物流センターの業務改善とレイアウトのポイント
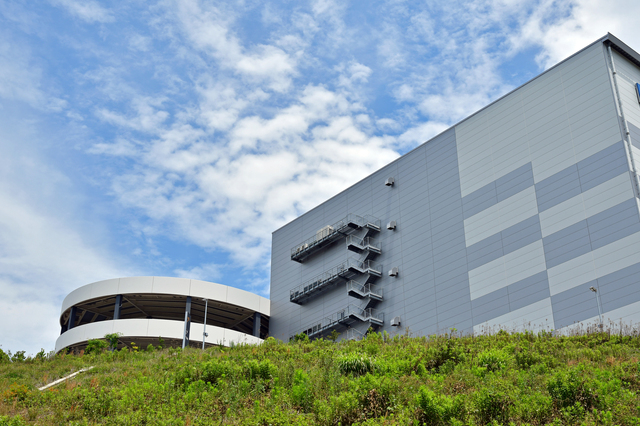
企業の経営戦略の中で物流の役割がますます重要視されています。物流の中心的な役割を担っているのは、物流センターと呼ばれる施設です。生産者から消費者へ安定した商品の供給を行うためには、「モノの流れ」を支える物流センターを如何に上手く運営するか要です。ここでは、物流業務最適化のために知っておくべき、物流センターのレイアウトや業務改善ポイントなどを解説します。
5種類の物流センター
物流センターは役割や規模によって5つに分類することができます。
DC(ディストリビューション・センター/Distribution Center)
在庫型物流センターのこと。在庫を保管・管理し、店舗別・方面別に仕分けをして小売店やエンドユーザーに納品することが役目の物流センターです。物流センターの中では入荷→検品→在庫管理→ピッキング→出荷といった業務を行っており、比較的大掛かりな設備が必要になる傾向にあります。
DC(Distribution Center)とは?TCとの違いや業務の流れ、導入するメリット・デメリット、再編する際のポイントを解説
DC(Distribution Centerʌ…
2025.04.21
TC(トランスファー・センター/Transfer Center)
通過型物流センターのこと。在庫を持たない、つまり保管機能がない点がDCとの違いです。主な役割は、入荷した荷物をすぐに小売店や物流センター向けに仕分け作業を行い、出荷します。DCと比べると比較的小規模で運営できる施設ではありますが、その一方で入荷後すぐに仕分けを行い出荷する必要があるため、各セクションの迅速な連携が求められます。
配送頻度が多いスーパーマーケットやコンビニエンスストア、大型量販店などはTCの利用が多く見受けられます。
TC(Transfer Center)とは?DCとの違いや業務の流れ、導入するメリット・デメリット、再編する際のポイントを解説
TCは、在庫|…
2025.04.21
PDC(プロセス・ディストリビューション・センター/Process Distribution Center)
流通加工・在庫型物流センターのことです。時にPC(プロセス・センター)とも呼ばれます。
DCでも包装、ラベルの貼り替えといった比較的簡易な流通加工は行いますが、PDCは、鮮魚や精肉の加工、部品の組立や設置といった専門機器・設備が必要な高度な流通加工までできることが異なる点です。そのため、防塵設備や温度管理設備等の工場さながらの生産ラインや労働力が求められます。
FC(フルフィルメント・センター/Fulfillment Center)
ネット通販で注文を受けた商品の物流センターのことです。機能は多岐にわたり、商品の仕入れやエンドユーザーからの受注、包装、発送、在庫管理、顧客データ管理、返品対応、クレーム対応、決済処理まで、すべて物流センターで完結することが求められます。まさにネット通販に必要不可欠なバックヤード業務全般を請け負う存在です。
エンドユーザー向けの出荷のため、出荷件数が多く、作業数も多い傾向にあります。そのため、人材確保が難しいと言われている近年ではコスト削減や効率化を図るために物流ロボットやAIの導入が盛んに行われています。
デポ(depot)
小型の物流拠点のことを指します。DC、TCなどから配送された商品を入荷し、多くの在庫を持たず、顧客に対して少量ずつ頻度の高い配送を行なうための施設です。
配送先の近くに設置され、配送距離やリードタイムの短縮、一時的な保管を担います。
物流センターの業務改善ポイント
物流に関わる方々は、より効率的に、よりコスト削減を目指して日々の業務を行っていると思います。作業の改善、ポカミス、ムリ・ムダ・ムラの3Mなどの改善は終わりがありません。
日によって入荷や出荷の数量に大きな変動があり、人員配置の設定が難しく、最小限の人員で仕事を回さなくてはならない物流現場では課題の特定が非常に難しい点があります。そこで重要になるのが工程管理と、後工程への意識です。
工程管理
入荷から出荷までの工程の中で、誰がいつ、どこで、どんな作業をしたのかをフィードバックする仕組みです。例えば1時間に入荷対応できる物量は何パレット分で、出荷のピッキングは1時間にどれだけできているのか、ピッキングから梱包が完了するまで何分かかっているのか、ピッキングが完了するまで現場のスタッフは“何歩”歩いているのかを知ることができれば、どの工程でムダやミスが発生しているのかおおよその見当がつきます。このように“実績”を収集し、現場の改善に役立てる活動が工程管理です。
後工程への意識
入荷、保管、ピッキング、流通加工、梱包、出荷の各業務では最適化していても、後工程を考えた全体最適がされていないと非効率になってしまう場面が多く存在します。例えば、梱包から出荷場に商品を移動する際、ラベルが見えるように商品を積み上げないと、検品が面倒になってしまうなどです。
このようなことを意識した上で、物流センターの業務フローごとに業務改善ポイントをご紹介していきます。
①入荷・入荷検品の業務改善ポイント
工程管理を従業員の負担をならずに行うために、現場のシステムを利用する方法があります。具体的には入荷予約システムと、ハンディターミナルを使用することが改善ポイントです。
入荷予約システムは、バース呼出し、入荷作業開始時間、作業終了時間などをリアルタイムで記録、処理を行えるため、別途記録を取る必要がありません。
ハンディターミナルは、荷物のバーコードから商品情報を読んで入荷予定情報と照合することで、自動的に入荷した荷物が合っているかチェックが可能です。目視と手作業では対応しきれないほど入荷数が多くても、照合作業の改善を行っておくとスムーズに遂行できるでしょう。
②入庫の業務改善ポイント
入庫の業務フローにおける重要なポイントは在庫数を正しく把握し「正確に入庫すること」です。誤って計上してしまうと、在庫管理システムや台帳に登録されている在庫数が実情と合わなくなってしまい、在庫差異が発生してしまいます。
これを防ぐためには、伝票突合や検品作業を入念に行う必要があります。また、入庫時に採寸計量器などを使用して商品サイズを採寸計量・マスター管理することで、梱包サイズの最適化や棚保管時の効率を向上することができます。
③保管の業務改善ポイント
保管の改善を行う際は、後工程である出庫の負担が減るように配慮する必要があります。具体的には、荷物を棚などに格納する際、あとでピッキングを円滑に行えるようにするため、取り出しやすさや通路からの視認性が良くなるようにロケーションを工夫するなどです。
④出庫・仕分けの業務改善ポイント
速さと正確性がトレードオフの関係にある作業といえます。急いだ分だけミスの発生するリスクが高まる可能性があります。
速さと正確性の向上施策として、デジタルピッキングシステムの導入があります。ピッキングする棚の場所、ピッキングする商品の個数を指示してくれるので、経験値が浅い従業員でもミスを減らせます。自動制御ロボットを利用するという手もありますが、費用面は大きな課題となります。
⑤流通加工の業務改善ポイント
内容や担当者によって効率が変わりやすい業務のひとつです。経験と作業のコツを多く把握しているベテランスタッフに頼ることが多くなりますが、そうした人材を確保し続けることは難しく、また業務の属人化が進むと当人以外が業務に携わるのが難しくなります。マニュアルの作成や研修の実施により情報・知見を共有し、スタッフを増やすことも重要です。
⑥出荷検品の業務改善ポイント
誤出荷を防ぐために、業務のため高い精度が求められます。2人体制や3人体制のチェックを行うケースがありますが、人件費や時間の問題で実施が難しいことも多いです。その場合、やはりハンディターミナルを活用して正確に出荷検品を行うことがポイントとなります。
荷物ごとにスキャンして納品先などの情報を確認していけば、誤出荷のリスクを大きく下げられます。
物流センター庫内レイアウトのポイント
物流センター業務の全体最適を考える
入荷から出荷までの作業工程を作業順で一筆書きの動線を作ります。入荷(荷受)、保管、移動、ピッキング、仕分け、梱包、出荷、棚卸のそれぞれの業務は効率化ではなく、後工程のことを考えたレイアウトにするのがポイントです。
移動距離から考える
庫内レイアウトは、倉庫で働く従業員の「移動距離」を考慮します。空走、荷探し、ピッキングの遠回りなどを削減し、移動距離を短くします。
出庫頻度を考える
出荷する商品の特長に合わせた保管レイアウト設計が必要です。定番商品など安定して多量に売れる商品や、流行品など一時的に爆発的に売れる商品、月数回だけの少量しか売れない商品などを同列、同方式で管理するのは得策ではありません。
レイアウトは、「ジャンル」や「仕入れ先」といったカテゴリー分けされていることが多いと思いますが、移動距離を効率的にするのであれば、出荷頻度に注目します。
在庫商品の出来高の多い順にA・B・Cのランクづけを行い、適切なレイアウト、配置に落とし込むABC分析という手法があります。
流動性・出庫頻度が高いAランク商品は作業効率を優先するレイアウトに配置し、出入り口付近に集中させたり、入り口から出口への最短距離の動線付近に集中して配置します。反対に流動性・出庫頻度が低いCランクは保管効率を優先します。
まとめ
物流センターの運用は物流戦略の要です。自社のニーズに合った物流センターを設置し、業務の改善を行っていくと、事業拡大や収益向上にもつながってくることでしょう。
物流センターの新設・移転をお考えの方は、以下資料もご参考ください。
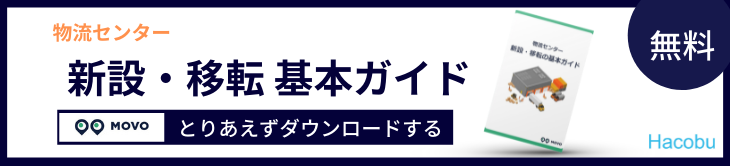
関連記事
お役立ち資料/ホワイトペーパー
記事検索
-
物流関連2法
-
特定荷主