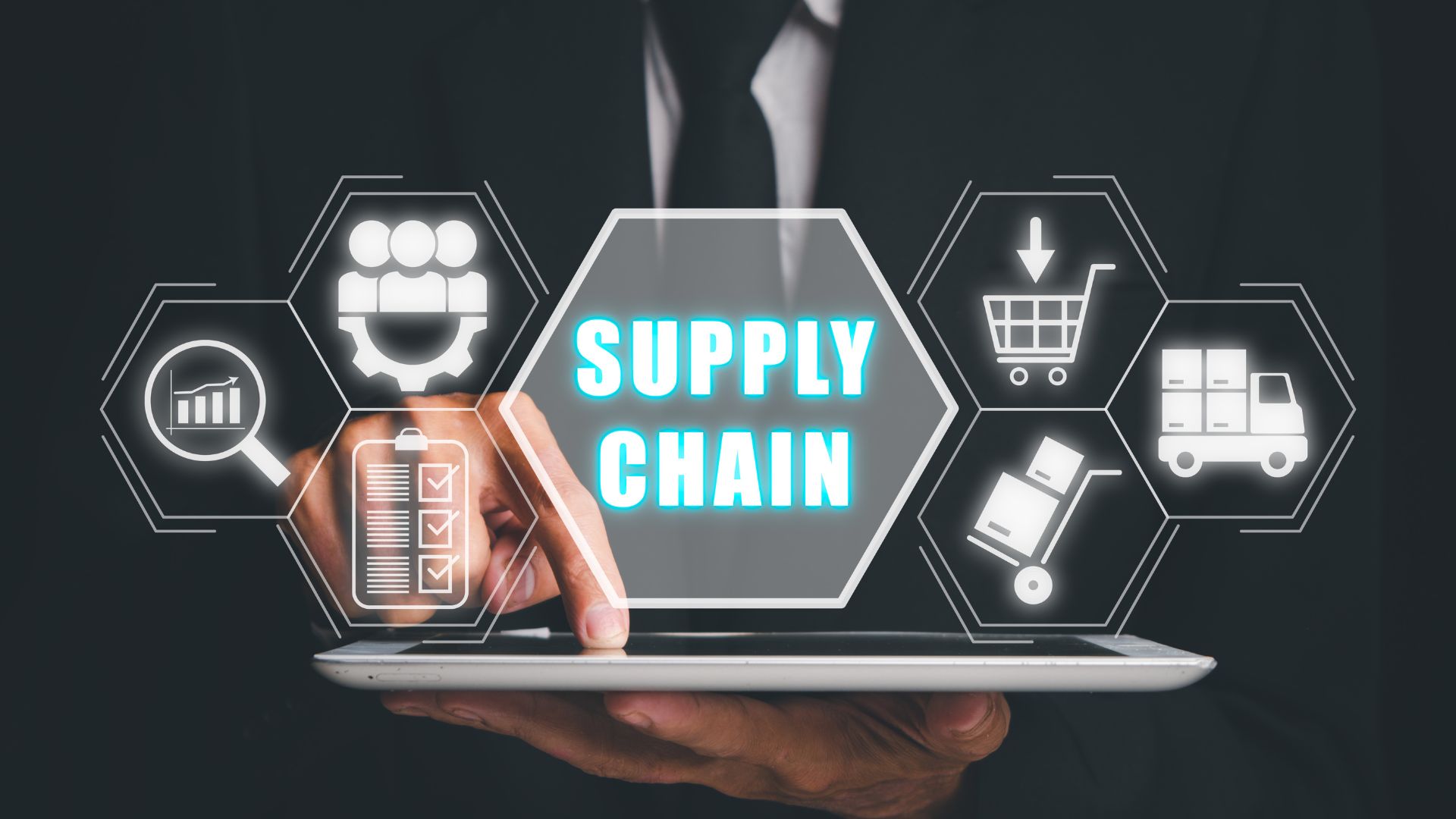
SCM(サプライチェーンマネジメント)とは、サプライチェーン全体のモノ・金・情報の流れを適切に管理する手法を指します。本記事では、SCMの概要や歴史、発展手法といった理論に加えて、実際にどのように実践していくのかの具体的なステップについても、物流DXパートナーのHacobuが解説します。
なお、Hacobuは物流DXコンサルティングサービス Hacobu Strategy(ハコブ・ストラテジー)を提供しています。物流業務の改善にお悩みがありましたら、以下をクリックしてご覧ください。
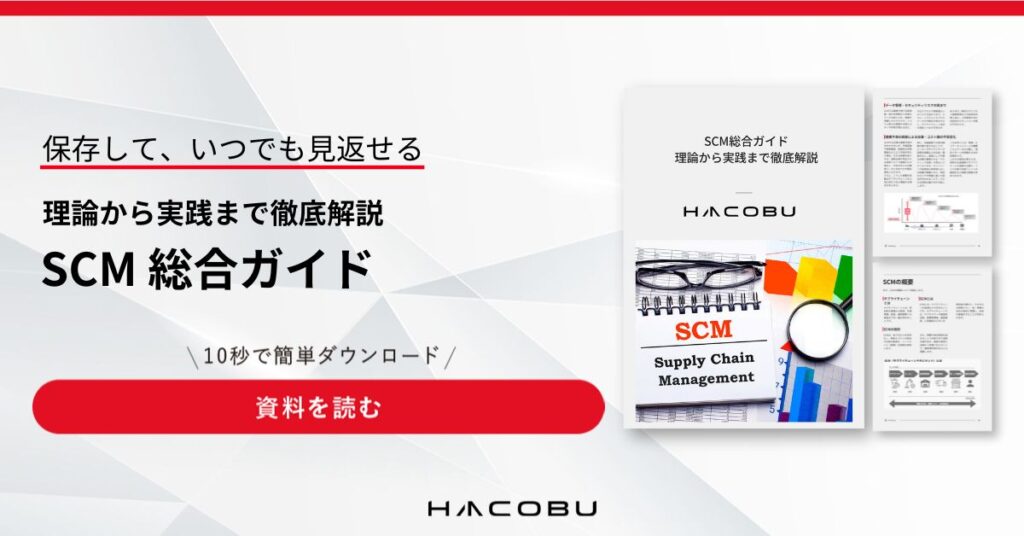
目次
SCM(サプライチェーンマネジメント)とは
SCMとは、サプライチェーンを最適化する手法のことです。サプライチェーンでは、サプライヤーや製造担当者、倉庫管理者、運送業者、小売業者など多くの関係者が関わり、それぞれの段階でモノ・金・情報の流れを適切に管理し、全体を最適化することが求められます。
サプライチェーンとは
サプライチェーンとは、原材料の調達から製造、在庫管理、配送、最終顧客への納品までの一連の流れのことです。
SCMの分類(SCPとSCE)
SCMは大きく分けるとSCP(Supply Chain Planning)とSCE(Supply Chain Execution)に分けられます。SCPはSCMの中でも「計画」を担当する領域であり、SCEはSCPによって作成された計画を現場レベルで実行するプロセスを指します。
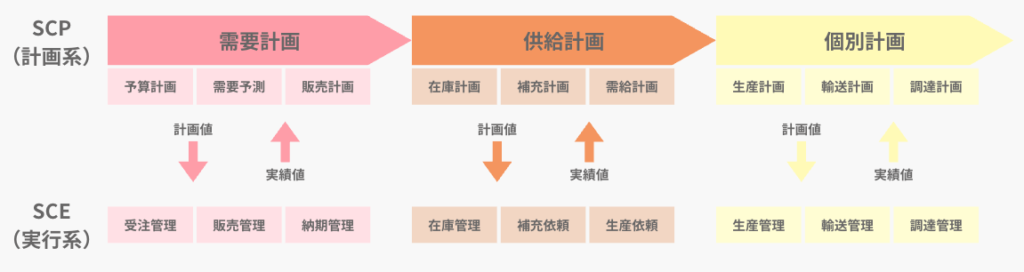
SCMとDCMの違い
SCMと似た言葉にDCM(デマンドチェーンマネジメント)があります。
SCMは、原材料の調達から製造・在庫管理・物流・販売に至るまで、供給の流れ全体を最適化する概念です。一方、DCMは、顧客の需要を起点としてサプライチェーン全体を設計・運用する考え方で、販売やマーケティングといった「需要創出」から逆算し、製造や供給の流れを調整します。
SCMとDCMのアプローチ例
たとえば、あるアパレル企業を例にすると、SCMの視点では、繊維原料の選定や工場での縫製、倉庫への在庫配分、店舗・ECへの配送までのプロセスを効率化し、コストを削減していくことが中心となります。一方、DCMの視点では「どんなデザインが必要なのか、どの地域でどのサイズがよく売れるのか」といった需要情報を重視し、生産数・在庫配分・販売タイミングを顧客ニーズに合わせて最適化することが主眼です。たとえば、SNSのトレンドやリアルタイムの売上データをもとに、次の生産計画や補充在庫をすばやく変更するといったアプローチがDCM的な手法と言えます。
SCMとDCMの統合
SCMは「供給側の効率性と最適化」に強いフォーカスがあり、DCMは「需要を起点にした柔軟な対応」に重点を置いている点が大きな違いですが、両者は対立概念ではありません。サプライチェーンの上流から下流までを、いかに需要を的確に取り込んで効率よく供給するかという視点で統合的に捉えることで、企業競争力を高めることができます。
SCMの目的
SCMは、各プロセスを効率化し、無駄なコストの削減や在庫の最適化、リードタイム(納期)の短縮を実現します。また、需要予測の精度を高めることで供給不足や過剰在庫を防ぎ、顧客の期待に迅速かつ的確に応えることで、顧客満足度の向上にも貢献します。
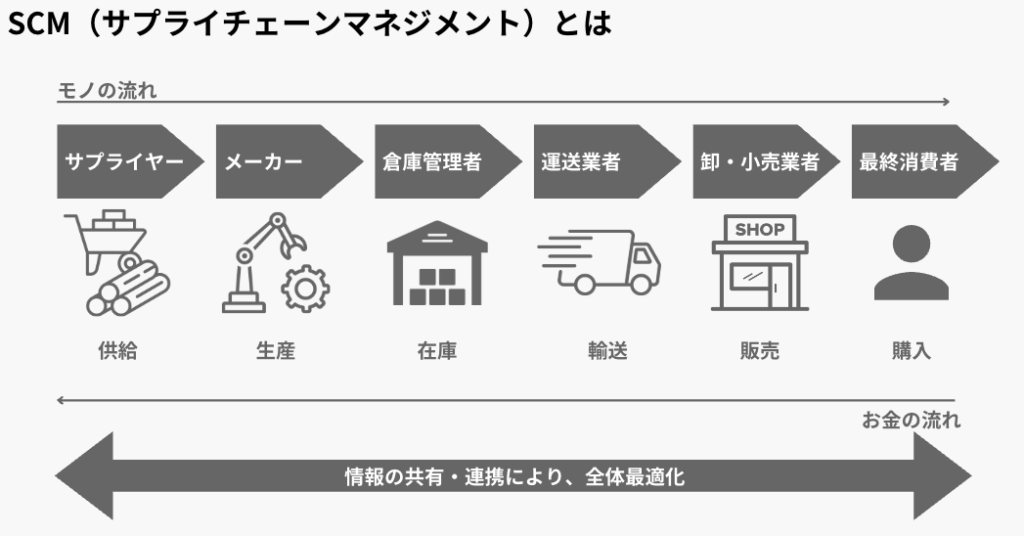
日本におけるSCMの歴史
本章では、日本においてSCMがどのように普及してきたか解説します。
戦後の復興期と大量生産・大量消費社会の幕開け
終戦直後の日本は、インフラや工場の復興が最優先課題でした。高度経済成長期に入ると、家電や自動車などの工業製品の大量生産・大量消費が進み、生産ラインの効率化と製品流通の円滑化が重視されるようになります。ただし、この時期はまだ企業内の管理が中心で、サプライチェーン全体を俯瞰する概念は一般的ではありませんでした。
オイルショックによるコスト管理意識の高まり
1970年代のオイルショックによって原材料価格や輸送コストが高騰し、日本企業は従来の大量生産体制から省エネルギーや効率化を図る方向へと転換を迫られました。それにより過剰在庫や無駄な輸送を抑える取り組みが進み、物流費や在庫費の見直しが加速しました。のちにSCMが普及する土台となる、コスト管理意識が一気に高まった時期でもあります。
バブル経済期の大量供給体制と物流効率化の発展
1980年代後半から始まったバブル経済期には、旺盛な需要に対応すべく企業は過剰ともいえる生産体制を整え、大量供給が一般化しました。一方で、物流費を削減しつつ需要変動に迅速に応えるための効率化技術や情報システムが導入され、倉庫や輸送拠点の最適配置が重視されました。大量・高速の流通を実現する仕組みづくりが急速に進んだ時期といえます。
バブル崩壊後の生産性向上とリードタイム短縮へのシフト
1990年代に入りバブルが崩壊すると、企業はリストラやコスト削減など生き残りをかけた改革を余儀なくされました。過剰な在庫や長いリードタイムが経営効率を圧迫する課題とされ、ジャスト・イン・タイム(JIT)などの生産スリム化技術が注目を集めます。こうして企業は、単なるコスト削減だけでなく、サプライチェーン全体の見直しによる迅速な顧客対応へとシフトしていきました。
グローバル化・IT化の進展とSCM概念の普及
1990年代後半以降、海外への生産拠点移転や国際貿易の増加などグローバル化が急速に進む中で、情報システムを活用した統合的な管理手法が注目を集めます。ERPなどが普及し、生産・在庫・物流などを横断的に最適化するSCMの概念が日本企業に浸透しました。多国籍に広がる拠点をつなぐことで、競争力強化を図る動きが広がりました。
自然災害や経済危機を機に高まるリスクマネジメント需要
阪神・淡路大震災や東日本大震災、リーマンショックなど大規模な災害や経済危機を経て、サプライチェーンの途絶や資材調達混乱の影響が企業活動を大きく左右することが明確化します。これらを機にBCP(事業継続計画)やリスク分散への取り組みが強化され、代替生産拠点や複数のサプライヤー確保など、SCMを軸としたレジリエンス構築が急務となりました。
デジタルトランスフォーメーション時代のSCMとAI・IoT活用
2010年代後半以降は、IoTセンサーやビッグデータ解析、AIアルゴリズムなどデジタル技術の急速な進歩がSCMを大きく変革しています。リアルタイムでの在庫・輸送状況の把握や需要予測の高度化、サプライチェーン全体を可視化するデジタルツインの導入など、新たなテクノロジーを活用した持続的な競争優位の確立に、各企業は取り組んでいます。
テクノロジーの進化が進む一方で、SCMに対して「現代のビジネス環境にフィットしなくなってきているのではないか」という声もあります。SCMの課題については、以下の記事で解説しています。
SCM(サプライチェーンマネジメント)のデメリットと問題点を解説。S&OPなど、さらなる対応策・発展手法とは?
SCM(サプラ…
2025.04.03
SCMが注目される背景
グローバル化とサプライチェーンの複雑化
近年、サプライチェーンマネジメント(SCM) への関心がかつてないほど高まっています。その背景には、グローバル化の進展とそれに伴うサプライチェーンの複雑化が挙げられます。国際的なサプライヤーからの調達が増えることで、為替変動リスクや地政学的リスクが顕在化し、安定的な部品供給に課題を抱えるケースが散見されます。さらに、消費者のニーズが多様化し、製品ライフサイクルが短期化する中で、多品種少量生産へのシフトが加速しています。この変化は、在庫の最適化を極めて困難にし、過剰在庫によるキャッシュフローの圧迫や、逆に機会損失を生む欠品リスクの増大というジレンマをロジスティクス部門にもたらしています。
不確実性の高まりとレジリエンスの必要性
パンデミックや自然災害といった予期せぬ事態がサプライチェーンに甚大な影響を与えるリスクは、常にSCMへの注目を加速させています。特に、数年前のコロナ禍においては、工場閉鎖や物流の停滞によって、多くの製造業が生産計画の狂いや納期遅延に直面しました。このような経験から、サプライチェーン全体の可視化とレジリエンス強化の重要性が改めて認識され、有事の際にも事業継続性を確保するための強固なSCM体制の構築が喫緊の課題となっています。
不確実性を高める要因は他にも存在します。その一つが地政学リスクとそれに伴う貿易政策の変動です。たとえば、米国で発動された「トランプ関税」は、特定の国からの輸入品に追加関税を課すことで、サプライチェーンの再編を余儀なくさせました。これにより、これまで安定していた調達先からの輸入コストが急増したり、代替調達先の確保に時間を要したりするなど、多くの企業がサプライチェーン戦略の見直しを迫られました。このような政治的判断がサプライチェーンに与える影響は大きく、今後も同様のリスクに備えるため、企業はサプライチェーンの多角化や地域分散といった対策を講じる必要に迫られています。
DXの進展とデータドリブンな意思決定
DXの進展に伴い、IoTやAIといった先端技術を活用したデータドリブンな意思決定の重要性が高まっていることも、SCMが注目される大きな要因です。これらの技術をSCMに適用することで、サプライチェーン全体をリアルタイムで把握し、より迅速かつ的確な意思決定を行うことで、競争優位性を確立しようとする動きが活発化しています。これらの複合的な要因が絡み合い、SCMは単なるコスト削減策に留まらず、企業の競争力を左右する戦略的な経営課題として認識されるに至っているのです。
Hacobu代表が語る。SCM全体最適化に必須な物流データプラットフォームとは
Amazon(アマ&…
2020.02.27
インダストリー4.0対応の重要性
インダストリー4.0では、IoTやAI、ビッグデータなどの先進技術を活用して、サプライチェーン全体のリアルタイムな可視化と最適化が求められます。従来のSCMは、拠点や部門間の情報分断により意思決定が遅れがちでしたが、インダストリー4.0では全体最適を実現するためにSCMの高度化が不可欠です。需給予測の精度向上やリードタイム短縮、在庫削減など、経営インパクトの大きい改善が可能になるため、SCMは単なる業務効率化を超えた戦略的機能として注目されています。
SCMの仕組みをSCORモデルに基づいて解説
サプライチェーンを最適にするためのフレームワークの一つとして、「SCORモデル」(Supply Chain Operations Reference-model)があります。SCORモデルに基づいて、SCMのマネジメント領域を解説します。
Plan(計画)
ネットワークデザイン
まず、工場や倉庫、物流拠点をどの地域に配置するかといった長期的なネットワークデザインが重要です。たとえば、主要消費地に近いエリアへ拠点を置くことで輸送コストやリードタイムの削減が見込めますが、拠点が分散することで管理工数や保管コストが増加します。
需要予測
需要と供給に関する情報を収集し、バランスを取るとともに、ギャップを特定し、それを埋めるための具体的な対策を計画します。季節や天候、過去の販売実績、広告キャンペーンなどを基にした需要予測は、日々の生産・在庫・配送計画に直結します。
たとえば、夏場に需要が高まる清涼飲料水などでは、正確な需要予測ができれば在庫不足や過剰在庫を防ぎやすくなり、利益率や顧客満足度の向上につながります。
部門連携
計画段階では、調達部門や製造部門、営業・マーケティング部門との連携が欠かせません。拠点配置の戦略性を高めたり、需要予測の精度を高めるためには、経営層の判断も含めた多角的な情報共有が重要です。こうした統合的なアプローチにより、サプライチェーン全体を俯瞰しながら柔軟かつ効率的な計画を立案できるようになります。
Planは前述のSCPに該当します。以降の領域がSCEに当たります。
Source(調達)
サプライヤー選定と契約管理
原材料や部品の品質や安定供給は製品価値を左右する重要ポイントです。たとえば食品メーカーなら、国産原料にこだわるのか、あるいは価格優先で複数国から仕入れるのかといった要件を整理し、適切なサプライヤーを選定します。契約時には、納期・価格・品質基準などを明確に定めてトラブルを防止します。
リスク分散と情報共有
天候不順や国際的な需給バランスの変動など、原材料価格や供給に影響を与える要因は多岐にわたります。そのため、複数のサプライヤーを確保するなどリスク分散が欠かせません。さらに需要予測や在庫状況をサプライヤーと共有することで、急なオーダー変更や増産の際にもスムーズに対応しやすくなります。
適正在庫とコスト最適化
需要予測に基づき必要量を的確に発注できれば、過剰在庫や欠品を防ぎつつ保管・廃棄コストを削減できます。たとえば食品の場合は賞味期限があるため、在庫回転率を意識した発注がとくに重要です。調達の段階で最適化が図れれば、その後の製造や配送にも好影響を及ぼし、サプライチェーン全体の安定性が高まります。
Make(製造)
生産計画とライン切り替え
調達した原材料を実際に製品へと変換します。需要予測に従って生産スケジュールを組むことで、過剰在庫や欠品のリスクを最小化できます。また、似た製品をまとめて生産するキャンペーン生産を実施すると、製造ラインの切り替えや清掃に要する時間が短縮され、稼働率の向上につながります。
品質管理
近年品質管理はますますその重要性を増してきています。たとえば、人命に関わるリスクを扱う医療機器や医薬品業界では、GMP(Good Manufacturing Practice)やGDP(Good Distribution Practice)といった省令に基づく厳格な管理を実施しています。また、一般製品の分野でも、製造業のPPM(Parts Per Million;100万個当たりの不良発生率)を応用し、例えば配送事故や汚損破損の発生率を条件の違うDCや車両で公平に比較し、ボトルネックを特定する手法を適用している企業もあります。
継続的な改善と人材育成
実際の製造現場では、設備トラブルや需要の急変動といった予期せぬ事態が発生することもあります。こうした状況に対応するため、品質管理部門やエンジニアとの情報共有を密に行いながら改善を積み重ねることが大切です。また、従業員の教育や作業マニュアルの標準化も、製造工程を安定させる大きな要素となります。
Deliver(配送)
在庫管理
適切な在庫管理により、供給の安定性が保たれ、需要変動にも柔軟に対応できます。また、商品を劣化や損傷から守り、品質を維持することで、クレームや返品のリスクを最小限に抑えられます。一方、在庫管理の精度が低いと、納品遅れや過剰在庫によるコスト増加などの問題が発生します。
配送
出荷指示から配達までのリードタイム短縮の改善を続け、必要な商品を迅速に届ける仕組みが求められます。これにより、需要が急増した際にも柔軟に対応でき、欠品を防ぐことが可能になります。
需要動向を先読みして在庫を適量に保つことが、効率的なDeliverを実現するポイントです。
Return(返品)
返品処理とトレーサビリティ
廃棄品や不良品の回収も行う必要があります。万が一、不具合のある製品が見つかった場合、どのロットの原材料を使用し、いつ製造・出荷されたかを即座に追跡することが重要です。
改善サイクルとしての返品情報
返品は単なる後処理だけではなく、製造工程の品質管理や販売戦略の見直しに役立つ貴重なフィードバックでもあります。たとえば、特定の商品が偏ったタイミングで大量に返品されるなら、需要予測や生産・出荷スケジュールに改善余地があるかもしれません。返品情報を活かして次のプランに反映し、継続的にサプライチェーンを強化することが重要です。
Enable(支援・連携)
ITインフラとデータ共有
サプライチェーン全体を円滑に回すための基盤作りも重要です。たとえば、ERP(Enterprise Resource Planning)やMES(Manufacturing Execution System:製造実行システム)、WMS(Warehouse Management System:倉庫管理システム)などの情報を一元的に連携することで、受注情報や生産状況、在庫状況をリアルタイムに可視化し、部門間やパートナー企業間のコミュニケーションを円滑にします。
経営層・社外パートナーとの協働
サプライチェーンの上流から下流までを最適化するには、経営トップの判断や投資意欲、取引先との連携が不可欠です。たとえば、新製品を共同開発したり、複数企業で共同輸配送を行うなど、社内外をまたぐ取り組みが成功すれば大きなコスト削減や新市場の開拓が可能になります。Enableはこうした連携を促進し、SCM全体を支える重要な基盤として機能します。
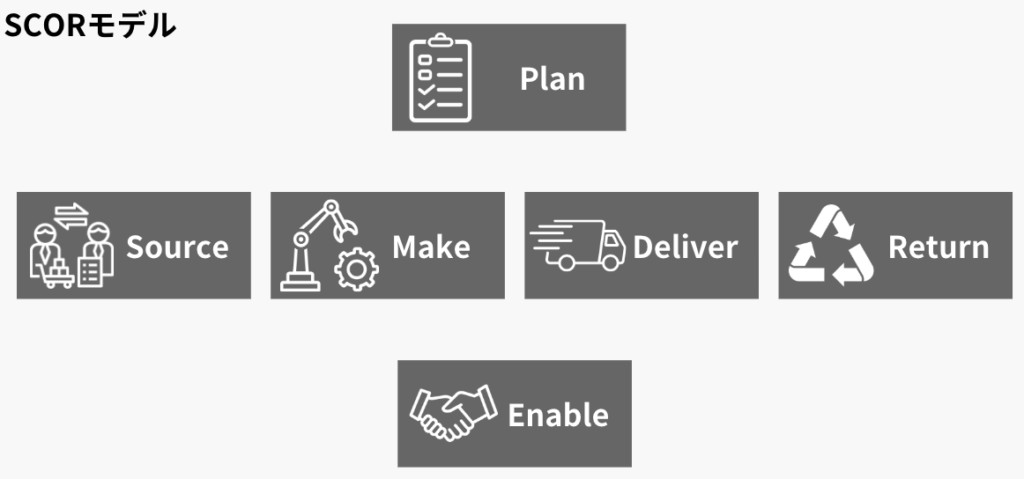
SCMのメリット
SCMを最適化することで、以下のメリットを得られます。
リードタイムの短縮
需要予測の精度向上や生産計画の最適化、物流ネットワークの強化など、SCMの各プロセスをシームレスにつなげることで、商品が顧客の手元に届くまでの時間を大幅に短縮できます。リードタイムを短縮できれば、商品の欠品や配送遅延といったリスクの削減につながります。
迅速な対応が実現することで競合優位性を高め、新製品やキャンペーンへの柔軟な取り組みも行いやすくなります。
プロモーション効果と売上拡大
商品の欠品や配送遅延の回避は、取引先への信頼獲得にも寄与します。信頼度が高い企業に対して取引先は、製品の露出を増やす、共同キャンペーンなどの販促活動が積極化されるなどの優遇措置が増えるなどの可能性が増します。こうした支援が増えることで、より多くの消費者にリーチでき、売上拡大につながります。
営業利益の改善
商品の欠品を回避するために過剰在庫を抱えては、製品の保管や廃棄にも過剰なコストがかかり、営業利益を圧迫してしまいます。一方で、SCMによる購買・製造・在庫管理・物流の統合管理で無駄な在庫を削減し、営業利益率を向上させることができます。
ROICの改善
過剰な在庫を削減できれば、棚卸資産(在庫そのもの)や固定資産(保管に関わる施設や設備)も効率化されます。結果として、投下資本も効率化でき、投資家や金融機関が重要視するROICの向上にもつながります。
リスク管理と継続性の強化
サプライチェーン全体の可視化によって、自然災害や原材料価格の高騰、サプライヤーの倒産などに加え、近年では地域紛争や政権交代等によるグローバルベースでの供給不足などの潜在的リスクを早期に把握し、迅速に対策を講じられます。
代替ルートや代替サプライヤーの検討が容易になるほか、サプライチェーンの分散化や在庫バッファの活用など、多面的なアプローチにより企業の持続可能性や回復力を高めることが可能です。これにより不測の事態にも柔軟に対応でき、企業の継続性を確保しやすくなります。
SCMが乗り越えるべきハードル
SCMには、乗り越えるべきハードルも存在します。
システム導入・運用コストの増大
SCMの導入には、在庫管理や生産計画、物流を統合管理するシステムの構築と保守が不可欠です。ソフトウェアやハードウェアへの投資、アップデートやカスタマイズにも費用がかかります。また、要員への教育やサポート体制の整備など、導入・維持には相応のリソースが必要となります。これらの初期投資や継続的な運用コストが増大すると、導入効果とのバランスに注意が必要です。
組織間の調整や運用プロセスの複雑化
SCMでは企業内で購買・生産・在庫・物流など多部門が連携する必要があり、評価基準やシステムの違いが統合管理を妨げる要因となります。調整不足による重複作業や責任の所在不明確化が起こりやすく、データの抜け漏れや意思決定の遅れにもつながります。全体最適化を図るには十分な時間と労力が必要です。
パートナー間連携の難易度・コミュニケーション負荷
SCMでは多数の取引先や物流事業者など企業外パートナーとの協力も必須です。情報共有の遅延や意見の衝突が起きやすく、システムや運用ルールの統合には高度な調整が求められます。こうした摩擦が生じると、納期遅延やコスト増、顧客満足度の低下などを招くリスクが高まります。
トレードオフを考慮した全体最適設計
SCMにおける施策はトレードオフが発生しやすいため、全体設計の視点が不可欠です。たとえば、欠品を防ぐために一度に大量の在庫を確保すると、運行のバラつきによる運賃高騰やドライバー不足、さらには保管料の増加といった別の課題が発生します。このような課題を回避するためには、各施策のメリット・デメリットをしっかりと把握し、全体最適の観点から判断を下す必要があります。また、部門間の利害対立が生じることもあるため、調整機能を果たす役割が重要になります。組織内外のパートナーと円滑に連携し、SCMのパフォーマンスを最大化するには、統合的な計画立案と情報共有の仕組みを強化することが求められます。
データ管理・セキュリティリスクの高まり
SCMでは需要予測や生産実績、取引先情報など多様なデータを扱うため、管理が煩雑になりがちです。システム同士の連携や外部とのデータ共有が増えるほど、不正アクセスや情報漏えいのリスクも高まります。さらに、システムトラブルやデータの不整合が発生すると、サプライチェーン全体の混乱につながる恐れがあります。暗号化やアクセス権限管理などの技術的対策に加え、人材教育を含む包括的なセキュリティ対策が不可欠です。
需要予測の誤差による在庫・コスト面の不安定化
SCMでは正確な需要予測が欠かせませんが、市場変動や季節要因、突発的な外部要因などにより予測が外れた場合、大きな影響を受けます。過剰在庫が発生すれば保管コストや廃棄ロスが増大し、不足が生じれば顧客ニーズに対応できず機会損失となります。
さらに、こうした需要の変動はサプライチェーンの上流に向かうほど増幅する傾向があります。特に、流通段階での発注調整が繰り返されることで、メーカーやサプライヤーが実際の需要以上の生産・調達を行い、結果として不要な在庫が蓄積される「ブルウィップ効果」が発生しやすくなります。キャンペーンや新商品の発売時にはこの影響が顕著になり、特定のエリアや時期に偏った発注が行われることで、さらなる供給の偏りを引き起こします。これを防ぐには、時期・エリア・キャンペーンの種類ごとにデータを分類し、発生パターンを把握するのが効果的です。
これらの損失を補うには、柔軟な生産調整やサプライヤーとの連携が必要で、リスク分散や在庫バッファの最適化など慎重な戦略が求められます。
SCMの最適化ならHacobu Strategy
本記事では、SCMの理論やメリット、乗り越えるべきハードルについて解説しました。サプライチェーンにおける、各プロセスを効率化し、無駄なコストの削減や在庫の最適化、リードタイムの短縮を実現しましょう。
重要なのは、「課題の本質」を正確に把握するために必要なデータを取得することです。どのようなデータを取得すべきかお悩みでしたら、ぜひHacobu Strategyへお問い合わせください。
Hacobu Strategyが考える、SCM最適化に向けた実践的な4つのステップは以下の記事で解説しています。
【実践的】SCM(サプライチェーンマネジメント)の導入ステップを解説。具体的な導入事例も紹介
SCM(サプラ…
2025.04.03
関連記事
お役立ち資料/ホワイトペーパー
記事検索
-
物流関連2法
-
特定荷主