Q.まずは会社概要について教えてください。
ユニリーバは、ビューティ&パーソナル領域を始めとして、世界約190カ国にブランドを展開し、毎日25億人以上から選ばれている世界最大級の消費財メーカーです。ユニリーバは創業当時から、ビジネスを通して社会の課題を解決していきたいという想いを持ち続けてきました。「サステナビリティを暮らしの“あたりまえ”に」という目的のもと、2010年には「ユニリーバ・サステナブル・リビング・プラン」(USLP)を導入。ユニリーバのUSLPの目標の多くがSDGs(持続可能な開発目標)と深く関わっており、USLPの目標を達成すれば、ビジネスを成長させながら、SDGsの17の目標すべてに貢献出来るようになっています。
カスタマーサービスロジスティクス部門としては、「革新・協働を通して、日本に関わる流通を持続可能なものにし社内外から選ばれるTEAMになる」というビジョンを掲げており、「持続可能であること」は会社としても部門としても重要なテーマになっています。
Q.ムーボ・バース管理ソリューションが導入された拠点について教えてください。
今回、トラック予約受付サービス「ムーボ バース」を導入したのはユニリーバ・ジャパン株式会社相模原工場(以下、相模原工場)です。非食品の工場として、ラックスやダヴ製品等の製造を行っています。敷地は広くはないのですが、24時間7日間稼働の工場として、グローバルでも5本の指に入る生産効率性の良い工場です。
他社との中継・共同輸送プロジェクトで工場の車両待機が大きな障壁になっていた
Q,導入する以前は、どのような課題をお持ちでしたか。
実は今回「ムーボ」を導入する前に、当社ではあるプロジェクトが実施されていました。複数発荷主、着荷主、倉庫、運送会社、パレット会社など関係企業様と共同で行った「スワップボディコンテナを活用した中継輸送の実証実験」というプロジェクトで、「ドライバー労働条件改善、実車率・積載効率向上、環境負荷削減」を目指し、従来7台のトラックが交互に運行していたケースにおいて、各社の輸送を組み合わせ、日帰り往復ラウンド運行を実施したものです。相模原工場からの輸送もこのプロジェクトの一部に組み込まれていました。実証実験そのものはドライバーの労働条件改善、実車率・積載効率向上、環境負荷の低減、などの効果が見られ、ホワイト物流推進としても意味のある取り組みとなりました。
今後はこれを本番導入に向けて進めていく必要がありますが、そこで問題となったのが相模原工場の車両待機です。この中継・共同輸送を成功させるには、時間通りに工場で荷積みを行う必要がありますが、本番導入にあたり、時間通りに車両を受け入れる仕組みが相模原工場には整っていなかったのです。
前述の通り、相模原工場は敷地が狭く待機場がない状態です。これまでは先に来た車両から荷積み、荷卸しの作業を行い、順番待ちの車両が敷地に入らなければ周辺を走行してまた順番待ち・・・工場の作業担当者も車両誘導のオペレーションが上手く回らないことに悩んでいました。
そのような状態の中、今回のプロジェクトにより車両待機への対策を迫られたことで、根本的な解決に向けて動き出すことになりました。
「導入実績」「サポート体制」、そして「スピード感ある提案力」
Q.そこで、Hacobuにお声がけいただいたわけですね。ありがとうございます。最終的に、ムーボをお選びいただいた理由についても教えていただけますか。
はい、まず車両待機という課題解決を行うにあたってのステップとして、まず社内外に目的を共有しました。「場内安全確保」と「待機削減」と2つの目的を共有し、工場勤務者や工場で庫内作業を行うパートナー企業とも意識統一を行いました。その上で、受付・予約システムのパートナー選定に移りました。私たちはスピード感を持って、確実に導入するためのパートナーを求めていました。そのためには自分たちで作りこんでいくよりもノウハウを持っている会社、かつ実績がありサポート体制が充実していて、安定・安心のサービスである必要がありましたが、そこに応えていただけるのが、ムーボというサービスだったと考えています。またHacobuのことは、以前あるセミナーで代表の佐々木さんの講演を聴いた時から面白い取り組みをされていると感じており、今回お声がけをさせていただいたという経緯があります。
選定後は社内決裁が比較的スピーディに進みました。一時的にシステム導入や待機場確保などのコストは発生するものの、「安全性」、「持続可能性」を優先させることは、会社の方針に沿った判断だった、ということだと思います。
受付システムを使用し、SMSで呼び出し。同時に待機場を導入
Q.相模原工場では2019年6月からムーボ・バース管理ソリューションを導入いただきました。現在はムーボを利用しどのように業務を進められていますか。
車両待機解決に向けた第一ステップとして、バース管理ソリューションのうち、受付システムを導入するとともに、工場から約1.7km離れた場所に待機場を新たに設置しました。相模原工場で荷積み、荷卸しをする車両はまず待機場に入場していただき、そこからオンラインチェックインもしくは電話受付(ガラケーのドライバー向け)をしていただき、その情報をもとに工場から呼び出しを行うという運用です。
どんな荷物を荷積み、荷卸しをする予定で、車格はこのサイズで・・・といったこれまで予め見えていなかった入場車両情報が見えるようになり、その情報をもとに呼び出しを行うことが出来るようになりました。
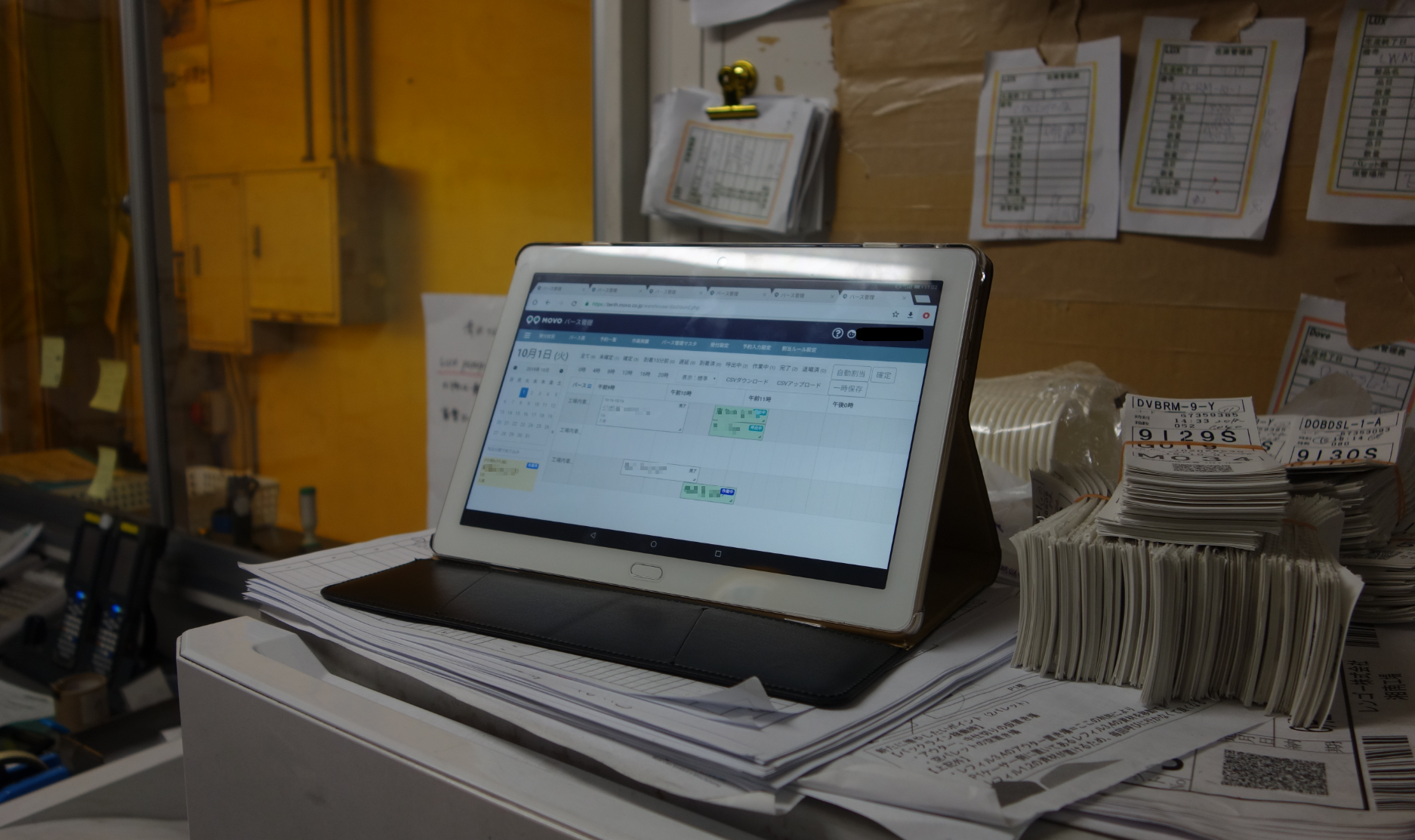
フォークマンが庫内でタブレットを操作し、車両を呼び出し
場所の制約やシステム機能の制約を現場運用設計で解決
Q.受付システムの導入時に苦労された点はありますか。
あります。まず、通常は受付システム導入の際、タブレット運用を行うことが多いと思うのですが、相模原工場はスペースがなくタブレットを置く場所がありませんでした。解決策を模索する際に、オンラインチェックイン※1機能を利用することを提案いただきました。タブレット受付以外の手段があったことで、導入がより現実的になりました。
また、オンラインチェックインは良い機能ではあるのですが、スマートフォンの位置情報機能を使用するためにガラケーでは利用が出来ません。この問題に対しては、庫内作業を委託しているパートナー企業にお声がけし、電話での受付を委託、オンラインチェックインと電話の2つの受付方法を併用することで解決しました。
あとはやはりパートナー企業様の事前周知に時間をかけました。2週間前には現場でドライバーの皆様へチラシを配布し、ドライバー、フォークマン(庫内作業者)、電話受付を担当されているパートナー企業の担当の方に向けてそれぞれマニュアルを作成しました。また、導入初日はHacobuのスタッフの方に現場に張り付いていただきました。そのかいあって、導入後は比較的スムーズに受け入れていただけたという感触があります。
※1:オンラインチェックイン・・・物流拠点から一定半径内(200, 500m, 1, 3, 5, 10kmから選択)に入ったときにはじめて、ドライバーが遠隔操作で携帯電話から受付入場登録できる機能。
当初の目的である「場内安全確保」を達成し、「待機削減」への足掛かりとなる入場車両情報デジタル化を実現
Q.導入後、どのような効果がありましたか。
まず、工場側では「安全を確保できた」「工場前に車両が滞留している状態を解消でき、精神的に楽になった」という声が上がりました。車両が列をなし、場外にも広がりそうである状況は工場勤務者からするとストレスフルな状況だったので、これを解消できたことは本当によかったと工場長からもコメントがありました。
それからドライバーは「こまめに車両を動かす必要がなくなり、接触の可能性が減った」「呼び出しまで休憩が取れるようになった」などポジティブな意見が多く出ました。「待機するとしても、安心して待てるように楽になった」と。
また、フォークマン(庫内作業者)からは「待機車両の入出庫の区別ができ、作業の効率化になった」「バースの遊びがなくなり、限定的ではあるが待機時間の解消が出来た」との声が上がっています。待機解消に大きな効果を発揮するのは予約システム導入だとは思いますが、受付システム導入だけでも車両誘導効率が上がり、待機時間の解消に繋がっています。8月の平均待機時間は24分※2というデータが出ており、以前は待機時間を取得していなかったので単純に比較はできませんが、おおよそ半分くらいには減っているのではないかという実感があります。
「場内安全確保」と「車両待機の解消」に向けて、入場車両の情報をデジタル化し効率的な誘導を行うといった当初の目的については達成が出来ました。今後は第二ステップとして、予約システム導入に向けて取り組みを進めていく必要があります。
※2:現在は待機場からの呼出タイミングを「呼出時刻」としてデータを取得。
「Try First」。スピード感を持って、関係者を巻き込み実現へ
Q.導入が成功したポイントはどのようなことだったとお考えですか。
課題の共有から解決策の実施まで、関係者を巻き込みスピード感を持って進めることが出来たことです。その中で庫内作業を引き受けていただいているパートナー企業との連携も上手く進みましたし、Hacobuからも十分でタイムリーな課題解決提案を都度いただきました。
その前提にあったのは「Try First」のマインドセットです。最初から全ての課題を解決することは出来ないが、段階的に進めることで効果を上げていくことが出来る。その中で最終的に持続可能である物流、サプライチェーンを構築するというゴールに向かっていければいいと考えています。でも最初の一歩はまず始めてみる、ということが重要だと考えています。
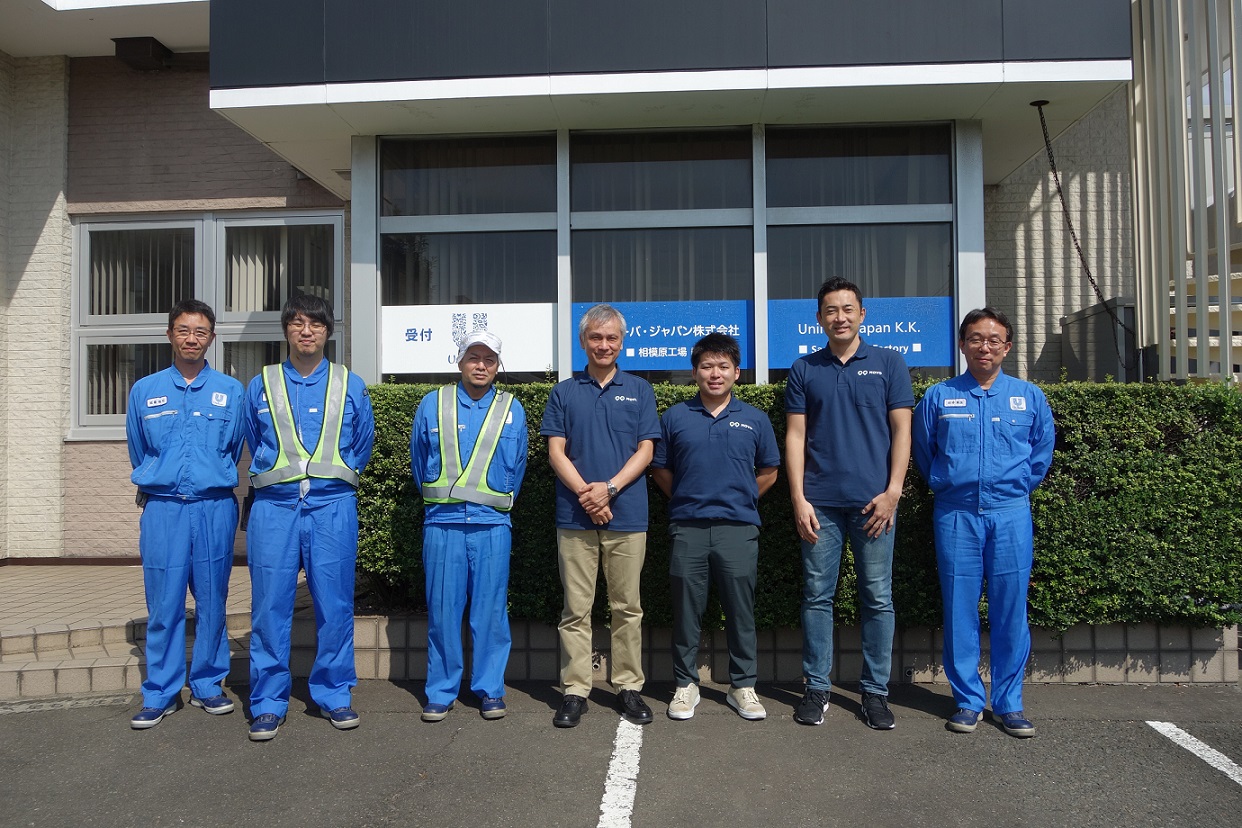
ムーボ導入プロジェクトメンバーの皆様
「ムーボに期待することは、発注情報や積み荷情報と連携したプラットフォーム化」と山下様。期待にお応えできるよう、物流情報プラットフォーム化をムーボは進めてまいります。
ユニリーバ様、ありがとうございました!