【実践的】SCM(サプライチェーンマネジメント)の導入ステップを解説。具体的な導入事例も紹介
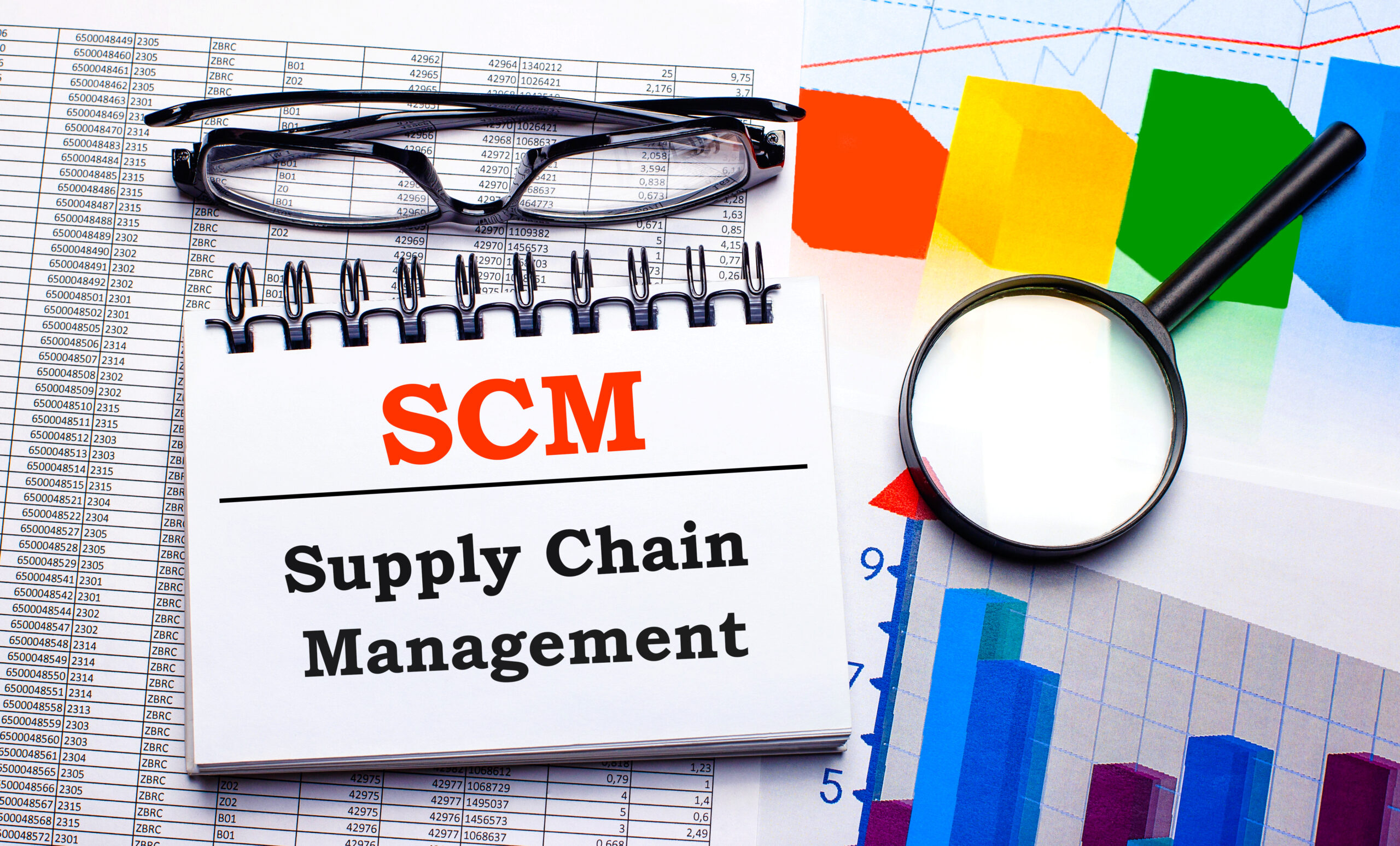
SCM(サプライチェーンマネジメント)とは、サプライチェーン全体のモノ・金・情報の流れを適切に管理する手法を指します。しかしながら、SCMの理論はわかるけれども、実際にどのように実践していくべきか悩んでいる方も多いのではないでしょうか。
本記事では、SCMを最適化する4ステップについて、物流DXパートナーのHacobuが解説します。
なお、Hacobuは物流DXコンサルティングサービス Hacobu Strategy(ハコブ・ストラテジー)を提供しています。物流業務の改善にお悩みがありましたら、以下をクリックしてご覧ください。
目次
本質的なSCMは、なぜ実現できないのか
物流クライシスが引き金となった改正物流関連2法がついに施行され、物流領域全体で主体的に「物流の効率化」を進めようとする動きが高まっています。物流効率化の本質は、サプライチェーン全体を俯瞰しながら最適化を図るSCMであり、これは新しい概念ではなく、いわば原点回帰といえるでしょう。
しかしながら、物流領域には多くのプレイヤーが存在し、企業間のパワーバランスなどによる壁があるため、進化しているデジタルテクノロジーの効果が一部にしか行き渡っていないのが現状です。その結果、本質的なSCMを実現できていないのではないでしょうか。以降で、SCMを実践するためのポイントは何かを解説します。
なおSCMの基礎や発展手法についての記事もぜひご覧ください。
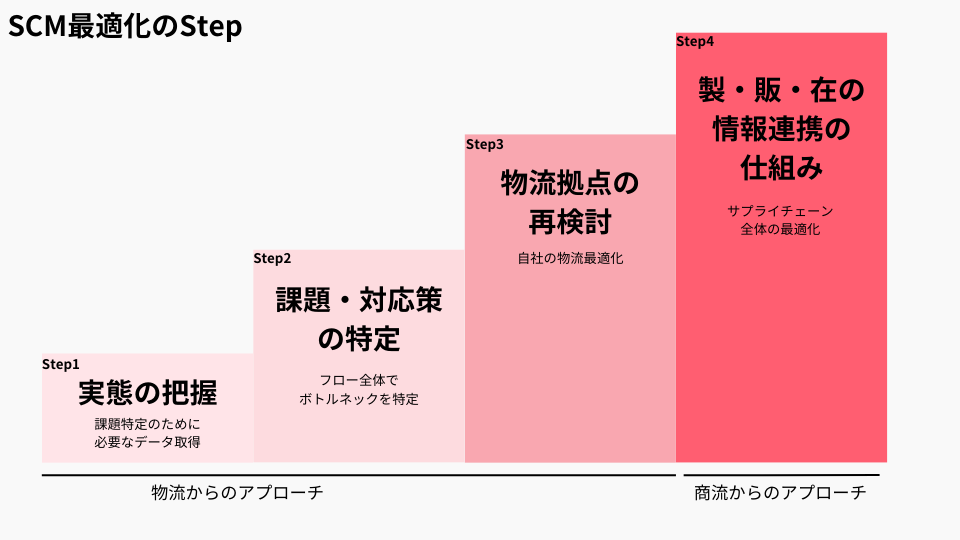
Step1:実態の把握
必要なデータの再定義と取得
企業がSCMを最適化するうえで、まず重要なのは、「課題の本質」を正確に把握することです。
しかし、多くの物流現場では、基幹システムやWMS(Warehouse Management System:倉庫管理システム)、TMS(Transport Management System:輸配送管理システム)を導入しているにもかかわらず、必要なデータを十分に取得できていない場合があります。
たとえば庫内作業において、SKU別の日次出荷量は把握できていても、ピッキングや荷揃えといった作業プロセスごとの生産性やボトルネックを明確に把握できていないケースが多く見受けられます。輸送においても、月間出荷ケース数やトラック台数といった大まかな情報は取得できているものの、日別・車格別に「どの製品を何パレット積載し、どれほどの積載効率で運んでいるのか」といった詳細なデータまで踏み込めていない場合が少なくありません。
ボトルネックを特定できなければ、どの部分を改善すべきかを的確に判断することが難しくなります。一方で、現在も多くの物流現場では紙ベースの指示書で作業が行われており、データ化が不十分なため、抜本的な改善点を見つけにくいという現状があります。まずは、必要なデータを明確に定義し、新たなデータの取得に取り組むことが重要です。
スナップショットではなくフローで考える
SCMにおいては、流れを最適化するアプローチが求められます。たとえば、トラックが指定の時間に到着しても、出荷用の商品がまだ荷揃えされていなかったり、人員が不足していたりすると、荷待ち時間が発生してしまいます。
庫内と輸送が同期できなければ、出荷プロセス全体の最適化は実現できません。どの時間帯にどのくらいの入出庫が集中し、どこで詰まりが発生しているのかを出荷フロー全体で把握することで、「実は必要な商品が集荷口に間に合っていない」といった本質的な課題を特定できます。
WMSやTMSから取得できるデータは、どうしても単一時点の情報(スナップショット)になりがちです。しかし、プロセス全体の流れをシームレスにつなげることで、生産性向上やコスト最適化の糸口を得ることが可能となります。
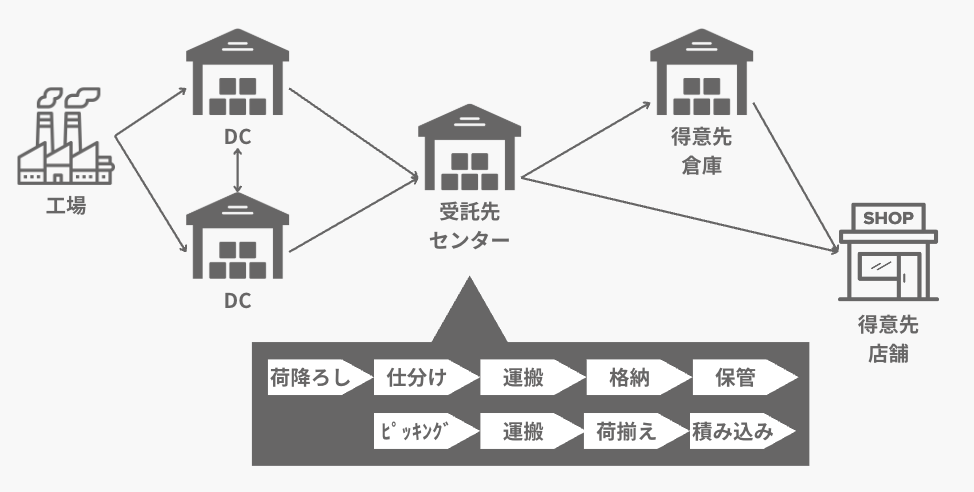
Step2:課題・対応策の特定
実態を正確に把握できたとしても、そのデータを活用し、ボトルネックや改善の余地を洗い出し、具体的な対処方法を検討しなければ成果にはつながりません。たとえば、庫内ではピッキング作業の集中によって滞留が発生しているのか、輸送では積載効率の低さが課題となっているのかなど、プロセス全体を俯瞰して問題点を明確化する必要があります。
そのうえで、課題に応じた対策を選択・実行していきます。具体的には、庫内作業においてはレイアウト変更や適切な人員配置、ピッキング自動化などのアプローチが考えられます。また、輸送面では積載効率を高めるためのルート最適化や、車両タイプ・台数の見直しといった施策が有効です。これらの対策が適切に実行されているか、また期待した効果が出ているかを継続的にモニタリングすることで、SCM全体の最適化を進めていくことができます。
Step3:物流拠点の再検討
本質的な課題を洗い出した後は、物流ネットワーク全体の再設計を検討することが重要です。その際、拠点の配置や役割、輸送モードの選定をネットワークシミュレーションで評価することが有効です。
慎重かつ綿密なシミュレーションが必須
新設と既存拠点の最適化では、アプローチが異なります。新たな拠点を設ける場合、土地や建物の確保だけでなく、それを活用する輸配送網の構築や、業者選定・業務プロセスの設計まで総合的に進める必要があります。RFP(提案依頼書)を複数の物流パートナーに提示する際には、規模やサービスレベル、コスト要件に加え、今後の拡張性やコントロールタワー機能の有無なども含めて総合的に評価することが重要です。こうしたプロセスには多大な労力がかかりますが、将来のSCMに大きな影響を及ぼす意思決定となるため、慎重に計画を立て、綿密なシミュレーションを行うことが不可欠です。
海外小売におけるネットワークシミュレーションの例
ある海外の小売業では、最初に周辺の人口動態や市場環境を詳細に分析し、ディストリビューションセンター(DC)の最適な配置を決定します。次に、WAD(Weighted Average Distance:運行当たりの平均輸送距離)などの指標を活用し、DCを中心に最適な位置と数の店舗を配置します。その過程で、ネットワークシミュレーションツールの最適化アルゴリズムを活用し、輸送制約や運行条件を考慮したうえで、総輸送距離が最小となる配置を算出します。最後に、温度帯や曜日ごとに変動する輸送量などの実運用上の要件を専門家が検証し、それに基づいて最適な調整を行い、より現実的な物流拠点構成を完成させます。
コストや投資に対するリターンだけでなく、環境面も意識する
近年、CO2排出量の削減は企業にとって重要な課題となっています。拠点再編に伴う輸送距離の変動は、CO2排出量に直接影響を与えます。前述の海外小売業では、物流ネットワークの拡大に伴い、WADを継続的に計測し、環境負荷を評価する仕組みを導入しました。一般的に、輸配送のCO2排出量は製造工程と比較して少ないとされていますが、拠点を新設する際には、建設時のエネルギー消費や日々の運用における電力・燃料使用量を含めたトータルの排出量を考慮する必要があります。
最終的に、拠点の配置や在庫の配置、輸送モードの選択が、コスト構造や環境負荷の最適化において重要な要素となります。既存拠点を活用する場合も、ネットワークシミュレーションを活用し、輸送経路や拠点間フローを再検討することで、コスト、リードタイム、環境面のバランスを考慮した最適な物流ネットワークを構築することが重要です。
Step4:製造・販売・在庫の情報連携の仕組み
SCMの最適化を進めるうえで重要となるのが、製造・販売・在庫の情報を一元的かつリアルタイムに連携させる仕組みの構築です。
販売計画をリアルタイムで共有することで、メーカーは生産量を最適化し、余剰生産を防ぎながら、需要増にもスムーズに対応できます。卸売業や小売業は、需要見通しの共有を活用し、適正在庫を維持することで、欠品や返品リスクを軽減できます。
輸配送においても、出荷量の変動を早期に把握することで、トラックや倉庫の手配を最適化し、余分なコストや時間の無駄を削減できます。こうした情報共有は、一企業内のITシステムだけでは十分でないため、サプライチェーン全体を統合するプラットフォームの導入が重要です。
Step3までは物流によるSCM最適化のアプローチでしたが、それだけでなく商流によるアプローチが重要です。
SCMの最適化ならHacobu Strategy
Hacobu Strategy では、以下のサービスを提供し、SCMの最適化を支援しています。
- 改革アクション策定支援 Logistics 100 Day Planning
- ネットワークシミュレーションと拠点再編
- 生産・販売・在庫管理サービス MOVO PSI
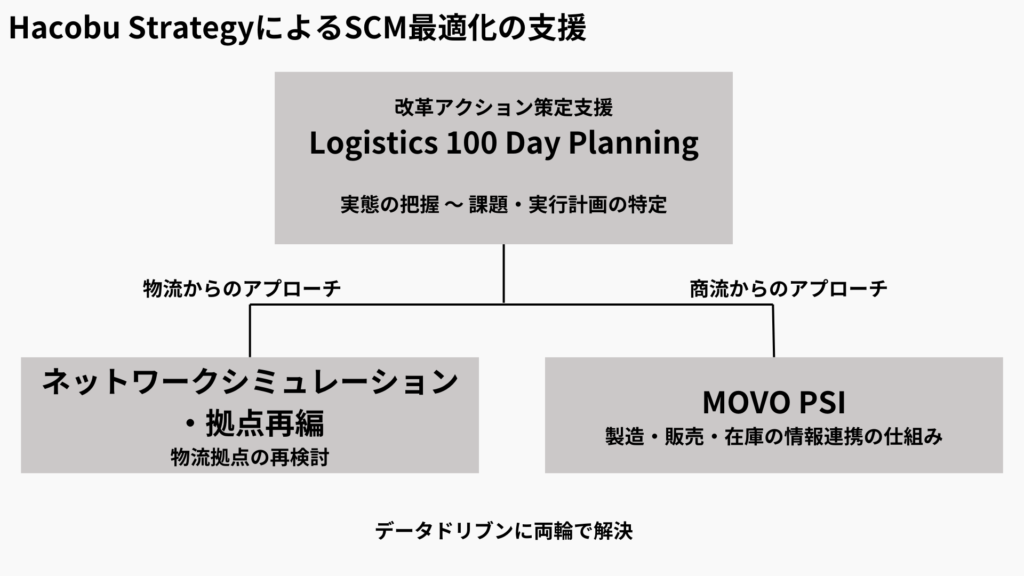
実態の把握 〜 課題・対応策の特定:改革アクション策定支援 Logistics 100 Day Planning
Logistics 100 Day Planningは、現状の物流ネットワークやオペレーションを整理し、課題の抽出と必要な施策の提示を行うサービスです。
基幹システムやWMSなどのデータを用いた定量的な分析だけでなく、現場視察やアンケート、ヒアリングといった定性的な分析との両方から真のボトルネックを特定することが特徴です。
現場の実態をデータでどのように解釈できるかを深掘りし、本質的な課題を短期間で突き止め、SCM全体の最適化に向けた改革・改善計画の立案までを行います。
実態の把握にはMOVOの活用もおすすめ
SCEの領域における実態の把握には、別途Hacobuが提供する物流DXツール MOVO(ムーボ)の の活用もおすすめです。
配車や積み降ろし、配送などの物流データがMOVO上に蓄積されるため、「どの荷物を、どのような荷姿で、いつ、誰が、どこからどこへ運んだか」といった詳細な情報を把握できます。基幹システムやWMSに加えて、MOVOのデータを活用することで、断片的な情報ではなくフローとして物流の全体像を把握したうえで、定量的に課題を導き出せます。
取得すべきデータなどの事前設計は、Hacobu Strategyでご支援可能です。
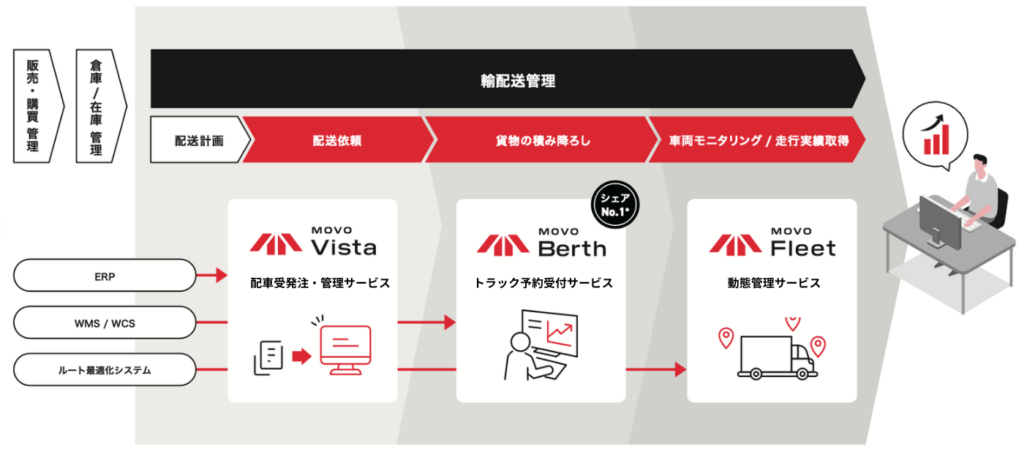
物流拠点の再検討:ネットワークシミュレーションと拠点再編
ネットワークシミュレーション
MOVOと物流診断で、現状の課題を明らかにした後は、課題点を解決し、経営戦略の実現に資する物流ネットワークを検討するステップに進みます。
物流施設の見直しには、数十億~数百億円規模(著者の経験では100億円超)の投資が必要となり、投資後は10年単位で使い続けるケースが多いため、慎重な経営判断が求められます。
Hacobu Strategyでは、AIなど先端のデジタルテクノロジーを組み込んだ物流シミュレーションツールを用いてデジタル空間にお客様の物流モデルを再現し、物流ネットワークの組み換えを支援します。
たとえば、拠点数の変更、立地の変更、DC・TCなどの拠点機能の変更といった複数パターンをシミュレーションし、トータル物流コスト・サービスレベル(納期)・CO2排出量などのKPIがどのように変化するかを定量的に確認できます。
このようなシミュレーションを正確に行うためには、現状の物流を正しく捉える基礎データの収集が重要です。その点で、MOVOから取得できる詳細なデータが大きく寄与し、高精度なシミュレーションを実現できることがHacobu Strategyの強みです。
拠点再編
ネットワークシミュレーションで最適な物流モデルを導き出したら、次は拠点再編のステップに移行します。
拠点再編のプロジェクトは、自社内の複数部署に加え、ディベロッパーやマテハンベンダー、システムベンダーなど、多数の社外関係者も巻き込むことになります。(著者が参画した生産材系EC事業者の拠点再編プロジェクトでは、実に約300名もの社内外の関係者が関与していました。)そのため、プロジェクトマネジメントの難易度は非常に高く、Hacobu Strategyは統合管理業者としてお客様のプロジェクト事務局の一員として、スムーズな拠点再編を支援します。
Hacobu Strategyは特定の業者にとらわれないベンダーフリーの立場で、お客様が拠点再編によって実現したい成果に合わせて最適なパートナーを選定できることが特徴です。また、物流拠点の設計におけるキャパシティー検討や、入出荷能力(スループット)の設定などは高度なデータ分析が欠かせません。これを疎かにすると、いざ移転を実行した後にキャパシティー不足で外部倉庫への追加投資が必要になったり、特定工程のみ自動化しすぎて結果的に無駄な投資となるなどのリスクがあります。Hacobuには物流現場に精通したデータサイエンティストが複数在籍しており、そうしたデータ分析を得意としています。これにより、拠点再編に伴うリスクを最小化し、SCM全体を最適化するための体制づくりを強力に支援します。
製造・販売・在庫の情報連携の仕組み:MOVO PSI
自社の物流拠点の再編だけでも物流効率化の効果は大きいですが、ブルウィップ効果に代表されるような課題を解決し、サプライチェーン全体の効率化を考える上では、「商流」の仕組みまで含めて見直すことが不可欠です。
Hacobu Strategyでは出荷先の発注オペレーションやデータ連携といった領域も含め、業界全体を変革することを目指し、生産・販売・在庫管理サービスのMOVO PSIを提供しています。
MOVO PSIは、メーカー・卸売業・小売業間をつなぎ、PSI(生産・販売・在庫)情報を一元管理・共有・分析するプラットフォームです。各企業は日々のデータを相互に活用して過剰在庫や欠品を防ぎつつ、在庫量や輸配送量の最適化を図ることができます。
MOVO PSIには2つのAI(機械学習)モデルが搭載されています。1つ目は卸売業や小売業からの受注を予測することで、在庫の変動を正確に把握し、必要なタイミングで必要な量を手当てできるようにします。2つ目は膨大な補充パターンを分析し、必要最低限の補充数量を毎日一定に保つための最適な方法を割り出し、現場の実務を強力に支援します。
これにより、輸送コストの削減や在庫効率の向上、欠品率の低減といった成果を期待でき、企業間を跨いだ連携が進むことで、サプライチェーン全体の最適化を実現します。
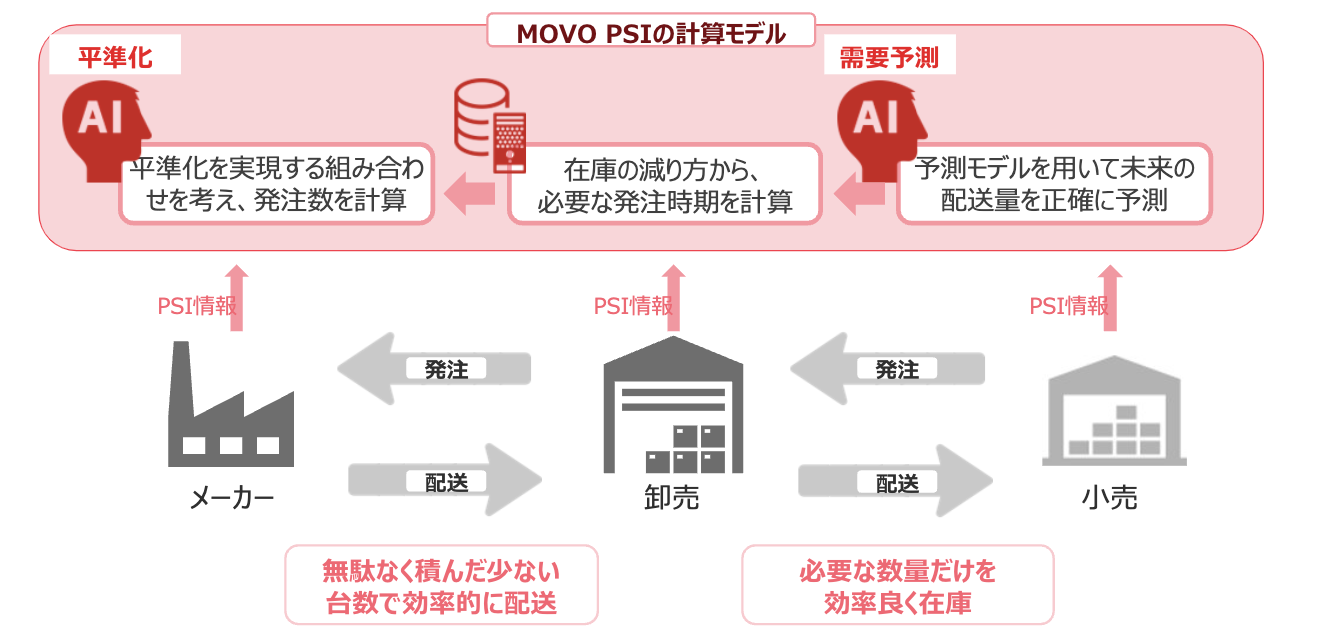
キリンビバレッジとアサヒ飲料の「輸送量平準化」の実証実験と成果
Hacobu、キリンビバレッジ、アサヒ飲料は、MOVO PSIのβ版を活用した発注数量の平準化を目的としたVMI拠点での実証実験を実施してきました。キリンビバレッジは、2023年10~11月の2か月のデータを用いて実験を実施。結果として、輸送コストを約9.1%削減することに成功し、在庫日数も約13.2%削減しました。実験に当たっては、例えば最低発注ロットなど実際のオペレーションと同じ条件を適用することで、導入時でも同等以上の効果が出せることを確認しています。アサヒ飲料は2024年3月~4月に実証実験を実施。より発注条件が厳しく、年始の需要変動が大きく難易度の高い2024年1月~2月の期間のデータを対象に実験しましたが、こちらも輸送コストを約6.2%削減、在庫日数を約6.5%削減することに成功しました。
まとめ
本記事では、SCMの実践的な最適化手法を解説しました。サプライチェーンにおける、各プロセスを効率化し、無駄なコストの削減や在庫の最適化、リードタイムの短縮を実現しましょう。
重要なのは、「課題の本質」を正確に把握するために必要なデータを取得することです。どのようなデータを取得すべきかお悩みでしたら、ぜひHacobu Strategyへお問い合わせください。
関連記事
お役立ち資料/ホワイトペーパー
記事検索
-
物流関連2法
-
特定荷主