BOP(Bill of Process)とは?BOMとの違いやメリット、導入ステップについて解説
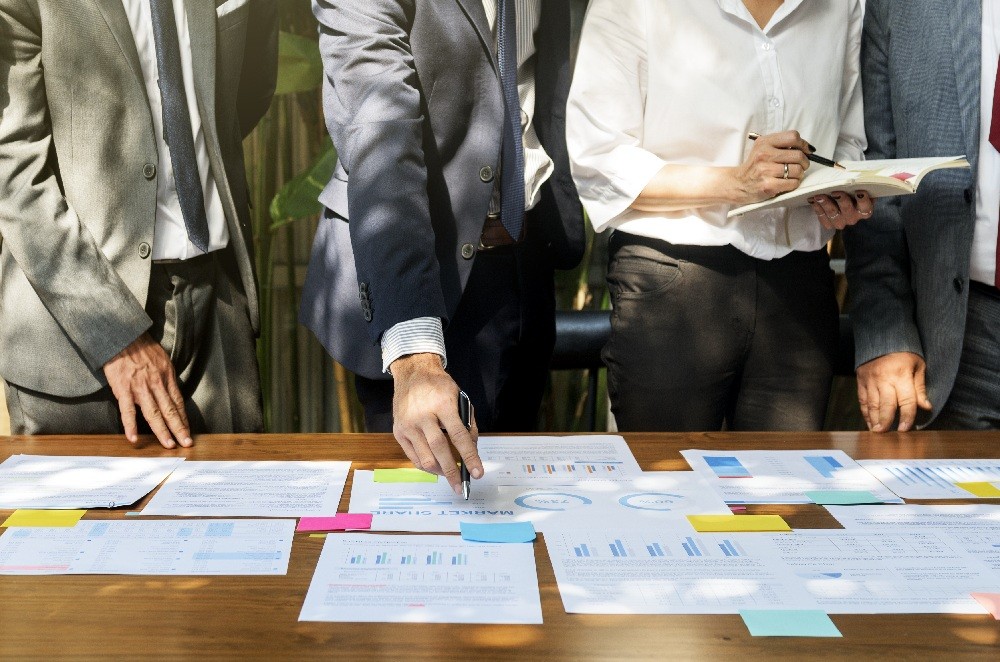
製造業におけるDXが進む中で、BOP(Bill of Process)という言葉を耳にする機会が増えてきました。従来は紙ベースや属人的な管理にとどまっていた製造プロセスを、標準化・デジタル化し、設計から製造現場までの情報を一気通貫でつなぐ仕組みとして、BOPの活用が急速に広がりつつあります。BOM(部品構成表)やルーティング情報と混同されがちですが、BOPは「製造プロセスの可視化と最適化」に欠かせない情報基盤として、注目されています。
本記事では、BOPの基本的な役割からBOMとの違い、設計から製造への情報連携におけるBOPの重要性について、物流DXパートナーのHacobuが解説します。
BOPとは
BOM(部品表)との違いと役割
BOP(Bill of Process)は、製品を「どう作るか」を体系的に整理・管理する情報であり、製造現場における「設計図」のような役割を果たします。具体的には、各工程でどの作業をどの順番で行うのか、どの設備を使い、どんな作業者スキルや治具が必要か、どのくらいの作業時間がかかるのか、といった詳細な情報が含まれます。
これに対して、BOM(Bill of Materials)は「何を使って作るか」、つまり製品を構成する部品や材料、構成階層を定義したものです。製造業では古くからBOMを活用しており、部品調達や在庫管理の基礎データとして使われてきました。
つまり、以下のように役割が明確に分かれています。
- BOM:製品を作るための「材料リスト」
- BOP:製品を作るための「作業手順書」
従来は、これらの情報が別々に管理されていたり、紙ベースで運用されていたりしたため、設計変更や製造ラインの見直し時に手間がかかっていました。BOPをデジタルで管理することで、こうした非効率を解消し、製造現場の柔軟性やトレーサビリティの向上が期待できます。
設計から製造への“プロセス情報”の橋渡し
製品開発において、「設計」と「製造」は本来シームレスにつながっているべきですが、現場では情報の断絶が課題になることが少なくありません。特に、設計側が作成した図面や仕様書が、製造現場での工程設計に活かされないケースもあります。
そこで重要になるのがBOPです。BOPは、設計から製造に至るまでの「プロセス情報」を一貫して管理・共有できる仕組みを提供します。たとえば、設計変更により製品の一部部品が変更された場合でも、BOPがあればその影響を製造プロセスまで即座に反映できます。
また、BOPをPLM(Product Lifecycle Management)やMES(Manufacturing Execution System)と連携させることで、設計—生産—現場の情報連携が強化され、モノづくりの全体最適化が進みます。
BOPの目的とメリット
BOP(Bill of Process)は単なる製造手順の記録ではありません。企業全体のモノづくりを最適化するための“共通言語”として、さまざまな目的とメリットを持っています。
グローバルな製造拠点間での標準化・効率化
製造業では、国内外に複数の工場を展開しているケースが一般的です。しかし、拠点ごとに製造工程が異なると、品質のばらつきや生産効率の差が生まれやすくなります。
BOPを導入し、各拠点で共通の製造プロセスを管理することで、製造の標準化とベストプラクティスの共有が可能になります。結果として、再現性の高い生産体制を構築でき、工場間でのスムーズな切り替えや負荷分散も実現しやすくなります。
プロセスの可視化による品質・納期の安定
BOPは製造プロセスを詳細に定義するため、各工程で「誰が・何を・どのように」行うのかを明確にできます。これにより、作業の属人化を防ぎ、教育や引き継ぎの効率化が図れます。
また、製造工程ごとの時間やリードタイムも可視化できるため、ボトルネックの発見や工程改善にも役立ちます。結果として、製品の品質安定と納期遵守の精度が高まり、顧客満足度の向上につながります。
設計と製造現場の連携強化
設計と製造の間には「言語の壁」が存在することが多く、図面や仕様書だけでは製造現場が意図を正しく理解できない場合もあります。
BOPを活用することで、設計段階で意図した製造プロセスをそのまま現場に伝えることができ、情報伝達の齟齬を防ぐことができます。さらに、PLMやERP(Enterprise Resource Planning)との連携により、設計変更の影響もリアルタイムでプロセスに反映できるため、部門間の連携がスムーズになります。
BOMとBOPとMBOMの違いと関係性
BOM(Bill of Materials)、BOP(Bill of Process)、MBOM(Manufacturing BOM)は、いずれも製品を生み出すために必要な情報ですが、それぞれの役割は異なります。
まず、BOM(部品表)は「製品の構成情報」を管理するためのものです。どの部品や材料を使って製品を構成するのかを明確にする役割を持っています。
一方、BOP(工程表)は「製造手順」を管理するもので、製品をどのような順序で、どの設備を使い、どのような作業を行って作るのかといった情報を含んでいます。
そして、MBOM(製造用部品表)は、BOMの情報を製造現場向けに最適化したもので、「工程ごとに必要な部品や数量」といった、実際の製造に即した構成情報を管理します。BOPとのひも付けも行われており、現場での生産活動をスムーズに進めるための重要な情報源となります。
このように、BOMは「何を作るか」、BOPは「どう作るか」、MBOMは「どの工程で何を使うか」と、それぞれのフェーズで必要となる情報を担っており、これらを連携させることで、設計から製造までのプロセスを一貫して最適化することが可能になります。
BOMは「何を作るか」、BOPは「どう作るか」を定義し、それらを結びつけて現場で実行可能な形に整えるのがMBOMの役割です。MBOMは、BOMの情報を製造プロセスに適した形で再構築したもので、BOPと密接に連携しています。
製品ライフサイクル全体を通して、これら3つの情報が統合・連携されていることで、設計〜製造〜納品までの流れを一気通貫で最適化できるようになります。
BOP導入時の課題と注意点
BOP(Bill of Process)は、設計から製造までのプロセスを一貫して最適化する強力な仕組みですが、導入すればすぐに効果が出るというわけではありません。むしろ、導入段階でつまずく企業も少なくなく、いくつかの課題と注意点を踏まえた上での運用が重要です。
現場との情報ギャップが生じやすい
BOPは上流(設計部門や本社企画)で整備されることが多いため、現場との認識にズレが生じやすい点が注意ポイントです。
たとえば、実際の作業手順や使われている設備の実情と、BOPに記載された情報が一致していないケースもあります。このようなギャップがあると、せっかく構築したBOPが「現場で使われない情報」になってしまい、形骸化するリスクもあります。
BOPを導入・運用していくうえでは、現場の担当者を巻き込みながら、プロセスの棚卸しや定期的なフィードバックを行うことが不可欠です。
個別最適にならないよう注意する必要がある
BOPは各製品・工程ごとに詳細な設計が必要なため、導入初期は「特定ラインや製品に特化した最適化」になりがちです。しかし、これが行きすぎると、他の拠点や製品には使い回せない「属人化されたプロセス定義」になってしまい、スケーラビリティを損なう恐れがあります。
重要なのは、個別最適ではなく「全体最適」の視点で設計・運用を行うことです。共通化できる工程や標準ルールを意識しながら、BOPを「横展開可能な資産」として整備していくことが、長期的な運用のカギとなります。
ツール導入だけで終わらせない体制づくりが必要
BOPの整備には、PLMやMESなどのITツールの活用が不可欠です。しかし、ツールを導入しただけで「DXが進んだ」と考えてしまうのは要注意。実際には、運用する人材のスキルや現場での運用フローが整っていないと、ツールは機能しません。
ツールを活かすためには、BOPの整備・活用に関わるチームや担当者の教育、プロセス改善を継続できる仕組みの構築など、「運用面の体制づくり」が必要不可欠です。
BOPの導入は、単なるIT化ではなく、業務そのものを見直し、全社的なものづくり体制を再設計する取り組みとも言えます。短期的な効果にとらわれず、中長期での運用設計を意識することが成功のポイントです。
導入を成功させるためのステップ
BOPの導入は、単に情報をデジタル化するだけではなく、業務のあり方そのものを見直すプロジェクトです。スムーズかつ効果的に導入を進めるためには、いくつかのステップを押さえておくことが重要です。
BOP導入の目的・ゴールを明確にする構想策定から始める
まず初めに行うべきなのは、「なぜBOPを導入するのか」「導入によって何を実現したいのか」を明確にすることです。
たとえば「多拠点での製造標準化を実現したい」「設計変更を現場へリアルタイムに反映したい」「工程ごとの生産性を可視化したい」など、目的を具体的に定めることで、BOPの設計方針やスコープ、優先順位を判断しやすくなります。
構想策定の段階では、経営層や設計部門、製造現場など関係者を巻き込んだディスカッションを重ね、共通のゴールを設定することが重要です。
プロセスを明文化し、マスターの整備をおこなう
BOPの土台となるのは、製造プロセスに関する正確で網羅的な情報です。そのためには、まず現場の作業内容や工程の流れを「見える化」し、標準化されたルールとして明文化することが欠かせません。
並行して、「工程」「作業内容」「設備」「スキル」などに関するマスターデータの整備も進めておく必要があります。これにより、属人的な作業が減り、BOPの構築やメンテナンスを効率的に進めることができます。
このステップは、BOPの品質を左右する重要な工程であり、現場との連携や実態に即した情報収集がカギになります。
PLMやMESとの連携設計をおこなう
BOPの真価は、他のシステムと連携してこそ発揮されます。特に、設計情報を管理するPLMや、現場の実行管理を担うMESとのスムーズな連携は不可欠です。
PLMとBOPを連携することで、設計変更が即座に製造工程へ反映されるようになり、開発と生産のギャップを縮めることができます。さらに、MESと連携すれば、BOPで定義した工程通りに製造が実行され、実績データのフィードバックによる継続的な改善も可能になります。
BOPを中心に各システムをつなぐことで、製造プロセス全体の見える化・一元管理が実現し、企業全体の競争力向上につながります。
製造現場だけでなく物流もシステム化を
BOPは、製品を「どう作るか」を定義し、設計から製造現場までの情報を橋渡しする重要な仕組みです。BOMやMBOMと連携させることで、部品情報と製造工程を一元的に管理し、全社的なモノづくりの最適化を実現することができます。
特に、グローバルで製造拠点を展開している企業にとっては、プロセスの標準化や工程の可視化が大きなメリットとなり、品質安定・納期遵守・生産性向上に寄与します。
一方で、BOPの導入には「現場との情報ギャップ」や「個別最適のリスク」「ツール導入で満足してしまう体制の弱さ」といった課題も伴います。だからこそ、導入前の構想策定、プロセスの明文化、PLM・MESとの連携設計などを丁寧に進めることが、成功のカギを握ります。
BOPは単なるITツールではなく、全社のモノづくりの質を底上げする「戦略的インフラ」です。製造業DXの取り組みの一環として、BOPの整備・活用を進めてみてはいかがでしょうか。
なお、企業としての競争力を高めるには、製造現場だけでなく、物流プロセスの最適化も重要です。
Hacobuでは「運ぶを最適化する」をミッションとして掲げ、物流DXツールMOVO(ムーボ)と、物流DXコンサルティングサービスHacobu Strategy(ハコブ・ストラテジー)を提供しています。物流現場の課題を解決する物流DXツール「MOVO」の各サービス資料では、導入効果や費用について詳しくご紹介しています。
トラック予約受付サービス(バース予約システム) MOVO Berth
MOVO Berth(ムーボ・バース)は、荷待ち・荷役時間の把握・削減、物流拠点の生産性向上を支援します。
動態管理サービス MOVO Fleet
MOVO Fleet(ムーボ・フリート)は、協力会社も含めて位置情報を一元管理し、取得データの活用で輸配送の課題解決を支援します。
配車受発注・管理サービス MOVO Vista
MOVO Vista(ムーボ・ヴィスタ)は、電話・FAXによるアナログな配車業務をデジタル化し、業務効率化と属人化解消を支援します。
物流DXコンサルティング Hacobu Strategy
Hacobu Strategyは、物流DXの戦略、導入、実行まで一気通貫で支援します。
関連記事
お役立ち資料/ホワイトペーパー
記事検索
-
物流関連2法
-
特定荷主