順調に伸びる出荷量に事務作業が追い付かない
「MOVO Berth」導入までの経緯を教えていただけますか?
ネスレは近年ペットボトルコーヒーの販売を順調に伸ばし、現在国内シェアはNo.1です。ペットボトルコーヒーは物量が非常に多く、夏場に需要が集中します。ピークシーズンにはトラックが朝一に集中し、待機が発生していました。また、出荷トラック受付には運送会社からの車番情報が必要となりますが、事前にFAXやメール等様々なフォーマットで送られてくる車番情報をエクセルに転記し纏める作業に時間がかかっていました。
視覚的に分かりやすいく、使用イメージが湧く
どのくらいの時間がかかっていたのでしょうか?
1台のトラックを確認するために運送会社に問い合わせる時間を含めると、2-3時間かかる時もあったのではないでしょうか。前日夕方に情報が入ってくるので、ピークシーズンはデータ作成のために残業をすることも多く、確認作業が全体のボトルネックになっていました。また当日受付情報が事前のものと異なる場合には、FAXやメールを探す作業が発生することもありました。
昨年夏はなんとか乗り切ったのですが、今後出荷量が増えていくと考えられる中、事務工数削減のためにシステムを活用する必要があると感じていました。秋頃Hacobuさんとお話をさせていただき、1月には本格導入しました。
もともとMOVOの存在は知っていました。実際に操作をしてみたところ、予約カードをバース表での移動やステータスが一目でわかるところなど視覚的に分かりやすいところがいいなと。また項目の活用方法など柔軟性も高く、使用イメージが湧きましたね。
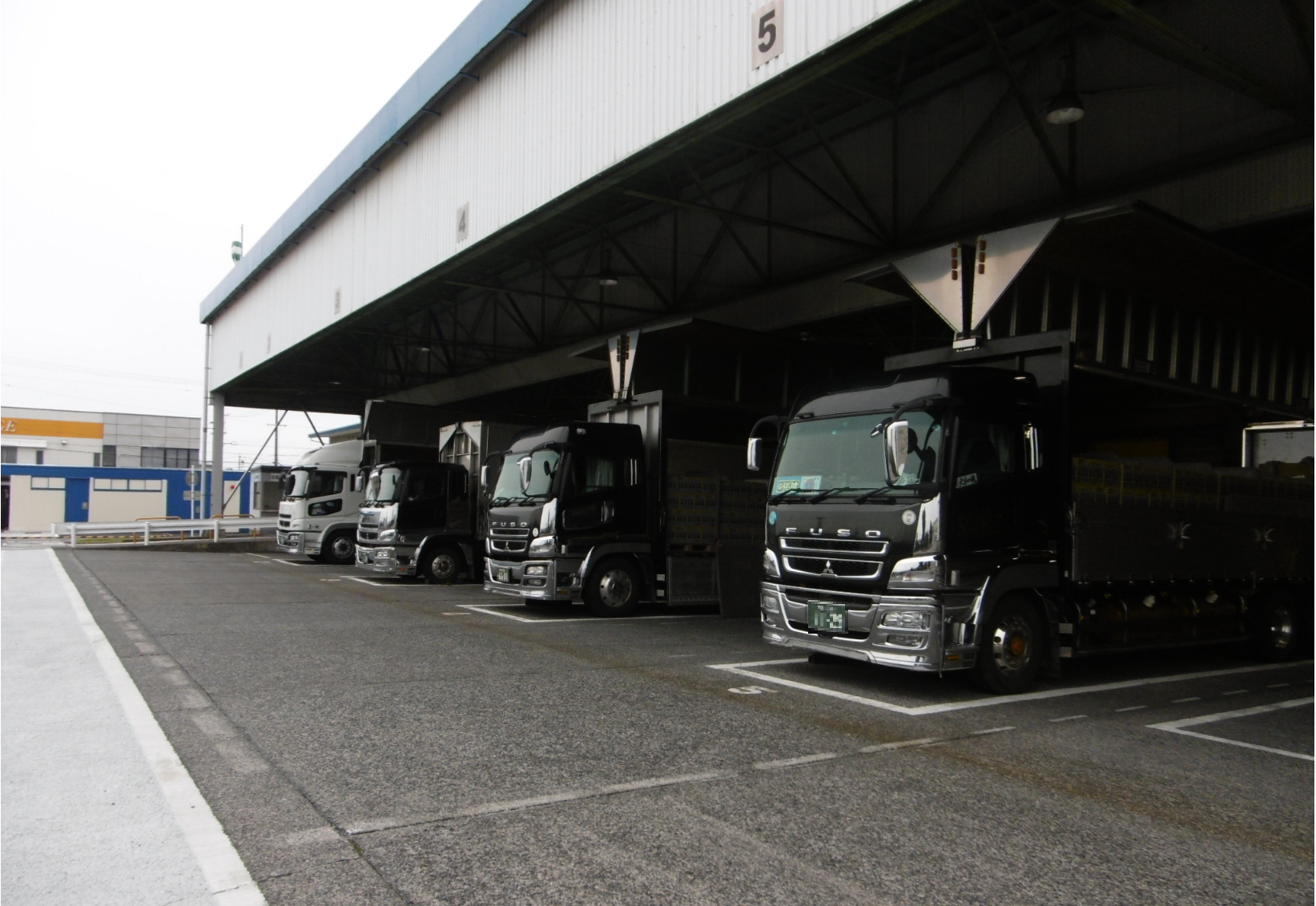
ネスレ日本 島田工場の様子
入出荷すべてのトラックで予約を活用
現在は入出荷ともに予約・受付機能を活用されていますよね。
はい。入荷についてはスタンダードな使い方で、前日までにメーカーや運送会社に予約をしていただき時間を確定、当日は予約時間に入場、トラックバースでタブレット受付をしています。
出荷についても同様の方法で始めたのですが、出荷の場合は到着前に他の仕事が入っていることが多く予約通りに来ることができない、といった声が多かったため途中で運用を変更しました。前日に仮の時間で出荷元運送会社に車番や出荷番号を入力した予約情報を作成してもらい、当日受付時に空いている時間・バースに確定する方法を取っています。
FAXメールを探す手間と混乱がなくなった
導入後は当初の課題は解決されましたか?
入荷については想定通りの運用が実現できました。倉庫担当者もいつどのトラックが入庫するのか事前に把握しているので、それに向けて庫内の準備を進めることができ、効率が上がっています。
出荷については当初とは異なる運用となったものの、効率よく車番と出荷番号を紐づけることが出来るようになりました。FAXやメールを探す手間と混乱が無くなったことが嬉しいですね。
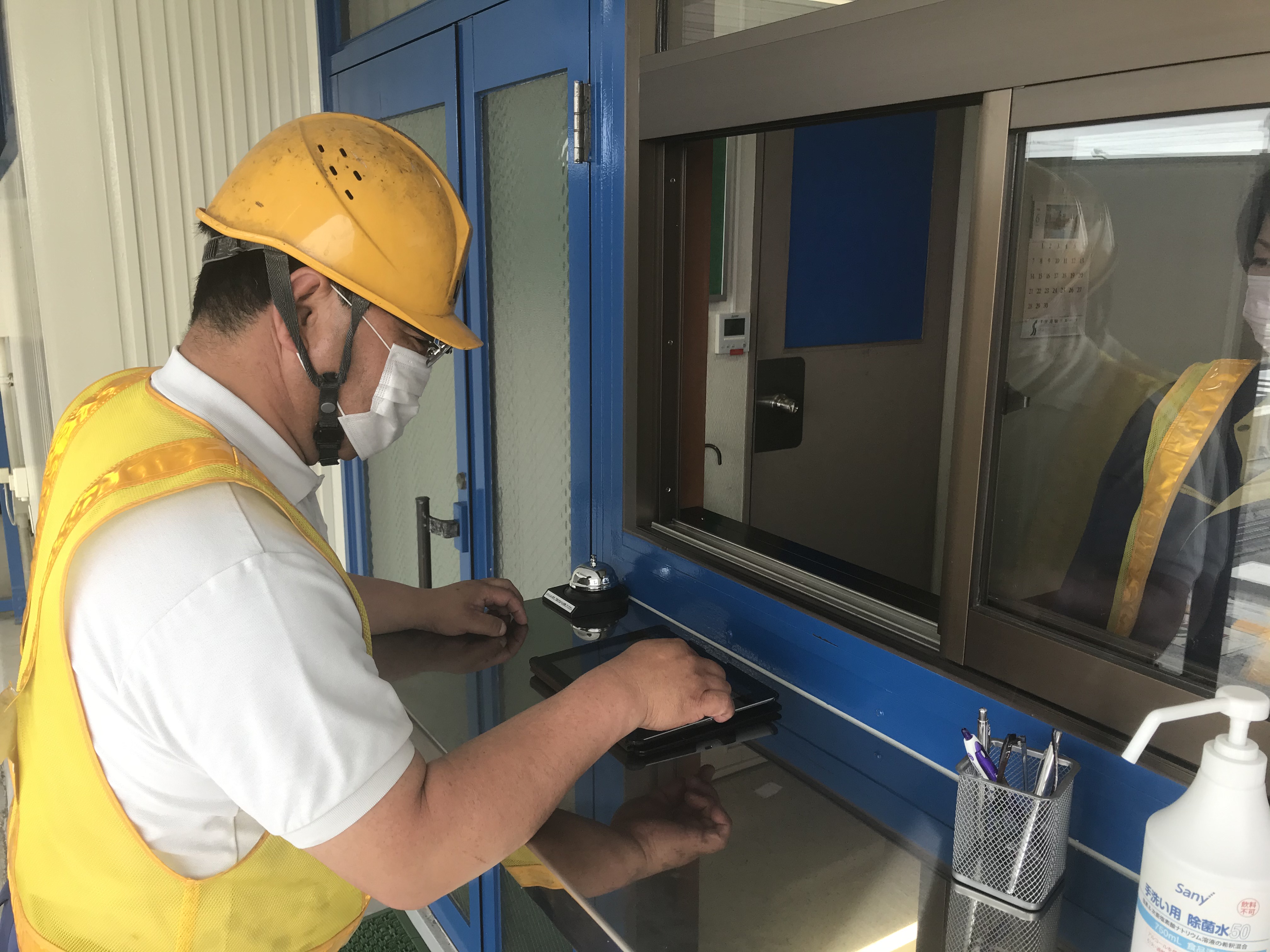
MOVOを使って受付を行う様子(新型コロナ対策として事務所の外側にタブレットを設置、ドライバーとの接触機会を削減)
導入当初は、入荷の路線便の対応に苦労も
導入は上手くいったように聞こえるのですが、苦労したポイントなどはあったのでしょうか?
入荷の路線便の対応に当初は苦労しました。予約対象としていなかったので、作業時間をどう捻出するかを考えました。路線便の到着時間を確認したところ、大体いつも同じ時間帯に来ていることが分かったので、ブロックカード機能を使って予め作業時間を確保することで現在では対応しています。仮にその時間に来なかったとしても、次に待っているトラックを先に呼び出して作業をすれば問題ありません。
一日の入荷のトータル作業台数と時間は予め分かっていますので、その中で状況に合わせて作業順を組み替えています。
運送会社からの問い合わせが減るという思わぬ効果があった
当初期待していたこと以外に何か効果はありましたか?
トラックの作業ステータスが画面で把握できるので、運送会社から状況の問い合わせの電話が入っても倉庫や工場内に問い合わせずに回答ができるようになりました。また、運送会社は予約者IDを持っており、パソコン等でシステムにアクセスすればトラックが着車した後の作業状況をシステム画面から確認してもらうこともできます。これによって、問い合わせ件数自体も減りました。
来年は出荷トラック台数2倍に。データ活用による改善で積込トラック回転率を上げたい
今後MOVOを使って実現していきたいことについて教えてください。
販売好調により、来年は製造能力の増強を予定しています。ピーク時で現在の2倍の出荷トラック台数になる可能性があるため、これまで以上に積込のトラック回転率を上げていく必要があります。
MOVOでは作業ステータスを入力することで作業にかかった時間の分析が可能なのですが、現在のところまだそのレベルには達していません。今後は積込時間を分析し、時間がかかっているトラックとかかっていないトラックのどこに違いがあるのか、データをもとに改善を図り、平均積込時間を短縮していきたいと考えています。まずはデータの取得をきっちりとやっていきます。
ネスレ日本 島田工場では事前のトラック情報確認から当日受付までにかかる事務工数をデジタル化によって削減、更に積込実作業時間の削減に向けて、出荷量増加に向けた体制作りを始めています。「MOVOを使って取得できるデータを活用し更なる改善を図りたい」と森本様の今後の取り組みに関する意気込みが伝わるインタビューとなりました。
森本様、大井様ありがとうございました!