PLM(Product Lifecycle Management)とは?製品ライフサイクル管理の基本と導入メリットを解説

製品開発の現場では、年々そのスピードと複雑さが増し、部門間の連携や情報管理の重要性が高まっています。こうした背景の中で注目されているのが、PLM(Product Lifecycle Management)という考え方です。製品の企画から設計、製造、保守、廃棄に至るまでの一連のプロセスを一元管理することで、業務全体の最適化と競争力の強化を図る仕組みです。
本記事では、PLMの基本概念やPDMとの違い、導入による具体的なメリットから、成功させるためのステップ、ERPやMESとの連携設計などについて、物流DXパートナーのHacobuが解説します。開発体制を見直したい企業や、製品ライフサイクルの全体最適に取り組みたい方にとって、実践的なヒントとなる内容です。
目次
PLM(Product Lifecycle Management)とは
PLMの定義と基本概念
PLM(Product Lifecycle Management)とは、「製品ライフサイクル管理」と訳され、製品の企画・設計・製造・販売・廃棄に至るまでの一連のプロセスを、部門横断的に管理・最適化する手法です。
単に開発段階の効率化にとどまらず、製品が市場に出てからの改良、保守、そして市場から撤退する段階までを一貫して見える化・データ化し、業務の効率化と付加価値向上を図ります。
現代のモノづくりでは、製品の多機能化・短納期化・グローバル展開などによって、開発・製造現場はますます複雑になっています。PLMはそうした複雑さを統合的に管理し、関係者間での情報共有を円滑にすることで、品質の向上やコスト削減、リードタイム短縮を実現します。
PDM(Product Data Management)との違い
PLMと混同されがちな用語に「PDM(Product Data Management:製品データ管理)」があります。
PDMは、設計図面や部品表(BOM)、仕様書などの技術データを中心に管理するシステムで、主に設計・開発フェーズに特化しています。
一方で、PLMはPDMを内包する広義の概念であり、製品に関わるすべての工程・データを対象とします。PDMが「設計情報の整理整頓」だとすると、PLMは「製品に関わるすべての情報のマネジメント」と言えるでしょう。
つまり、PDMはPLMの一機能であり、PLMを導入することでPDMの機能も包括的にカバーされるという位置づけです。
PLMが必要とされる理由
PLMが必要とされる背景には、製造業を取り巻く環境変化と、それに伴う課題の高度化があります。主な理由は以下の通りです。
製品開発のスピードアップ
市場ニーズに迅速に応えるためには、製品開発のリードタイム短縮が不可欠です。PLMは開発プロセス全体の流れを可視化・標準化することで、無駄な手戻りを減らし、スピード感ある開発を支援します。
グローバル対応
海外の拠点や外部パートナーと連携して製品開発を進めるケースが増える中、関係者全員が同じ情報をリアルタイムで共有するためには、PLMのような共通基盤が必要不可欠です。
コンプライアンスとトレーサビリティの確保
製品に関する規制対応や、部品の変更履歴、使用材料の管理などが求められる中で、PLMは記録の一元管理や追跡性の確保にも役立ちます。
製品の複雑化と多品種対応
IoT機器やスマート家電など、ソフトウェアとハードウェアが融合した製品が増えており、関係部門の連携が不可欠になっています。PLMはその橋渡しを担い、全体最適を実現します。
これらの背景から、製品を「設計する」「作る」だけでなく、「育てていく」ための戦略的な仕組みとして、PLMはますます注目されています。
PLMが担う役割と範囲
製品企画から設計・生産・保守・廃棄までを一元管理
PLMは、製品のライフサイクル全体の情報を一元管理する仕組みです。製品企画の初期段階からはじまり、設計・開発、製造、出荷、保守、そして最終的な廃棄やリサイクルに至るまで、すべてのフェーズを一貫して管理します。従来は部門ごとに個別で管理されていた製品情報や図面、部品構成などを、PLMによって統合的に扱うことで、重複作業や情報の齟齬を防ぎ、開発からリリースまでのリードタイムを短縮することが可能になります。また、過去製品のデータを参照して新製品に活かすといった、ナレッジの再利用にもつながります。
部門横断での情報共有と業務プロセス最適化
製品開発には、企画、設計、生産、調達、品質保証、サービスなど、さまざまな部門が関わります。PLMは、これらの部門間で製品情報をリアルタイムに共有できる環境を提供することで、部門間の連携を強化し、業務プロセス全体の最適化を実現します。たとえば、設計段階で変更があった際に、その情報が即座に生産部門や調達部門に共有されることで、手戻りや調整コストを大幅に削減できます。こうした情報の一元化とプロセスの連携により、企業全体としての意思決定のスピードが高まり、変化の激しい市場環境にも柔軟に対応できる体制を整えることができます。
設計変更やバージョン管理の効率化
製品開発では、設計変更が頻繁に発生するのが常です。PLMは、こうした変更履歴を正確に管理し、関係部門に迅速に通知する仕組みを備えています。誰が、いつ、どのような理由で変更を行ったのかという履歴情報を追跡できるため、トレーサビリティの確保や品質向上にもつながります。また、製品の仕様や設計が複数のバージョンに分かれる場合でも、それぞれのバージョンを明確に管理することができ、意図しない古いデータの使用を防ぐことができます。結果として、設計の正確性と作業の効率性を両立し、開発全体の生産性を高めることが可能になります。
PLMを導入するメリット
開発期間の短縮とコスト削減
PLMを導入する最大のメリットのひとつが、製品開発にかかる期間の短縮と、トータルコストの削減です。製品情報を一元的に管理することで、各部門間でのやり取りがスムーズになり、設計から生産までの工程にかかる無駄な時間を大幅に削減できます。また、過去の製品データや類似設計の再利用が容易になるため、ゼロからの設計作業が減り、人的リソースや材料のコストを効率的に抑えることが可能になります。このようにPLMは、開発スピードとコストの両面において、企業競争力を高める大きな支えとなります。
設計ミスや情報漏れの防止
複数の部門が関与する製品開発においては、設計ミスや情報の伝達ミスによるトラブルがつきものです。PLMは、すべての製品情報を一つのプラットフォーム上で管理し、最新情報を関係者全員が常に確認できる状態に保つことで、情報の抜け漏れや認識のズレを防止します。さらに、変更内容の承認フローやアラート機能により、人的ミスを事前に察知し、問題の早期発見にもつながります。これにより、後工程での修正や不具合対応にかかるコストを削減し、開発の信頼性を高めることができます。
トレーサビリティの強化と品質向上
製品の品質を担保するうえで重要なのが、設計から製造、出荷、アフターサービスに至るまでの履歴を正確に追跡できること、いわゆる「トレーサビリティ」の確保です。PLMでは、各工程のデータや変更履歴が詳細に記録されており、万が一トラブルが発生した場合でも迅速な原因究明と対応が可能です。これにより、製品の品質管理がより厳密に行えるようになり、顧客満足度の向上や、法規制への対応力の強化にも貢献します。高品質な製品を安定して供給するための基盤として、PLMはますます重要性を増しています。
PLMを導入する時の課題と注意点
業務プロセスとの整合性をとる
PLMを導入する際には、既存の業務プロセスとの整合性をとることが不可欠です。理想的なPLMの仕組みを構築したとしても、実際の現場業務と噛み合っていなければ、逆に混乱や作業の遅延を招くリスクがあります。導入時には、業務フロー全体を俯瞰しながら、どのプロセスにどのような影響を与えるのかを丁寧に検証し、必要に応じてプロセスの見直しや調整を行う必要があります。システムありきではなく、業務との親和性を意識した導入が成功のカギを握ります。
現場のニーズや運用方法をヒアリングする
システムの導入がうまくいかない原因のひとつに、現場の声が十分に反映されていないという点があります。PLMも例外ではなく、実際に使用する現場の担当者の業務スタイルや課題を丁寧にヒアリングし、それをシステム設計に反映させることが重要です。運用上の細かいニーズや使い勝手を無視したままでは、導入後に「使いづらい」「結局エクセルに戻ってしまった」といった事態にもなりかねません。導入前から現場との対話を重ね、納得感のある形で展開することが、定着の第一歩となります。
ITシステムの統合や既存ツールとの連携を検討する
PLMの導入にあたっては、既存の基幹システム(ERPなど)や設計ツール(CAD、BOM管理など)との連携も視野に入れる必要があります。異なるシステム同士の連携が不十分だと、かえって二重入力や情報の不整合が発生し、業務の非効率を招くことになります。したがって、導入段階でITインフラ全体を見直し、データ連携やAPI活用の設計を事前に検討することが求められます。また、セキュリティやアクセス権限の設計も忘れてはならないポイントです。全社的な視点でシステム連携を進めることで、PLMの価値を最大限に引き出すことが可能になります。
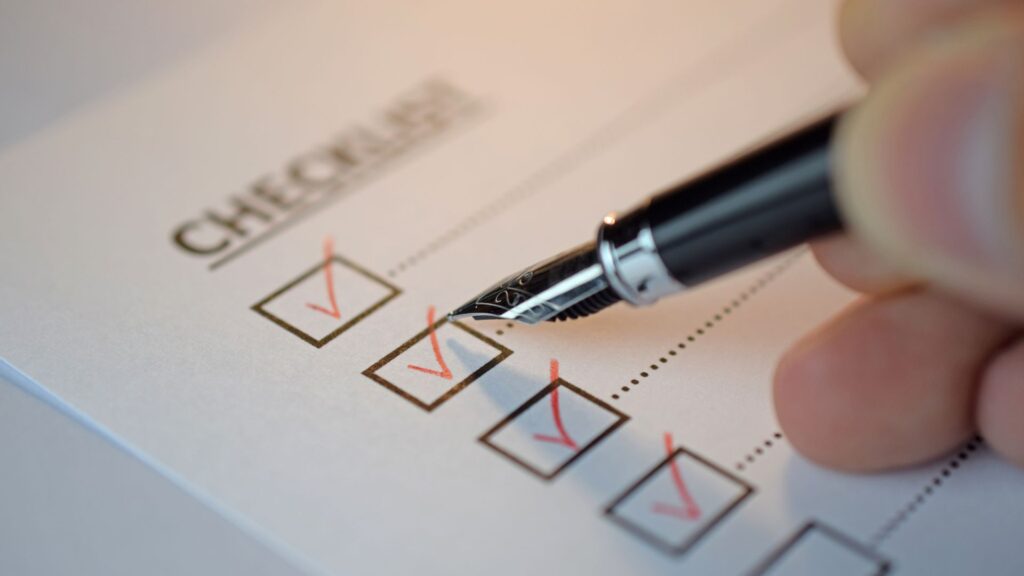
PLM導入を成功させるステップ
PLM導入の目的と範囲を明確にする
PLMの導入にあたって最初に取り組むべきは、「なぜ導入するのか」「どこまでをPLMでカバーするのか」といった目的と範囲の明確化です。目的が曖昧なままでは、導入後に効果測定ができず、関係者の協力も得づらくなります。たとえば、「設計の手戻りを減らす」「開発期間を短縮する」「情報共有を促進する」など、現場の課題をベースに目的を具体的に設定することで、PLM導入の意義が社内に浸透しやすくなります。導入範囲もまた、全製品を対象とするのか、一部の開発領域にとどめるのかを事前に決めておく必要があります。
業務プロセスとデータ構造の整理
PLMを正しく機能させるには、既存の業務プロセスと製品データの構造を整理することが不可欠です。部門ごとにバラバラだったフローやデータ管理の方法を見直し、全体で整合性の取れたプロセスに統一することで、システム導入後の混乱を防ぎます。たとえば、設計図や部品表(BOM)、承認フローなどが部門や担当者ごとに異なる形式で管理されていた場合、それらをPLMに取り込むためには、共通ルールや命名規則を定め、整理する作業が必要です。この段階での丁寧な作業が、PLMの運用精度を大きく左右します。
マスターデータ整備と教育体制の構築
PLM導入を定着させるには、マスターデータの整備とユーザー教育が欠かせません。たとえば、部品番号や設計図面のフォーマット、製品カテゴリなどの基幹データが不統一な状態では、PLM上での検索や共有が困難になります。そこで、データ入力ルールの標準化や、不要データの削除、重複の整理といったマスターデータ整備を事前に行う必要があります。また、新しいシステムに対する社内理解を深めるためには、ユーザー教育も重要です。操作研修だけでなく、「なぜこの業務が変わるのか」「PLMによって何が良くなるのか」を伝えることで、利用者のモチベーションと定着率が高まります。
ERPやMESなど他システムとの連携設計
PLMは単体で機能するシステムではなく、ERPやMES(製造実行システム)など、他のITシステムとの連携を前提として設計する必要があります。設計変更がERPの調達計画に反映される、製造現場の実績がPLMに戻る、といった情報の双方向連携が可能になることで、部門横断の最適化が実現します。そのためには、各システムがどのタイミングでどのような情報を必要とするのかを整理し、データ形式や連携手段(API、バッチ処理など)を明確にしたうえで、連携設計を進める必要があります。
PLMと連携する主要システム
PLMを最大限に活用するには、他のシステムとの連携も欠かせません。ここでは代表的なシステムとの関係性について紹介します。
ERP(基幹システム)との連携で業務効率化
ERPとPLMは、製品情報を中心に互いの機能を補完し合う関係にあります。PLMで作成・更新された設計情報や部品情報は、ERPに連携されて調達・在庫・生産管理に活用されます。一方、ERPでの原価情報や販売実績などもPLMにフィードバックされることで、製品開発におけるコスト設計や改善の材料となります。両者を連携させることで、部門間の情報断絶を解消し、製品開発から生産、出荷までをシームレスに接続する業務プロセスが実現します。
MES(製造実行システム)とのデータ統合
MESは、生産現場における実行データをリアルタイムで管理するシステムです。PLMとMESを連携させることで、設計情報がそのまま製造現場に伝達され、製造実績や品質データが設計側に戻るという双方向のデータ循環が可能になります。これにより、設計意図に沿った製品づくりが徹底され、不具合の早期検出や改善がしやすくなります。また、現場の作業指示や使用材料、進捗管理などをPLMと連動させることで、生産効率の向上にも寄与します。
BOP・BOM・MRPとの関係性
PLMでは、製品構成を管理するBOM(部品構成表)や、製造工程を定義するBOP(製造手順書)、資材所要量計画を行うMRP(資材所要量計画)との連携が重要です。設計段階で作成されたEBOM(設計BOM)は、製造現場に最適化されたMBOM(製造BOM)へと変換され、その内容がBOPやMRPに反映されます。この連携により、設計・生産・調達の各プロセスが一貫性を持ち、無駄のない製品供給体制が構築されます。BOMやBOPのバージョン管理もPLMの重要な役割であり、変更時の影響範囲の把握や迅速な対応を支援します。
まとめ
PLMは、製品ライフサイクル全体を横断して情報を管理・活用することで、開発スピードの向上、コスト削減、品質の強化を実現する戦略的なシステムです。導入にあたっては、目的や範囲の明確化、業務プロセスとの整合性、マスターデータの整備、他システムとの連携など、多くの検討事項がありますが、これらを丁寧に設計・実行することで、大きな業務改革と競争優位性の確立につながります。
関連記事
お役立ち資料/ホワイトペーパー
記事検索
-
物流関連2法
-
特定荷主