ハウス食品の商品輸送がメイン1都4県共配エリアへ供給するDC
Q.まずは三郷物流センターの特徴からお聞かせいただけますか。
小山様:当センターはA倉庫(写真①)とB倉庫で構成されており、B 倉庫は外部業者へ賃貸しています。
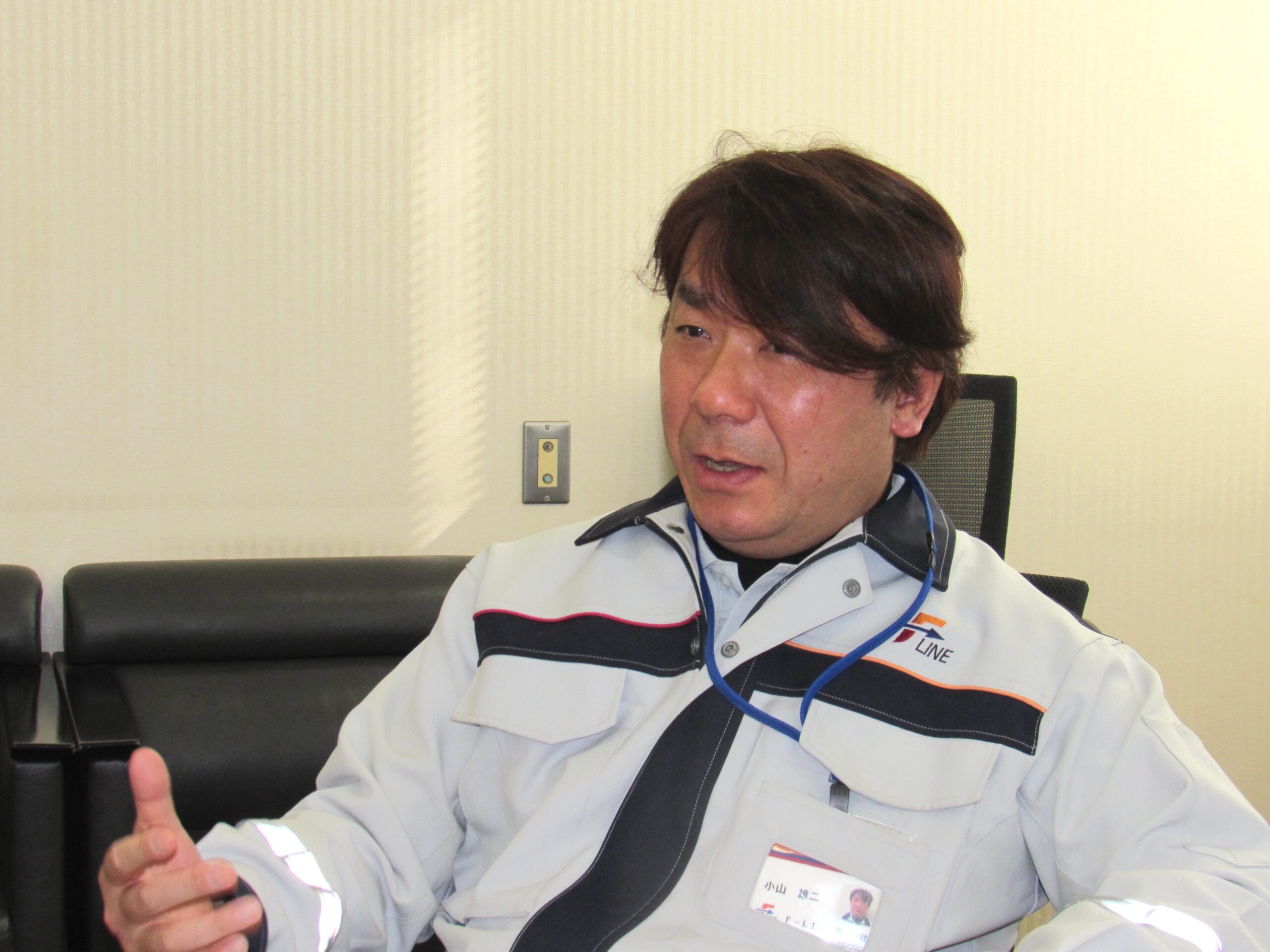
小山雄二様
2009年に設立されたA倉庫は1〜2階を合わせて4500坪の倉庫面積で、最大保管数は30万ケースの設定ですが、繁忙期は36万ケースほどあります。
A倉庫の特徴は、低床型と高床型のバースが両方設けられている点です。高床型バースは荷捌きの関係で、低床からパレット等の荷物を一度持ち上げてそれから確認をする二段階の手間がかかりますが、低床型ですとパレットで荷受けしたフォークリフトはそのまま倉庫内に入れるので1回の操作で済むわけです。
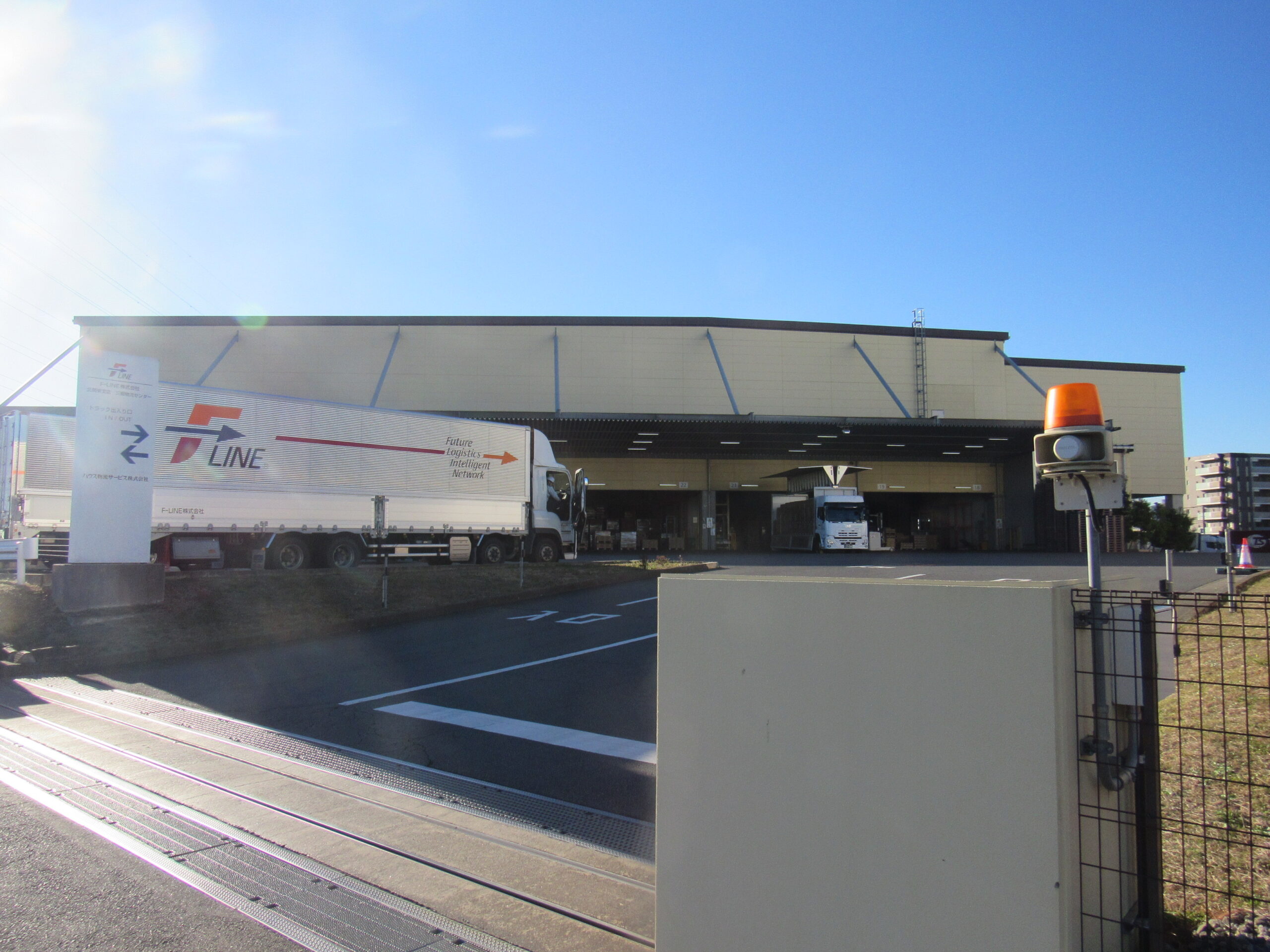
写真① 三郷物流センターA倉庫の建屋外観
Q.お取引先(荷主)を教えて下さい。
小山様:ハウス食品様(家庭用)と、ハウスギャバン様(業務用)です。そのほか、朝岡スパイス様等、スパイスを取り扱う企業様数社です。
A倉庫は、F-LINEと協業会社とのエリア共配におけるメーカー側のDC拠点という役割ですので、協業会社が持つエリア共配車両に当センターへ集配していただくことが多いです。エリア共配車両は共配拠点まで運び、仕分けして配送してもらっています。当センターの商品の届け先は卸の物流拠点になります。
田所様:ここから1都4県のエリアに荷物が運ばれる拠点です。例えば、埼玉県でもいろいろなセンターや卸からのものを、運送会社に持っていってもらい、そこで仕分けをして各店舗へ届けてもらうわけです。
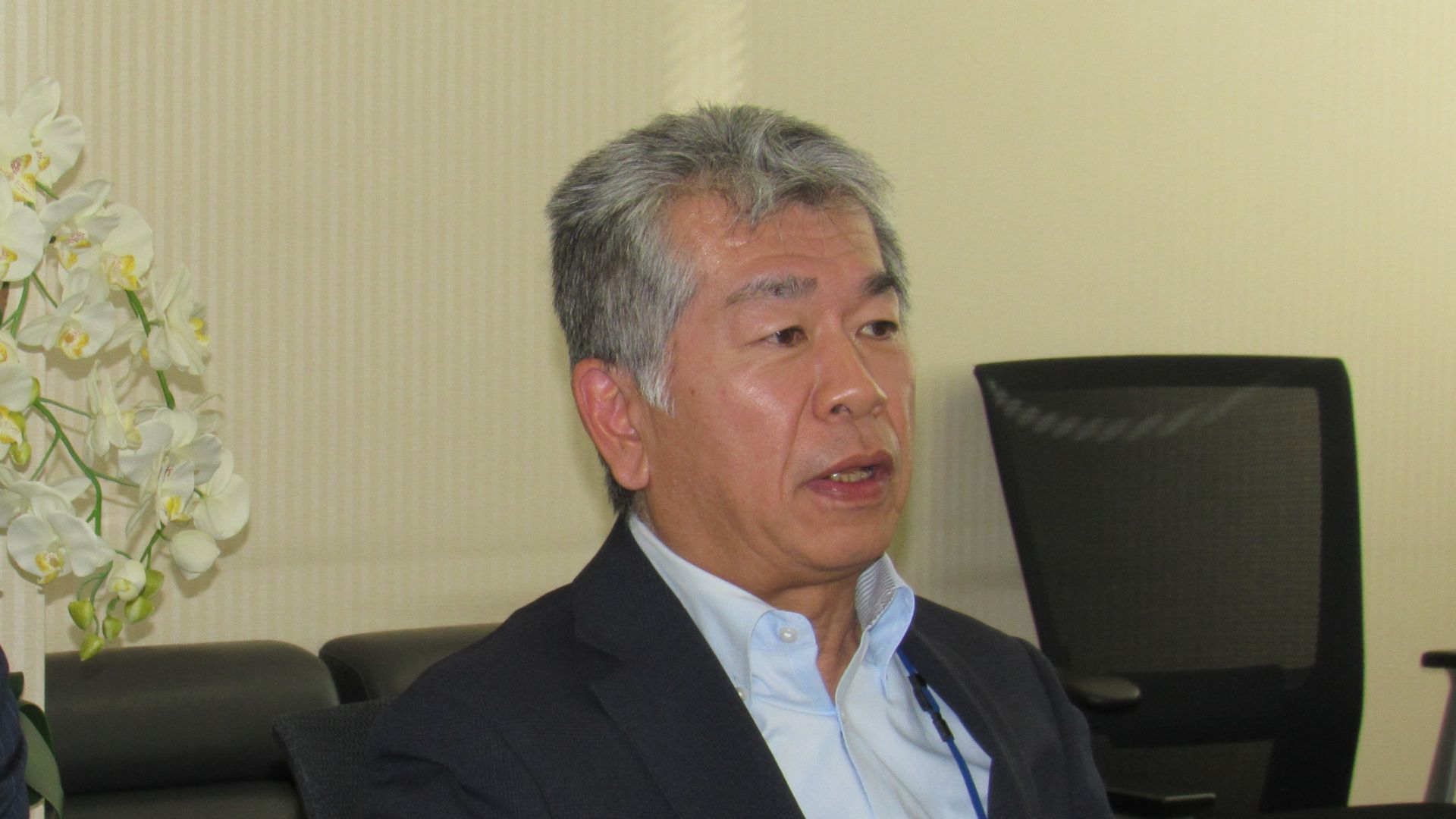
田所朋也様
小山様:当センターはそれらの運送会社に向けての物量をトータルで出すだけなので、その点は楽です。ここから出発してトラックに乗せる分は店舗ごとに仕分けが必要ですが、協業の運送会社に任せるものは、一括して送り出し、向こうで仕分けをしていただく。作業効率はとても改善されました。
Q.現在、1日の出荷台数はどれくらいですか。
小山様:25台、引き取りを合わせると40台程度です。今後はもっと減らして、各エリアにお願いして行く予定です。以前はここの直送車両だけで50台以上ありましたが、この2〜3年でかなり減らしました。
Q.引き取りの車両が多いので、待機車両が結構出た面もありますか。
田所様:朝積み、早朝に積んでそのまま直接出かけるトラックの台数が多く、さらにそこに入荷車両も入ってきますから、たしかに庫内が混乱していた面はありました。朝積みの出荷車両を減らしつつ、今回はHacobuのバース予約システム「MOVO Berth」を導入して、入荷車両の時間制限を掛けて交通整理をしたわけです。
小山様:一方、ハウスギャバン様の業務用製品は、北海道を除く関東甲信越全域と、家庭用とは配送エリアが全く異なります。また、細かいものが多いため、路線便を中心に輸配送の形態も異なります。
その他の業務として、バンニングと呼ばれる輸出貨物をコンテナに詰め込む作業や、輸出製品のラベルを変える流通加工の作業も行なっています。こちらは小口の部分で詰め合わせの商品がありますので、細かいものをピッキングして箱詰めして出荷する作業もあります。
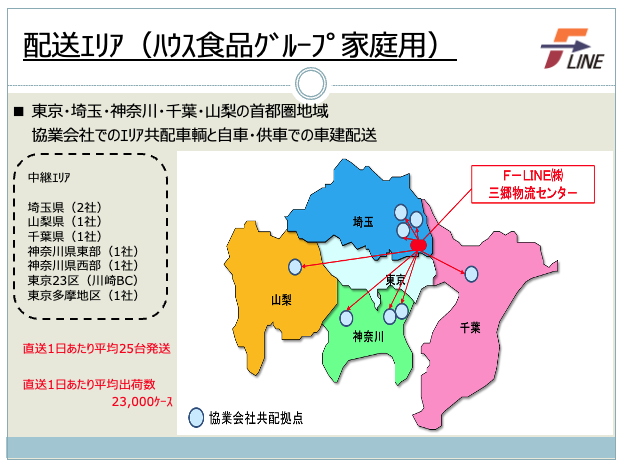
図表② ハウス食品グループ家庭用商品の配送エリア
入出庫の車両混雑と非効率業務を解消 ドライバーへの普及度も導入の決め手
Q. 「MOVO Berth」を導入した経緯からお聞かせいただけますでしょうか。
小山様:先程、現場説明を担当した鈴木が2019年に東京ビッグサイトで行われていた国際物流総合展でHacobuと顔見知りになったのがきっかけでした。鈴木は2024年問題もあり、この先のことを考えるとバース予約システムをはじめ、何かシステムを導入した方が良いのではという気持ちがあったようです。その後、当社の相模原の物流センターで「MOVO Berth」が導入され、Hacobuの当社担当者から「三郷物流センター様では、何かお困り事はありませんか」と連絡をいただいたのです。
当センターはちょうどその頃、入庫業務に課題を抱えていました。先着順の受付と倉庫員誘導のため特定時間帯に車両が集中し、待機が2〜3時間発生していたのです。入荷は深夜2時から朝8時の受付でしたが、ドライバーさんが2時頃の時間帯に集中して来てしまうのです。その結果、2時に来ても入荷作業のスタートは5時以降ですから、3時間も無駄に待機していることもあり、問題は認識していました。
また、当センターの敷地は車両待機のスペースが少ないほか、隣のB倉庫に関連する車両も来てしまうので、駐車場は非常に混雑していました。そのため、結構敷地内で「当たった」「こすった」とかトラック同士の接触事故も多かったのです。加えて、敷地の外で待機するドライバーと、バースの空き状況を発信する倉庫、事務所との間で何度も電話連絡をしなければならない等、様々な点で業務が非効率でした。ドライバーに電話しても出ず、皆で探し回ることもよくありましたね(笑)。
Q. 入荷受付を2時からにしていた理由は、慣習的なものですか。
田所様:それもありますが、朝積みの出荷車両の台数は物量に応じて日々変わるのです。それによって多い時は遅くなるし、逆に少ない時は早まるわけです。
小山様:2時にしているもう1つの理由は、分散です。入荷トラックは1日30台程度ですが、例えば、早朝5時に「入荷開始」となると、事務所で受付表を書いてもらうのもドライバーが集中して大変です。ですから2時に最初に書いてもらいながらも、開始は5時というような、要するに受け側の都合でそうしてきた面もあります。
Q. そうせざるを得ない面もありますね。
小山様:こういった状況をHacobuに相談したところ、まず、入荷車両の待機時間や、非効率になっている運用を可視化して改善していきましょうと提案がありました。特に、待機時間の長さは2024年問題の時間外労働の上限規制に直接関わってくる課題です。
当センターとしては、入荷するとすぐ荷下ろしができるセンターという印象付けを行いたいとの思いもありましたので、入荷車両の待機時間短縮によるドライバーの拘束時間の改善と、倉庫・事務作業の効率化を目標に「MOVO Berth」の導入を決めました。実際のシステム稼働は2023年9月から開始しています。
また、「MOVO Berth」の普及率が高かったのも導入の決め手になりました。1万拠点以上の利用実績(取材当時/※1)があり、46万人以上のドライバーが登録している(取材当時/※2)というシェアの高さは、安心につながりました。ドライバーに訊くと、大概「ああ、あのシステムね」「大体のやり方は知っている」という返事が返ってきました。
このシステムの良さは、何と言ってもすべてが一気通貫という点です。発拠点の配車マン、ドライバー、そして、荷受け側倉庫の事務所と庫内作業者が、PCやタブレット、スマホ等を通じてやり取りすることで、入庫時間の調整、バース指示、作業完了報告まで、1つの画面ですべてが見渡すことができます。これまで全部バラバラで動いていたことが、一気に可視化され、コントロールできるようになります。ドライバーと倉庫作業者のやりとり全部を一人が同じ画面でできます。
当センターでは作業指揮者を4〜5人置き、その指示で作業スタッフ皆が動くようになっています。その指揮者が流れをきちんと把握できる点がいいですね。その作業の状況に応じて作業者の振り分け等も1回で可能で、作業指揮者も皆「やりやすくなった」と言っています。
Q. システムの導入前と導入後の違いを説明して下さい。
小山様:図表③は「MOVO Berth」導入前のフローですが、2時に到着しても、実際に荷下ろしするのは5時頃だとか、「8時に来るようにと指示を受けている」といった混乱が生じていました。
また、入荷車両からは出発後、「明日そっちに行くのだけど、何時から下ろせるの」と問い合わせがくる。これらの問い合わせが意外と多く、その対応をするために、事務のスタッフにも負担がかかっていました。ドライバーの気持ちとしては分かりますが、本音を言えば、それは発側に聞いてほしいというのはありました。
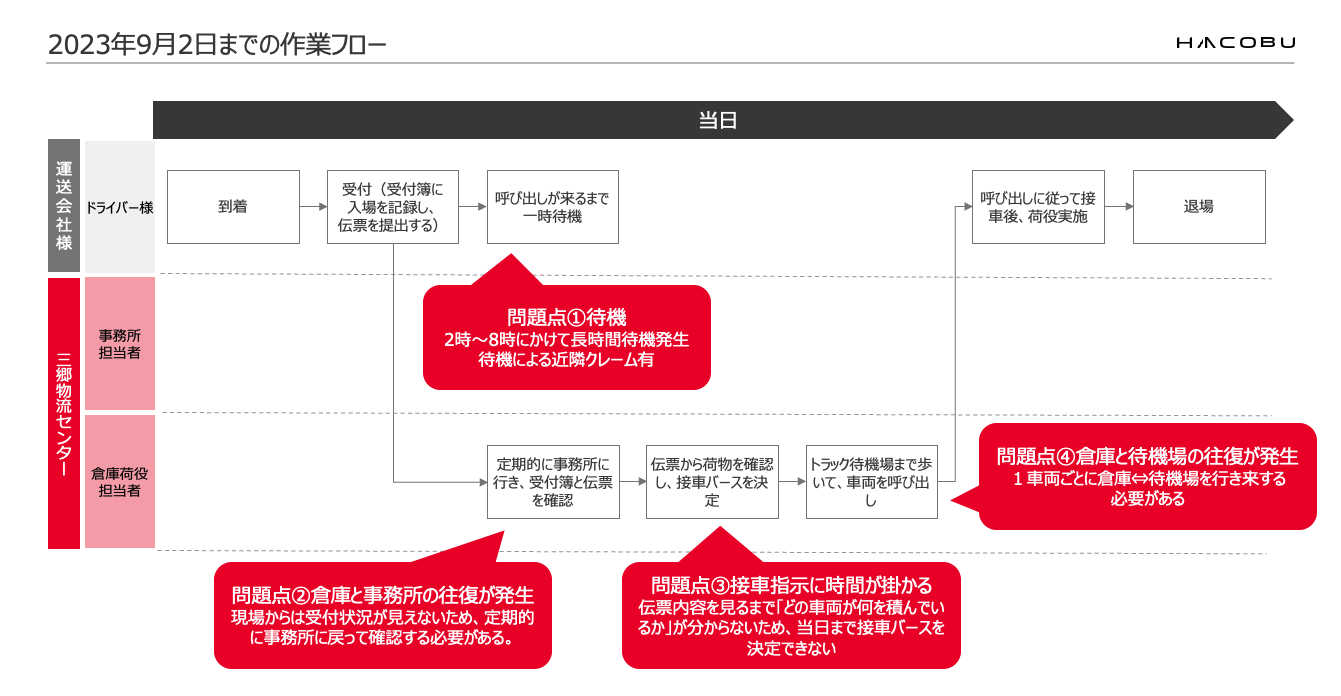
図表③ 三郷物流センターの「MOVO Berth」導入前の作業フロー
その上、伝票で荷物を確認して割り当てたりする作業のため、庫内と事務所をあちこち往復する等の手間がかかる一方、その際にドライバーはセンターの敷地内に停められないと外で待機しているのですが、周囲は住宅街なのでクレームが入るのです。何度も警察を通じてクレームがあり、やがて毎日、周辺をパトロールされるようになりました。
トラックの待機場所もなかなかないのはわかるし、大変だとは思うのですけれど、「ごめん、ここにいたら通報されちゃうから動いて」と言わなければならない場面も多かった。このように、様々な不都合があったのです。
Q. なるほど。
小山様:そうした不都合も「MOVO Berth」を導入してからは大きく改善されました。図表④は、導入後のフローですが、作業が大幅に削減され動きが整理されています。
入庫予約を入れてもらうと、すべて画面にそれが並びます。それを組み合わせて、「この時間にこうしよう」とか、「15時までに入れてくれれば16時までには返します」など、スムーズに予約が把握できます。
また前日15時までにいただいた予約に関しては、16時までに確定し、SMSでお知らせできるようになりました。注意書きも全部そこに書いておくので、問い合わせの電話もなくなりました。
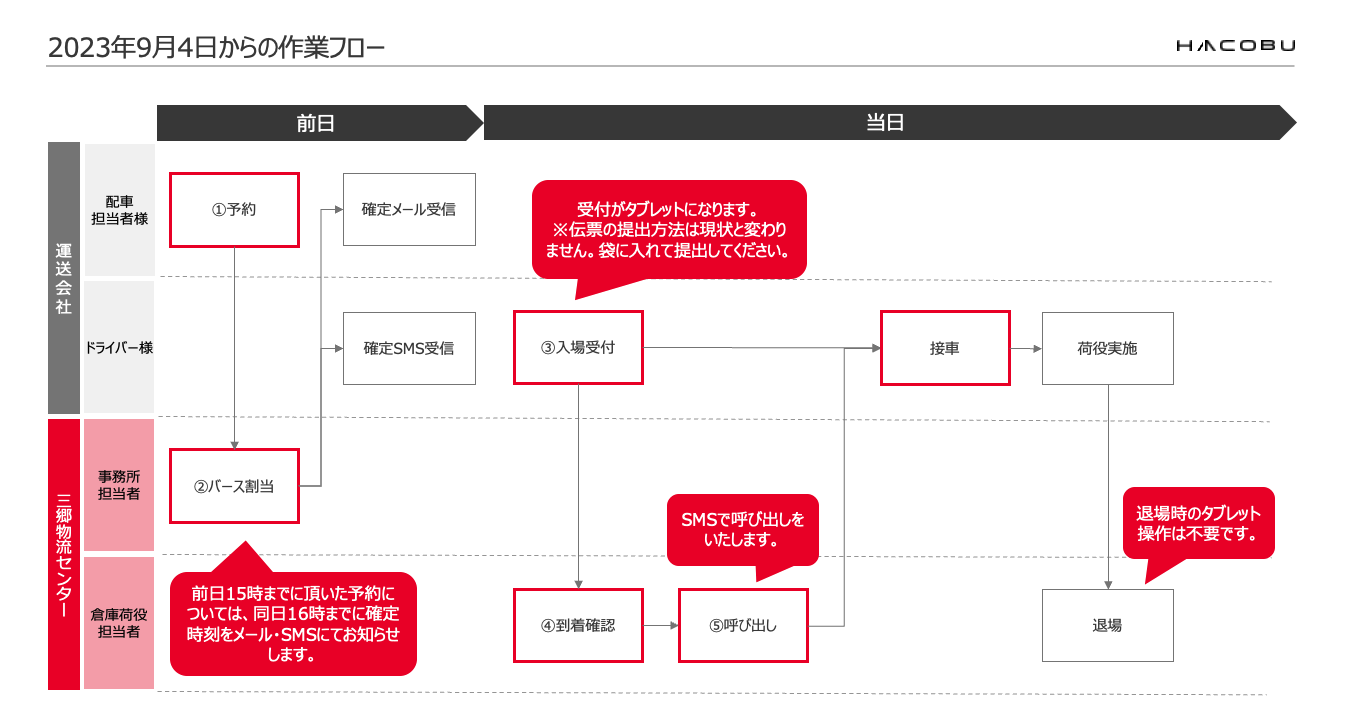
図表④ 三郷物流センターの「MOVO Berth」導入後の作業フロー
また情報を更新すれば、常にSMSがドライバーに届くようになっています。時間変更などがあっても、ドライバーにもすぐに伝わるので混乱を抑えられます。さらに、呼び出しができるので、あちこち探し回らなくて済むようにもなりました。「何番バースにつけて」と送信するだけでいい。
動き回らなくて済むから、スムーズになった。効率化というのが本当に目に見えてわかりました。
作業時間見える化、待機時間削減 「作業カード」は1時間から40分に短縮
Q. 導入効果について詳しくご説明いただけますでしょうか。
小山様:まず作業時間が可視化された点が挙げられます。これまではパレット下ろしは30分ぐらい、バラ下ろしは2時間くらいかなと感覚でしか捉えていなかった作業時間が、データで正確に把握できるようになりました。
「MOVO Berth」を導入して実績を取ってみると、パレット下ろしの作業時間は11〜20分、バラ下ろしは40〜50分、全体で30分程度であることがわかりました(図表⑤)。
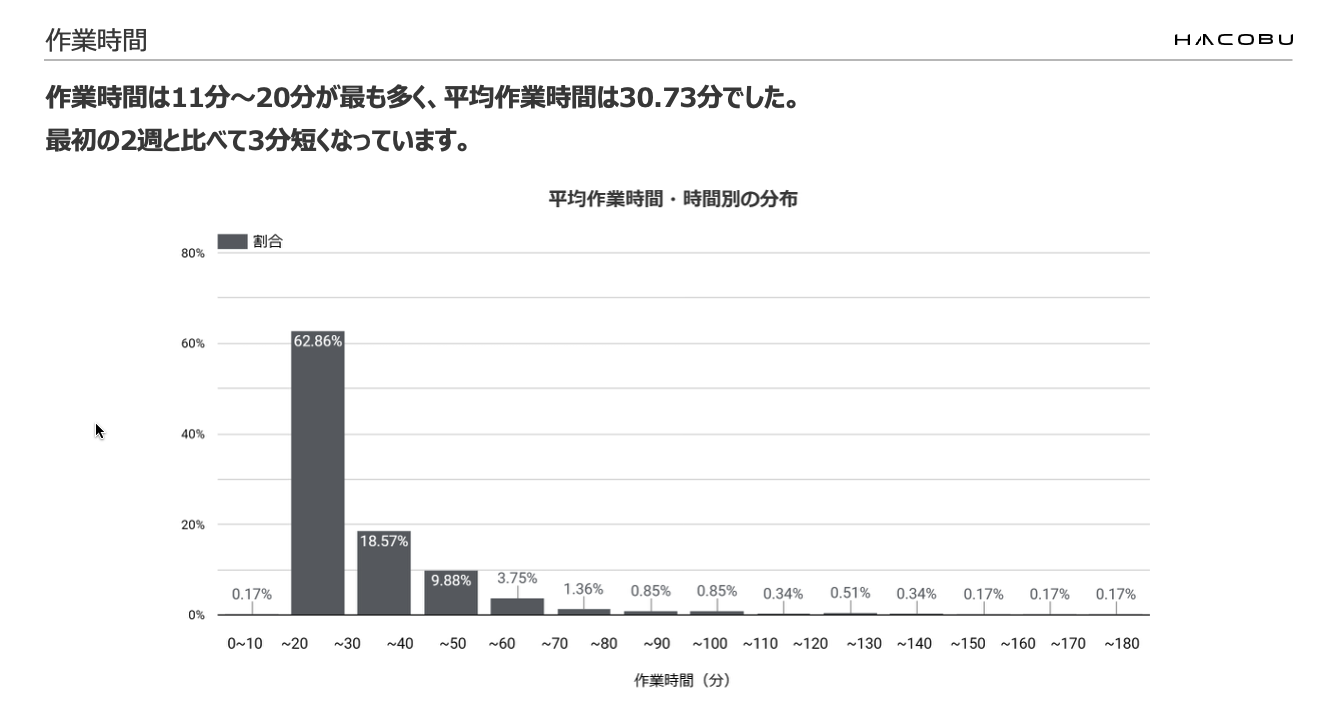
図表⑤三郷物流センターの「MOVO Berth」の導入効果(作業時間)
Q. 入荷作業時間を把握し、類型化できたわけですね。
小山様:はい。「待機時間の削減」について、「MOVO Berth」導入後は、30分以内の待機時間が実に91.47%に上り、平均で11分しか待っていないわけです(図表⑥)。
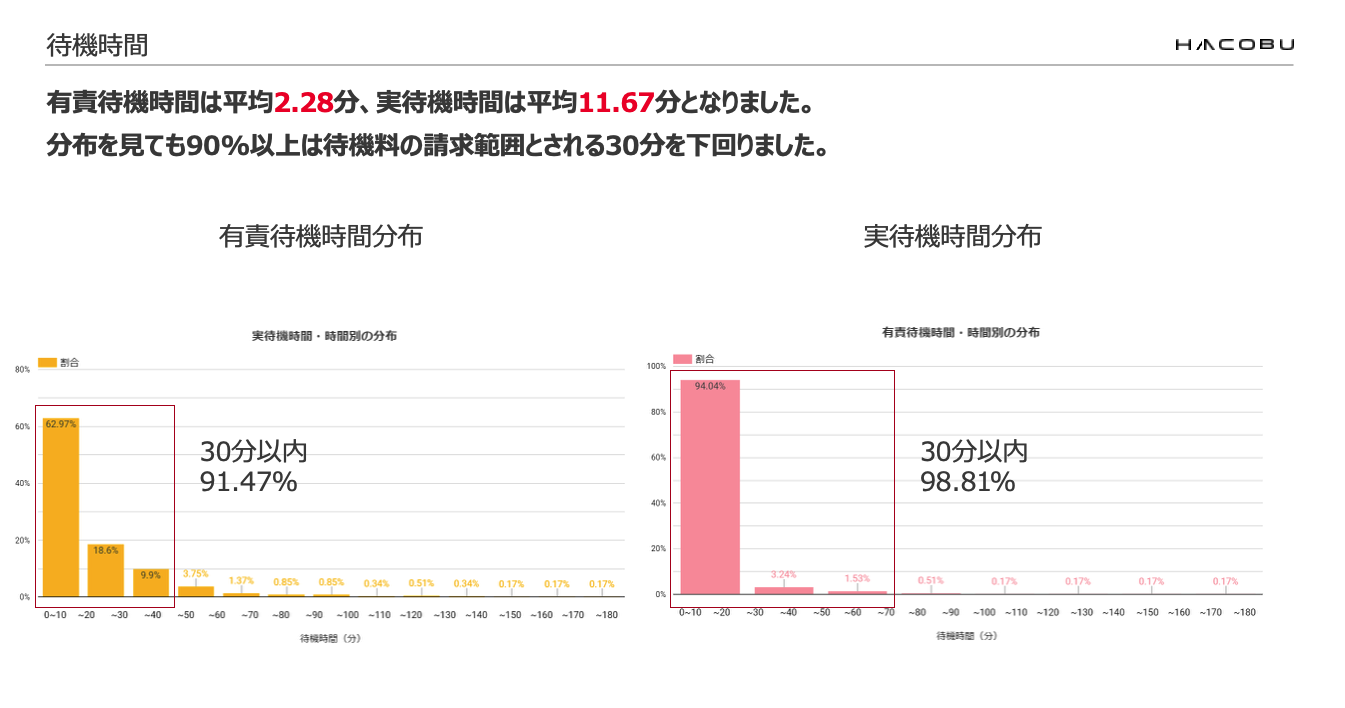
図表⑥ 三郷物流センターの「MOVO Berth」の導入効果(待機時間)
吉濵:以前は2時に受付をして5時から、場合によっては8時から等と2〜3時間は待たせてしまっていましたが、今は入場して受付ボタンを押してから平均10分程度で荷下ろしが開始されています。
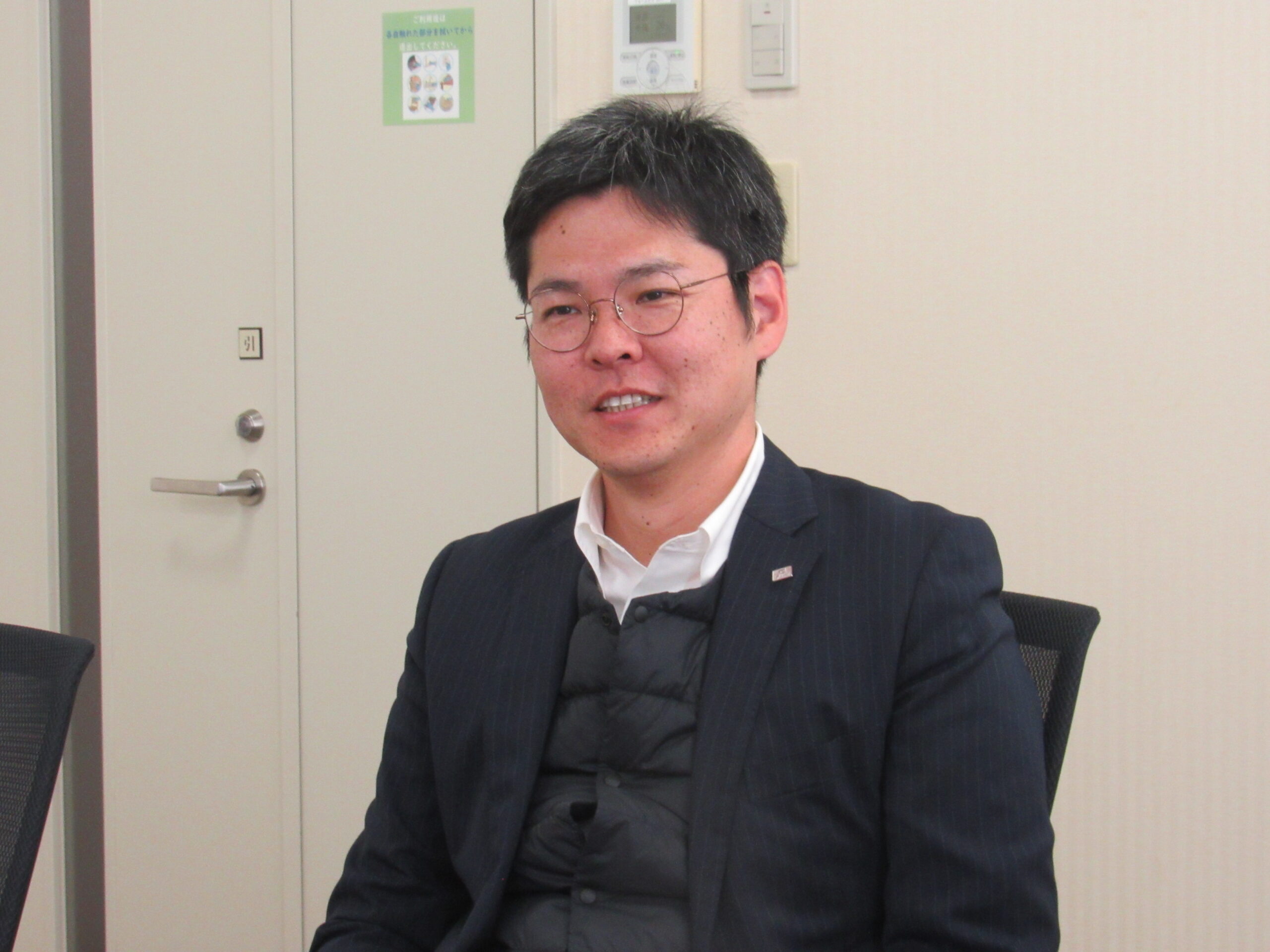
吉濵暁様
小山様:2〜3時間の待機も、きちんと整理すれば10〜11分程度しか待たずに済むわけです。
さらに、予約ありの人の待機は2分という数字も出ています(図表⑦)。予約なしでもだいぶ短縮されましたが、やはりなしとありでは全然違います。この数値があるから、「予約入れてくれれば、これだけ早くできます」というアピールにもつながります。
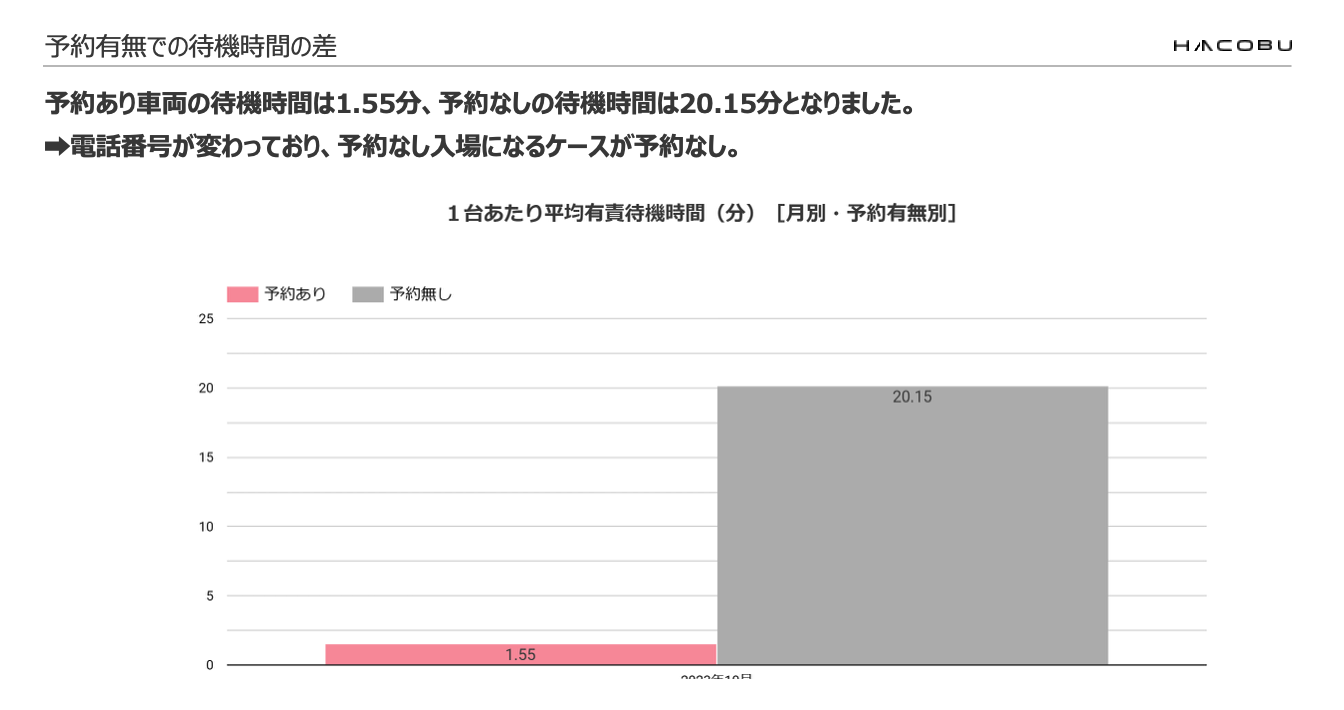
図表⑦予約有無での待機時間の差
また、我々は午前10時までに作業を終わらせることを目標にしていますが、円グラフでわかる通り、10時までに作業が終了しない車両がまだ51台、全体の8.7%あります。「MOVO Berth」では、車両ごとの「作業カード」をバース表に割り当てて作業計画を管理しますが、現在はカードの長さを1時間で設定しています。ただ、実際の作業実績をみると、先ほどもお話したとおり、バラ下ろしでも平均30分です。この1時間の設定を例えば40分にすることで、これまで2台で計画していたところに3台を割り当てることができることになります。このように、作業時間を可視化することにより、より精緻な計画を立て、バースの稼働率を上げることで、10時までに作業を終了できる割合も増やせるのではないかと考えています。
Q. 1時間だった枠を40分ですか。 凄いですね。
吉濵様:「MOVO Berth」の導入前は、入荷作業がお昼の12時頃までかかっていました。それが今は10時を目標にして91%を達成しました。そこでさらにこの51台分を前倒しにするために、もっとバース作業の効率化を進めようということです。
Q. 導入にあたって、関係各社向けの説明会等は行いましたか。
吉濵様:協力会社への説明会は15社ほどで行いました。その窓口から栃木や大阪、九州等の孫請けの手配元へお話してもらっています。
Q. 協力会社も「MOVO Berth」を契約しているのですか。
小山様:いいえ、基本的に導入拠点との契約ですので、F−LINEの三郷物流センターだけが支払い元となります。使用するドライバーや予約する配車マン等は費用がかかりません。
Q. 下請けや孫請けまで入れると、相当数になると思いますが、皆さん「MOVO Berth」を使っているわけですか。
小山様:全体で100社いくかどうか、ドライバーの数で言えば100を超えますが、もちろん皆様に使ってもらっています。
吉濵様:その結果、作業効率は改善してきて、午前中の仕事が大分スムーズになりました。当センターの出荷は、まだ今日受注を受けて明日の納品。つまり、D1です。ですので、午前中に入荷作業が終わっても実際に出荷を始めるのは午後の1〜2時です。
今後は、2024年問題を絡めた動きとして、D2の流れ、受注してからお届けが翌々日の流れに変わってくるのではないかと予測しています。そうなった場合、10時までに入荷作業が終われば、午前中に出荷作業もできるわけです。こうして早め早めに動けることによって、積込み時間までドライバーを待たせることもなくなり、倉庫の効率も良くなります。当センターの従業員も遅くまで仕事をしなくて済むようになるでしょう。
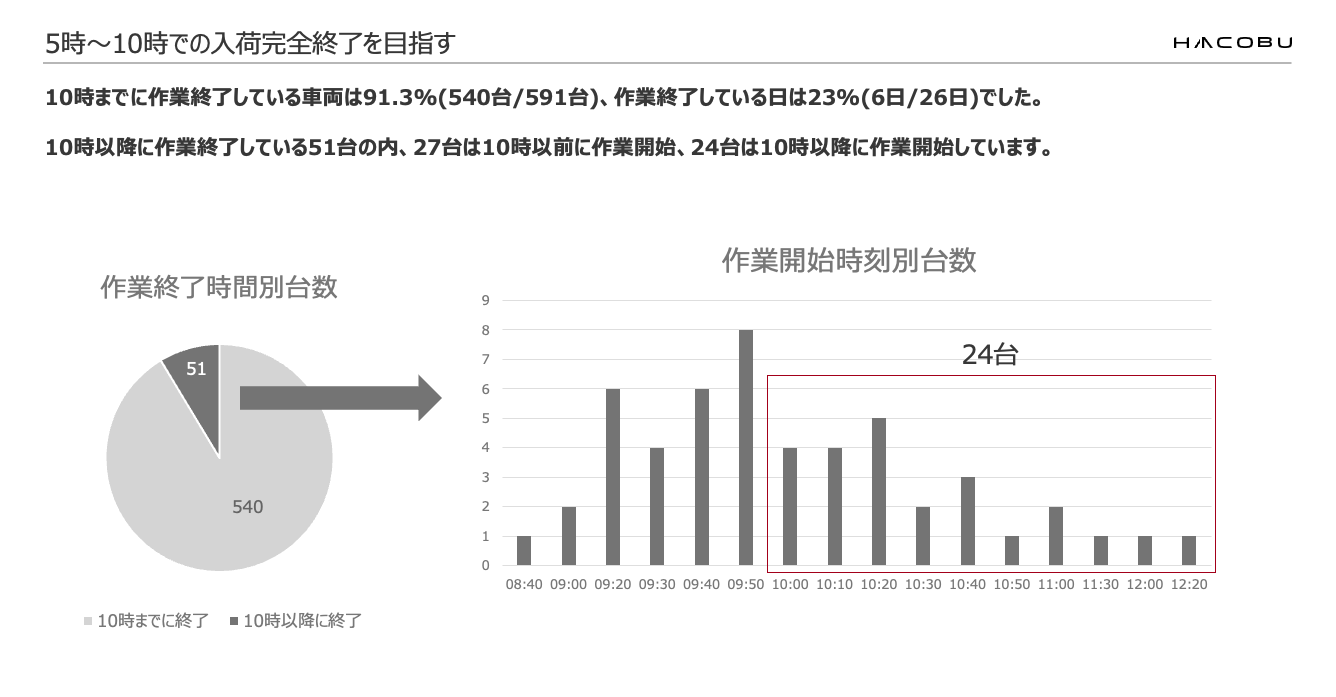
図表⑧バース効率化に伴う作業時間終了時間の早期化
Q. 今後の課題をお聞かせ下さい。
小山様:1つは、先程も紹介した作業カードの長さ見直しです。1時間を40分に短縮することにまさに取り組んでいます。作業状況が見えたことで、カードの長さを40分にしても運用が回ることがわかりました。ここを精緻化してバース効率を上げたいと思います。ただし、詰め込みすぎると作業員の休憩時間がなくなりますので、そこは臨機応変な対応が必要です。
次に、呼び出しから反応が遅い車両への対応は、まさに今後の課題です。受付後の待機中に、ドライバーが疲れて寝てしまうと、呼び出しても反応がない時があります。その場合、うちのスタッフが行って起こしていたのですが、原則としてそういう対応はやらないようにと伝えています。
これをやり始めると、「起こしてくれるから」とルーズになったり、「起こさないとクレームになったり」もします。呼び出しても反応がない場合、1回電話する約束にしています。それでも反応がない時は、そこにいようがいまいが、最後に回っていただくことにしました。厳しいようですが、そうしないと全体がグダグダになってしまうためです。
そのほか、出荷車両や庫内作業把握等の活用拡大も今後取り組みたいテーマです。今、入庫でこれだけできるようになりましたので、これを出荷車両や庫内作業の管理に活用できないか、と考えています。
Q. 新たな取り組みにも期待しております。本日は貴重なお話を誠にありがとうございました。
※1 利用事業所数とは、MOVO 導入拠点に加えて、MOVO を利用する事業所のIDを合計した数字。掲載されている数字は、2023年12月の取材当時のもの
※2 累計登録ドライバー数。利用者が「MOVO Berth」を利用する際に登録するドライバー電話番号の累計ID数。掲載されている数字は、2023年12月の取材当時のもの